切削時の切りくず詰まりを防ぐ方法 ─ 加工トラブルの未然防止策とは
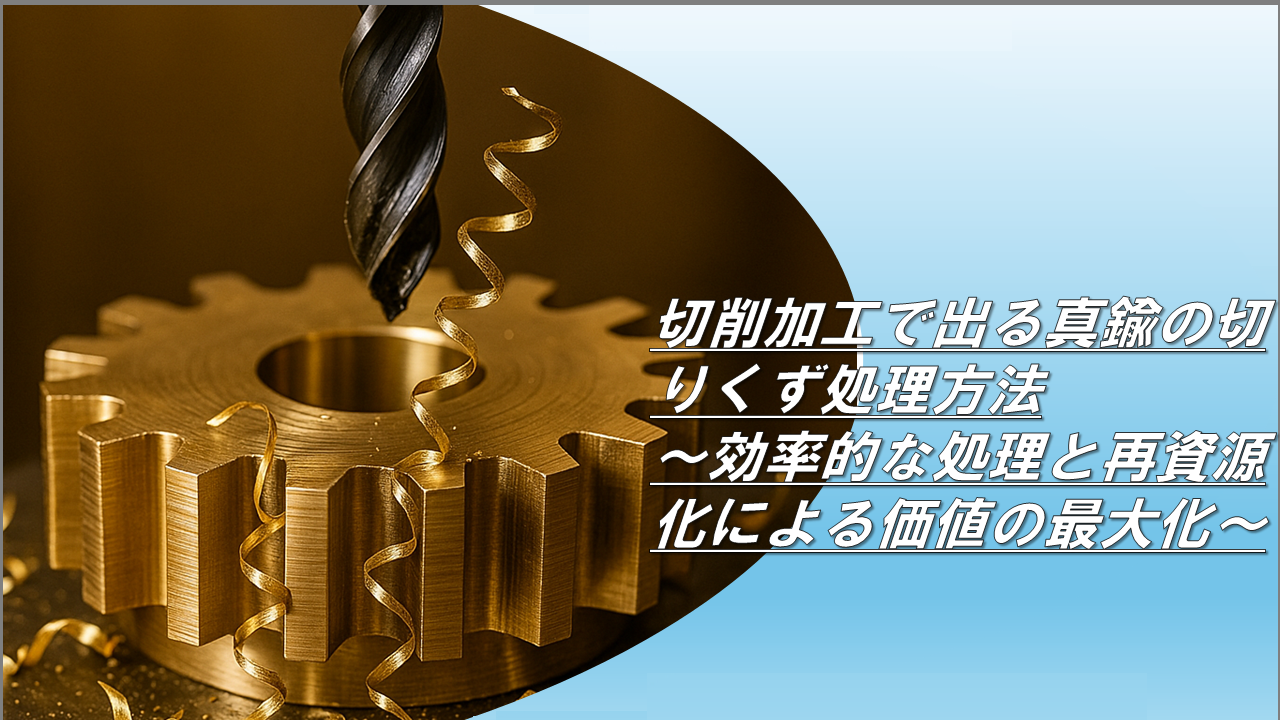
mw2pp0jd6c
CONTENTS
1. はじめに:切りくず詰まりはなぜ問題か?
切削加工では、素材を削り出す際に必ず発生するのが「切りくず(切粉)」です。これが排出されずに工具や加工物に絡みついたり、切削点に再侵入してしまうと、「切りくず詰まり」としてさまざまなトラブルを引き起こします。
- 工具摩耗・欠損の加速
- 加工精度の低下(寸法ずれ・面粗度悪化)
- ワークの焼き付きや傷
- 最悪の場合、設備トラブルによるライン停止
こうした事態を避けるためには、切りくず詰まりの原因を知り、それに対する対策を事前に講じることが極めて重要です。
2. 切りくず詰まりが起きやすい主な原因
原因 | 説明 |
---|---|
切削条件の不適正 | 切削速度や送り量が適正でないと、切りくずが短くならず排出しづらくなる |
工具形状の不適合 | すくい角やチップブレーカーが不適切な工具を使うと切りくず排出が悪化 |
切削材の性質 | ダクタイル鋳鉄、アルミ、真鍮など粘りのある材料は切りくずが絡みやすい |
冷却・潤滑不足 | クーラントが適切に届かないと、熱膨張や粘着により切りくずが残留しやすい |
機内レイアウトの問題 | 切りくず排出方向に障害物があるとスムーズに流れない |
3. 切りくず詰まりを防ぐための具体的な対策
真鍮加工では、材質特性から切削抵抗が低く、連続加工に適している反面、切りくずが細く長くなりやすいという傾向があります。このため、切削条件や工具形状によっては切りくずが排出されずに工作物や工具、機内に絡みつき、詰まりを引き起こすリスクが高くなります。
切りくず詰まりは、刃物のチッピング、加工面への傷、不良品の発生、機械の緊急停止、火災リスクの増加など、多岐にわたる悪影響をもたらすため、事前の予防が極めて重要です。以下に、現場で即実践できる有効な対策を体系的に解説します。
対策①:チップブレーカ付き工具の選定
- 切りくずを**意図的に短く折る構造(チップブレーカ)**を備えた専用工具を使用することで、帯状やらせん状の切りくず発生を大幅に抑制できます。
- 真鍮加工に適したチップブレーカは、すくい角が大きく、切りくずの滑りが良いデザインになっているものを選びましょう。
- 特にC3604のような快削材には、「切れ味重視タイプ」+「強制分断構造」のある刃先形状が効果的です。
対策②:切削条件の最適化
- 切りくずが帯状や長尺になる場合、切削速度(Vc)が高すぎるか、送り速度(f)が小さすぎることが原因となるケースが多く見られます。
- 対策としては以下の調整が効果的です:
調整項目 | 推奨対応 |
---|---|
回転数(Vc) | 過剰に高すぎないよう抑え、切りくず温度上昇を防止 |
送り速度(f) | やや高めに設定して切りくずに厚みを持たせて分断促進 |
切込み量 | 適切な切込み(0.3~0.8mm程度)で負荷を安定化 |
- 最適条件=切りくずが自然に折れて、かつ加工面が安定する条件を試作加工で見つけておくことが重要です。
対策③:クーラントおよびエアブローによる強制排出
- 加工中に発生した切りくずを確実に排出させるためには、切削油の適正供給およびエアブローによる除去が有効です。
- 特に穴あけや深溝加工、バリ取り後の残留切りくずなど、滞留しやすい箇所には、以下の方法が推奨されます:
対策手段 | 内容と効果 |
---|---|
スルークーラント工具 | 穴の内部に切削液を直接噴射し、切りくずの排出を強力に補助 |
エアブローガン | 加工終了後に手動で切りくずを除去(特に薄板・ポケット部に有効) |
加工中のエアブロー制御 | マシン制御で加工中にもエアブローを当てる(オプション機能) |
切削液ノズルの多方向配置 | スピンドル回りやワーク全体に流動性を持たせて詰まりを防止 |
対策④:排出性の高い工具設計を活用
- ドリル、リーマ、ボーリングバーなどの内部加工工具には、切りくず排出経路の確保された特殊設計の工具を使用することで詰まりのリスクが低減します。
- 具体的には:
工具タイプ | 切りくず排出の工夫 |
---|---|
スパイラルドリル | 高らせん角設計で切りくずを強制的に押し上げる |
オイルホールドリル | クーラント通路を内蔵し、油圧で切りくずを押し出す |
面取り工具(多段式) | 切削層を分散させ、切りくず発生量を制御 |
対策⑤:機内清掃・排出システムの整備
- 長時間連続加工を行う現場では、機内に切りくずが蓄積し、それが二次的な巻き付きや詰まりを引き起こすケースが多発します。
- そのため、以下のような切りくず管理インフラの整備も重要です:
設備・機能 | 効果 |
---|---|
スクレーパー式コンベア | 切りくずを自動で機外へ搬出 |
チップフローセンサー | 切りくずの流れ・排出状況を常時監視 |
自動洗浄スケジュール設定 | 加工ごとに機内洗浄・ブロー動作を自動実行 |
切りくずボックスの適正配置 | 切りくず排出口とボックスの位置が一致しているか |
チェックリスト:切りくず詰まり対策の確認項目
チェック項目 | 対応確認ポイント |
---|---|
チップ形状・工具設計 | 分断性・排出性に優れた構造になっているか? |
切削条件 | 切りくずが伸びすぎない条件で運転しているか? |
クーラント供給状態 | 圧力・向き・量は適正か?詰まりやすい部分に届いているか? |
工具・機械内の清掃頻度 | 残留切りくずによる再詰まりを防ぐ習慣があるか? |
機械・ラインの清掃装置の有無 | 自動排出・洗浄装置が機能しているか? |
4. 切りくずの形状で知る!詰まりリスクのサイン
切りくずの形状 | リスク度 | 備考 |
---|---|---|
長く帯状 | 高 | 巻き付き、詰まり、再切削のリスク大 |
細かい破片状 | 低 | 理想的な状態。切りくず排出良好 |
粘着状 | 中~高 | アルミや真鍮で多発。熱の影響を受けやすい |
粉状 | 中 | クーラント不足、摩耗工具が原因の可能性 |
5. 切りくず排出補助の工夫(現場の知恵)
- 機械内部に傾斜をつけた加工テーブル:自然排出を促進
- 定期的なエアブロー・スキマ清掃:切りくずのたまりを防止
- コンベア・チップリフターの点検:搬送不良がないか定期確認
6. 自動化・無人運転における注意点
- 長時間の連続運転では、切りくず詰まりが致命的なトラブルに直結する
- 切りくずセンサーやカメラ監視を導入し、詰まりを即時検知・停止できる体制が重要
- バー材加工などでは、**切りくず排出シュートの工夫(角度・形状)**が効果的
7. まとめ:切りくずは「出し切る」ことが鉄則
切りくず詰まりは、加工精度や工具寿命、ライン稼働率に大きな影響を与える「隠れた敵」です。しかし、工具の選定、切削条件の最適化、冷却の工夫など、基本を押さえた対策によって、確実に抑え込むことが可能です。
トラブルが発生してからの対応ではなく、「切りくずを詰まらせない設計思想と段取り」が、安定加工と高い生産性を生む鍵となります。