SUS304の切削特性と最適な加工方法
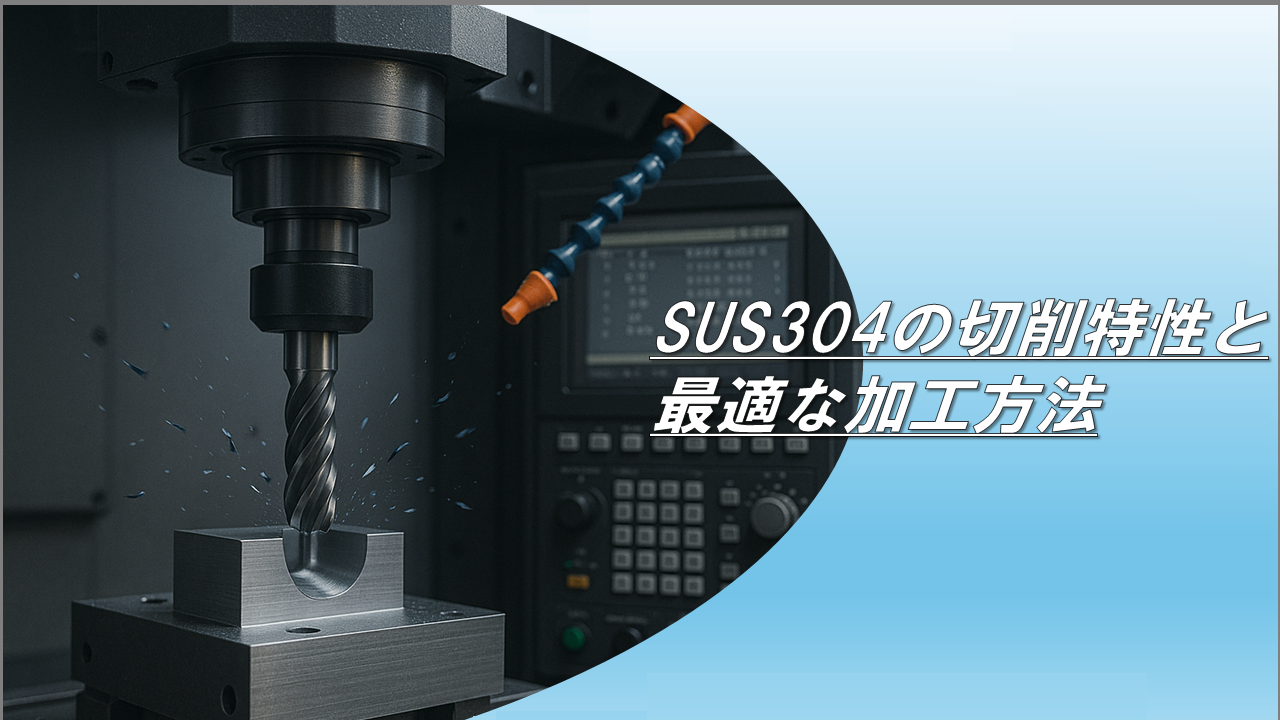
はじめに
ステンレス鋼は耐食性に優れた素材として広く利用されていますが、その中でも特に代表的なオーステナイト系ステンレスである「SUS304」は、建築、自動車、食品機器、化学設備など多岐にわたる分野で使用されています。しかし、SUS304は切削加工において「加工しにくい材料」として知られており、工具の摩耗やビビり、面粗度の悪化、寸法不良などの課題に直面することが少なくありません。本稿では、SUS304の材料特性を整理しつつ、切削時に生じる問題とその対策、そして最適な加工方法について詳述します。
1. SUS304とは?─基本特性の概要
1-1. 化学成分と分類
SUS304はJIS G4303などに規定されたオーステナイト系ステンレス鋼で、主な成分は以下の通りです:
元素 | 含有量(%) |
---|---|
C(炭素) | ≤0.08 |
Si(ケイ素) | ≤1.00 |
Mn(マンガン) | ≤2.00 |
P(リン) | ≤0.045 |
S(硫黄) | ≤0.030 |
Ni(ニッケル) | 8.00~10.50 |
Cr(クロム) | 18.00~20.00 |
このように、CrとNiを多く含むことで高い耐食性と加工性を有しているのがSUS304の特徴です。
1-2. 機械的性質
項目 | 数値(代表値) |
---|---|
引張強さ | 約540 MPa 以上 |
降伏強さ | 約205 MPa 以上 |
伸び | 約40%以上 |
硬さ(HB) | 約160~190 |
延性が高く、加工硬化しやすいという性質が切削に大きな影響を与えます。
2. SUS304の切削における課題
SUS304の切削では以下のような問題が発生しやすく、一般的な鋼材とは異なる配慮が必要です。
2-1. 加工硬化の発生
オーステナイト系ステンレスは切削時に塑性変形を受けやすく、加工硬化が進行します。これにより、切削工具が硬化層に当たって摩耗しやすくなり、刃先が損耗して寿命が短くなります。
2-2. 熱伝導性の低さ
SUS304は熱伝導性が低く、切削時の熱が工具に集中しやすいため、工具温度が上昇しやすいです。これが切削抵抗や工具摩耗の要因となります。
2-3. 切りくず処理の難しさ
延性が高いため切りくずが連続的に発生しやすく、切りくずの巻き付きや再切削を招きやすいです。特に高送りで加工した場合に問題が顕在化します。
2-4. 工具の早期損耗
高い加工硬化性、低熱伝導、切りくず処理性の悪さの複合的な要因により、工具寿命が他の材料と比較して著しく短くなる傾向があります。
3. SUS304切削における最適な加工条件
SUS304の切削を効率化し、工具寿命や加工精度を向上させるためには、以下の点に注意して加工条件を設定する必要があります。
3-1. 切削速度(Vc)
SUS304に対する切削速度は、使用する工具材質によって異なりますが、一般的には次の範囲で設定されます。
工具材質 | 推奨切削速度(m/min) |
---|---|
HSS(高速度鋼) | 10~20 |
超硬工具 | 50~120 |
CBN/セラミック | 120~200(仕上げ切削) |
切削速度が高すぎると加工熱の蓄積が進み、工具摩耗が早くなるため、バランスの取れた速度が求められます。
3-2. 送り速度(f)
過大な送りは工具負荷やビビリの要因になります。仕上げ加工では0.05~0.15 mm/rev程度、荒加工では0.2~0.4 mm/revが目安です。
3-3. 切込み量(ap)
一度に大きく削ろうとすると加工硬化層に対して刃が当たり、摩耗が加速します。荒加工では1~3mm程度、仕上げでは0.2~0.5mm程度が一般的です。
4. 切削工具の選定とコーティング
4-1. 工具材質の選定
SUS304には、次のような工具材質が適しています:
- 超硬合金(Carbide): 高硬度・高耐熱性で、量産に適する
- コーティング超硬: TiAlN、AlCrNなどの耐熱コーティングが有効
- サーメット・セラミック: 仕上げ専用、熱変形に強い
- CBN工具: 仕上げ切削に最適だが高価
4-2. チップ形状
切れ味重視のポジティブ形状チップや、S字形状で切りくず処理性を高めたものが推奨されます。
4-3. コーティング
- TiAlN(チタンアルミナイトライド): 高温下での耐酸化性に優れ、工具寿命を延ばす
- AlCrN(アルミクロムナイトライド): 熱伝導性に優れ、摩耗対策に効果的
5. クーラントと潤滑の活用
SUS304の切削においてクーラントは不可欠です。冷却・潤滑・切りくず排出の3つの観点から適切に使用することで、加工安定性が向上します。
5-1. クーラントの種類
- 水溶性切削油(エマルジョンタイプ): 冷却性が高く、加工熱を抑える
- 不水溶性油: 潤滑性重視。ねじ切りやタップ加工に有効
5-2. 高圧クーラントの導入
高圧クーラントにより切りくずの排出性が向上し、切りくず巻き付きによるトラブルを防止できます。
6. 切削トラブルとその対策
以下は、現場でよくあるトラブルと推奨される対策の一覧です。
トラブル内容 | 原因 | 対策 |
---|---|---|
工具摩耗が早い | 熱集中、加工硬化 | 低速回転、コーティング工具使用 |
ビビりが発生 | 工具剛性不足、切削条件不適 | 剛性の高い工具、送り・切込みの見直し |
寸法不良 | 熱変形、摩耗による刃先の鈍化 | クーラント強化、工具摩耗監視 |
面粗度が悪い | 刃先の欠損、再切削 | シャープな切れ刃使用、切りくず処理 |
切りくず巻き付き | 切りくずの長さ、排出不良 | 高圧クーラント、チップブレーカ付チップ |
7. 加工法別のポイント
7-1. 旋盤加工
工具剛性を重視し、刃先のシャープさを保ったまま、低切削速度・中送りで加工します。チップブレーカ付の超硬チップが有効です。
7-2. フライス加工
上げ刃でなく下げ刃加工を基本とし、加工方向に対して送り方向を逆にして切れ味を安定させます。乾式より湿式が安定しやすいです。
7-3. ボーリング加工
加工熱がこもりやすいため、クーラントは多量に供給します。深穴ではスパイラル加工や高圧クーラント併用が有効です。
7-4. ドリル加工
ねじれドリルの使用が一般的ですが、スパイラル溝+クーラント孔付きドリルが理想的。穴径φ10以下では特に刃先の摩耗に注意が必要です。
8. 加工現場での工夫
現場では以下のような工夫が実際に活用されています:
- 工具寿命をモニタリングして早期交換
- 工具メーカーによる最適切削条件の導入支援
- 機械剛性やクランプの見直しによるビビり対策
- 自社での加工データベース化によるナレッジ共有
おわりに
SUS304は、その高い耐食性や広い用途展開により、重要な材料として多くの製品に使われていますが、切削加工においては難加工材に分類されることが少なくありません。しかし、その切削特性を理解し、適切な工具・条件・潤滑・対策を講じることで、安定した加工と高品質な製品を実現することは可能です。現場での試行錯誤とデータ蓄積により、SUS304加工の最適化が今後さらに進展していくことでしょう。