真鍮加工時の異音・振動の原因とは?
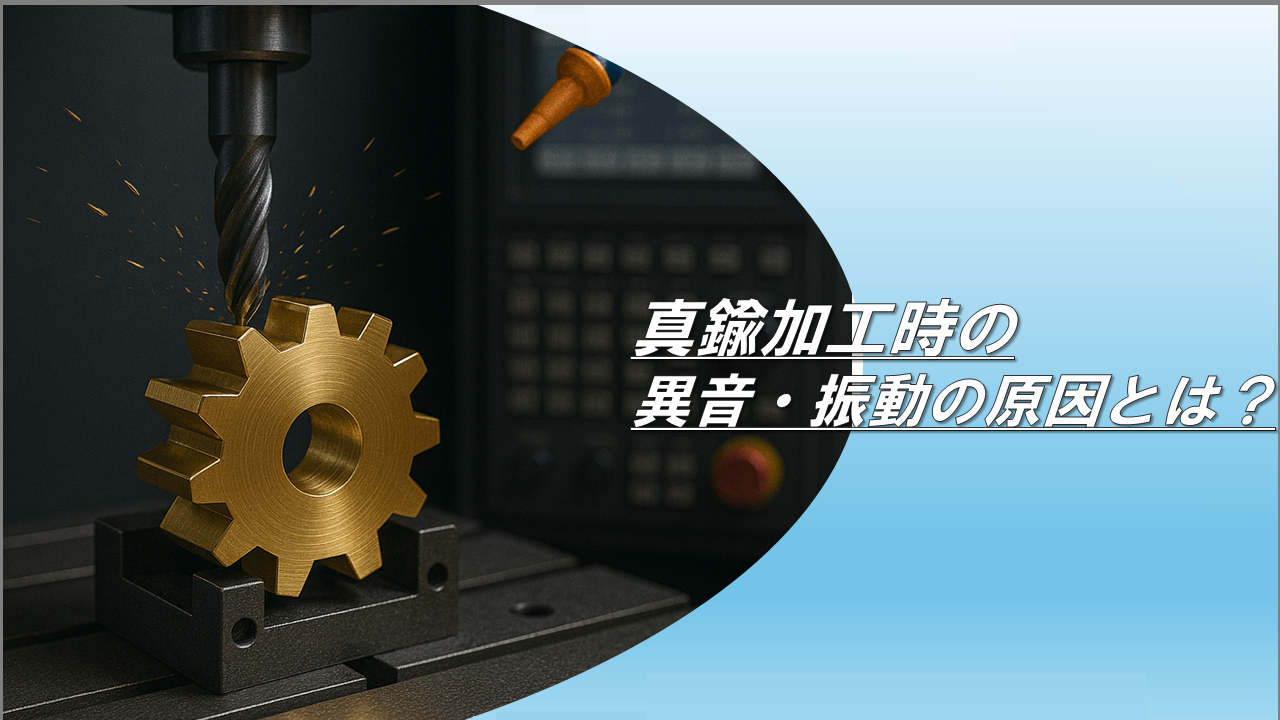
真鍮(黄銅)は切削性に優れた金属材料として、幅広い分野で利用されていますが、加工中に「キーン」という異音や振動(ビビり)が発生することがあります。これらの異常は製品精度や工具寿命を著しく損ねるため、原因を正確に把握し、的確な対策を講じることが重要です。
本記事では、真鍮加工時に発生する異音や振動の代表的な原因と、それぞれの対処法について詳しく解説します。
1. 工具の不適合や摩耗
原因
真鍮は比較的軟らかく加工しやすい材料ですが、刃先が鋭利でないと切削抵抗が不安定となり、異音や振動が発生します。特に以下のような状態の工具は注意が必要です。
- 工具先端の摩耗
- 切れ味の悪い工具材質(例えば過剰に硬質な超硬など)
- 不適切な工具形状(逃げ角不足など)
対策
- 真鍮専用の快削向け工具(刃先が鋭利なタイプ)を使用
- 工具摩耗を定期的にチェックし、早期交換を徹底
- エンドミルやバイトの逃げ角を適正化(真鍮は5〜10度程度が目安)
2. 切削条件の不適正
原因
切削速度(Vc)や送り速度(f)が材料特性に合っていないと、ビビりや共振が発生しやすくなります。例えば、低すぎる切削速度や過剰な送り速度は、加工時に不均一な抵抗を生みます。
対策
- 真鍮の推奨切削速度(150〜300m/min程度)を参考に設定
- 送り速度は工具径や機械剛性に応じて最適化
- 面取りや仕上げ加工では、軽切削と高回転を意識
3. 加工物の固定不良
原因
加工物がチャックやバイスにしっかり固定されていないと、微小な振動が増幅されてビビりにつながります。また、複雑形状や薄肉構造のワークでは、変形による共振が発生しやすくなります。
対策
- ワークの固定具(治具)を見直し、クランプ力を十分に確保
- 複雑形状の場合、段取り変更や支持点の増設を検討
- 振動吸収材やゲルパッドの併用も有効
4. 加工機の剛性不足
原因
機械本体やスピンドルの剛性が不十分だと、加工時の負荷変動に機械が耐えられず、振動が発生します。特に小型NC旋盤や長年使用した汎用フライスなどではこの傾向が顕著です。
対策
- できる限り剛性の高い加工機を使用
- 古い機械の場合、ボールねじや主軸ベアリングの劣化を確認
- 切削条件を控えめに設定し、負荷を分散
5. 工具突き出し量の過大
原因
工具の突き出し量(ホルダーからの長さ)が長すぎると、加工中のたわみや共振が生じやすくなります。特に長尺バイトやドリルでの深穴加工では要注意です。
対策
- 工具突き出しは「必要最小限」が鉄則
- 可能であればショートタイプ工具を採用
- 高剛性ホルダーや振れ補正付きツールを使用
6. 切りくずの処理不良
原因
真鍮は短く砕ける切りくずが出やすい一方で、連続切りくずが発生する条件(送りが少ない、回転が遅い)では切りくずが工具やワークに巻き付き、異音や振動の原因になります。
対策
- 自動切りくず排出機構の利用
- 加工中に定期的なエアブローやクーラント洗浄を実施
- チップブレーカー付き工具の導入
7. 共振現象の発生
原因
加工条件・工具形状・機械の剛性・ワーク形状が特定の「共振周波数」と一致すると、異常な振動(チャタリング)が発生します。これは加工中のビビりの代表例です。
対策
- 切削条件を微調整して共振周波数から外す(回転数の±10%変更など)
- 工具形状や材質を変更して振動モードを変える
- 加工機・チャック部にダンパーや吸振材を装着
まとめ
原因 | 異音・振動の誘発メカニズム | 主な対策 |
---|---|---|
工具の摩耗・不適合 | 切削抵抗が不安定になる | 工具の定期交換、適正な工具形状選定 |
切削条件の不適正 | 共振や不均一切削が発生 | 推奨条件に基づく速度・送りの調整 |
ワーク固定不良 | 微振動が増幅し共振 | クランプ力強化、治具改善 |
機械剛性不足 | 外力に対する耐性が低下 | 剛性の高い機械選定、部品の点検 |
工具突き出し過多 | 工具がしなり共振 | 突き出し量の最小化、高剛性ホルダー使用 |
切りくず処理不良 | 切りくず干渉によりビビり | 切りくず除去対策、適切なチップ形状採用 |
共振現象 | 周波数の一致により増幅 | 回転数変更、ダンパー・吸振対策 |
異音や振動は、放置すると製品の不良や工具破損を招く重大な問題に発展します。真鍮加工は一見トラブルが少ないように思われがちですが、微妙な条件のズレが大きな品質低下を引き起こすこともあるため、日常的な点検と改善意識が非常に重要です。
「加工中に少しでも違和感を覚えたら即確認」を徹底することが、安定した生産品質の第一歩です。