真鍮切削で使われる主な工具とその特徴
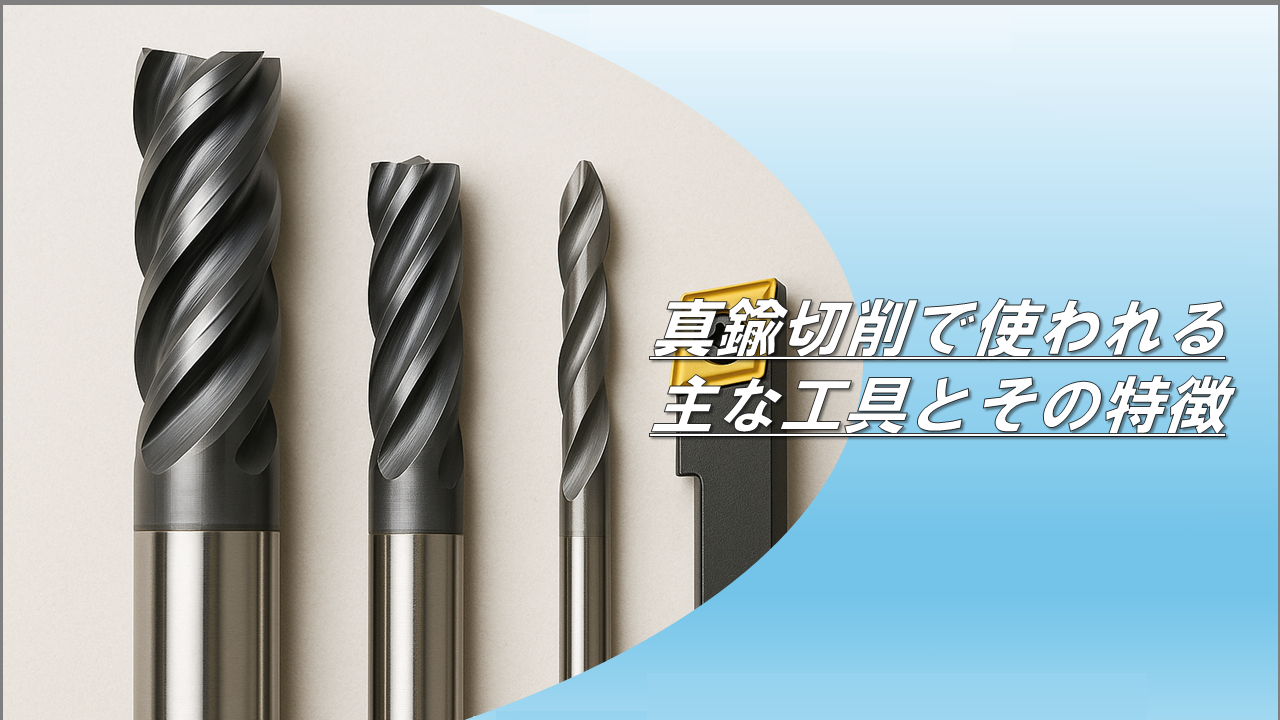
真鍮は加工性に優れた非鉄金属の一つであり、切削加工においても非常に人気の高い素材です。電気・水道部品、装飾品、自動車部品など幅広い分野で使用されており、その美しい光沢と加工のしやすさから、多くの加工現場で日常的に扱われています。本記事では、真鍮の切削に使用される代表的な工具とその特徴について解説します。
1. 真鍮の切削に適した理由
まず、真鍮が切削加工に適している理由を簡単に整理します。
- 靭性が低く、加工中の変形が少ない
- 被削性が高く、バリや溶着が少ない
- 熱伝導性に優れ、熱による変形が少ない
- 加工中に発生する切りくずが細かく処理しやすい
これらの特性から、真鍮はアルミやステンレスに比べて工具摩耗が少なく、切削条件を高めに設定できる素材とされています。
2. 真鍮切削に使用される主な工具種
真鍮の被削性は極めて高いため、工具選定においては「過剰な性能」よりも「コスト効率」や「加工目的に応じた適正選定」が重視されます。以下では、代表的な工具材質別にその特徴や適用シーン、さらに近年のトレンドも交えて詳述します。
2-1. 超硬工具(超硬合金:Carbide)
概要:
超硬工具はタングステンカーバイド(WC)とコバルト(Co)を主成分とする焼結材で、高硬度・高耐摩耗性を有するため、真鍮加工において主力となる工具種です。
特徴とメリット:
- 高速回転・高送りに対応し、高能率加工が可能
- 工具寿命が長く、段取り時間や交換頻度を削減
- 切れ味を維持したまま、加工面の面粗度も安定
- 自動旋盤やCNC旋盤において、量産用途での実績多数
推奨シーン:
- 旋削加工におけるチップ式バイト
- 高回転でのフライス加工(エンドミル使用)
- 切削抵抗を抑えたい中〜高精度穴加工
注意点:
超硬は割れに弱いため、衝撃のある加工(断続切削や細径工具)には不向き。その場合は次項のハイス工具を検討します。
2-2. ハイス工具(高速度鋼:HSS)
概要:
ハイスはタングステン、モリブデンなどを含む耐熱鋼で、粘り強く、再研磨性に優れています。加工速度は超硬に劣るものの、柔軟性や加工安定性で根強い需要があります。
特徴とメリット:
- 刃先が欠けにくく、衝撃に強い
- 手動や中低速加工でも安定性が高く、加工ミスを防止
- 形状自由度が高く、特殊形状・カスタム刃物の製作が容易
- 再研磨で繰り返し使用可能なためコストパフォーマンス良好
推奨シーン:
- 小径穴あけや細穴加工(Φ3mm以下)
- 手動ボール盤やフライス盤での加工
- タップ加工やリーマ加工(ねじ精度重視)
注意点:
高温下で摩耗しやすいため、水溶性切削油などの冷却管理が重要です。
2-3. コーティング工具(TiN, TiAlN, DLCなど)
概要:
コーティング工具は、超硬やハイスなどの母材に耐摩耗性・耐熱性を高めるためのコーティングを施したもので、表面改質による性能向上を図る手法です。真鍮加工では特に摩擦係数を下げることが重視されます。
主なコーティングとその特徴:
コーティング種 | 特徴 | 真鍮への適正 |
---|---|---|
TiN(チタンナイトライド) | 黄金色。汎用性が高く、耐摩耗性に優れる | ◎ |
TiAlN(チタンアルミナイトライド) | 耐熱性が高く、鉄系に向くが真鍮でも可 | ○ |
DLC(ダイヤモンドライクカーボン) | 超低摩擦で切りくずの排出性抜群 | ◎ |
メリット:
- 工具寿命が向上し、工具交換頻度の削減
- 摩擦低減により、バリ・溶着の発生を抑制
- 切りくず排出性が向上し、加工面の清浄性が安定
注意点:
コーティング層が摩耗すると性能が一気に低下するため、使用限界の見極めが重要。また、真鍮の種類によってはコーティング効果が薄れる場合もあります(鉛フリー系など)。
2-4. 固定刃・インサート式工具
概要:
旋削バイトやフライスカッターに多用されるインサート交換式工具は、真鍮加工でも主力の座を占めます。摩耗部のみを交換できるため、トータルのコスト低減に有利です。
メリット:
- インサート(チップ)の交換だけで済むためランニングコスト削減
- 材質や形状のバリエーションが豊富で、加工用途に応じた最適化が可能
- 自動盤や量産機において工具寿命の可視化がしやすい
注意点:
インサート固定部の剛性が不足するとびびりや加工精度低下の原因となります。しっかりとしたホルダー選定が肝要です。
2-5. ダイヤモンド工具(PCD・単結晶)
概要:
多くは高硬度材料向けですが、鏡面仕上げや超高精度な真鍮加工ではPCD(多結晶ダイヤモンド)や単結晶ダイヤモンド工具が選ばれる場合もあります。
特徴:
- 抜群の切れ味と耐摩耗性
- 面粗度Ra0.1以下の光学仕上げが可能
- 溶着・バリの発生が極小
用途例:
- カメラ部品・医療機器などの外観部品
- 鏡面加工・精密金型の母材仕上げ
注意点:
非常に高価なうえ、断続切削や高送りには不向き。用途は限定されます。
以上のように、真鍮切削に使用される工具は、その加工目的・量産条件・設備構成により使い分けが必要です。単に「硬い工具を使えば良い」という発想ではなく、「材料特性に合った切削特性を持つ工具を選定する」ことが、加工精度・コスト・効率の最適化につながります。
2-1. 超硬工具(超硬合金)
特徴:
超硬工具は、タングステンカーバイドなどの硬質素材で構成されており、高硬度・高耐摩耗性を有します。真鍮のように被削性の高い材料に対しては、工具寿命が長く、高速切削にも対応可能です。
利点:
- 高速切削が可能(回転数・送り速度を高めに設定できる)
- 工具寿命が長く、段取り回数を減らせる
- 真鍮特有の「溶着」のリスクが少ない
代表的な用途:
旋削バイト、エンドミル、ドリルなど、汎用的な切削工具として広く利用されます。
2-2. ハイス工具(高速度鋼)
特徴:
HSS(High Speed Steel)とも呼ばれるハイス工具は、鋼をベースにした耐熱合金で構成されており、刃物の粘り強さに優れています。超硬ほどの硬度はないものの、価格が比較的安価で、研磨による再利用も容易です。
利点:
- 刃先が欠けにくく、小径工具や精密加工に向く
- 手仕上げや低速加工でも安定した切削が可能
- 成形自由度が高く、特殊形状の工具が作りやすい
代表的な用途:
小径ドリル、タップ加工、リーマ加工などで利用されます。手動加工機や細かい寸法精度が求められる場面でも活躍します。
2-3. コーティング工具
特徴:
切削工具の表面にTiN(チタンナイトライド)やTiAlN(チタンアルミナイトライド)などの皮膜を施したものです。真鍮のように溶着しにくい材料であっても、工具寿命をさらに延ばす目的でコーティングが施されます。
利点:
- 工具の耐摩耗性・耐熱性を向上
- 摩擦係数を下げ、切りくずの排出性が良くなる
- 工具寿命の安定化に貢献
代表的な用途:
旋削用バイト、フライス工具、ドリルなど、超硬工具との組み合わせで使用されるケースが多いです。
3. 用途別:真鍮切削における代表的な工具とその選定ポイント
加工内容 | 使用工具 | 推奨工具種 | 特徴・注意点 |
---|---|---|---|
外径旋削 | 旋削バイト | 超硬工具+TiNコート | 高速加工可能。刃先の鋭利さに注意 |
内径加工 | 内径バイト | ハイスまたは超硬 | 細径工具はハイスのほうが割れにくい |
穴あけ | ドリル | 超硬またはハイス | 切りくず排出の良い2枚刃推奨 |
ネジ切り | タップ | HSSタップ | 低速加工が望ましく、タップ下穴精度が重要 |
フライス加工 | エンドミル | 超硬エンドミル+コーティング | 切れ刃数の多いタイプが推奨 |
面取り加工 | 面取りカッター | 超硬またはハイス | チップタイプでも可 |
4. 真鍮切削における工具選定のポイント
4-1. 鋭利な切れ刃が必要
真鍮は塑性変形が起きにくい一方で、切れ味が鈍るとバリの発生や面粗さの悪化につながります。したがって、刃先のシャープさが重要であり、定期的な再研磨や交換が推奨されます。
4-2. チップブレーカは不要または簡易でOK
鉄系材料とは異なり、真鍮は切りくずが自然に短く切れやすいため、チップブレーカの機能がなくても支障は少ないです。逆に複雑な形状のチップブレーカが干渉して加工面を荒らすこともあります。
4-3. コストパフォーマンスの最適化
真鍮の加工では、工具の消耗が比較的少ないため、高価格帯の工具よりも、安価で高頻度に交換する戦略が有効なこともあります。量産ラインではこのバランスが重要です。
5. 真鍮の種類と工具適正の違い
真鍮にはさまざまな種類があり、切削工具の相性も異なります。
真鍮の種類 | 特徴 | 推奨工具タイプ |
---|---|---|
C3604(快削黄銅) | 被削性が非常に高い | 超硬+TiNコートで高速加工 |
C2700(黄銅二種) | 一般的な加工性 | ハイス工具で十分対応可能 |
C3771(鍛造用黄銅) | やや硬め | 超硬工具が望ましい |
RoHS対応真鍮(鉛フリー) | 被削性が低下傾向 | 鋭利な刃先・高剛性が必要 |
6. おわりに
真鍮の切削加工は、比較的低コストかつ高精度に行えるため、多くの製造業で利用されています。適切な工具の選定により、加工品質を向上させるだけでなく、加工時間の短縮や工具寿命の延長といった生産性向上にも寄与します。素材特性を正しく理解し、加工条件に合った工具を使用することが、高効率な真鍮加工の鍵となるでしょう。