真鍮切削における最適な工具選定と条件設定
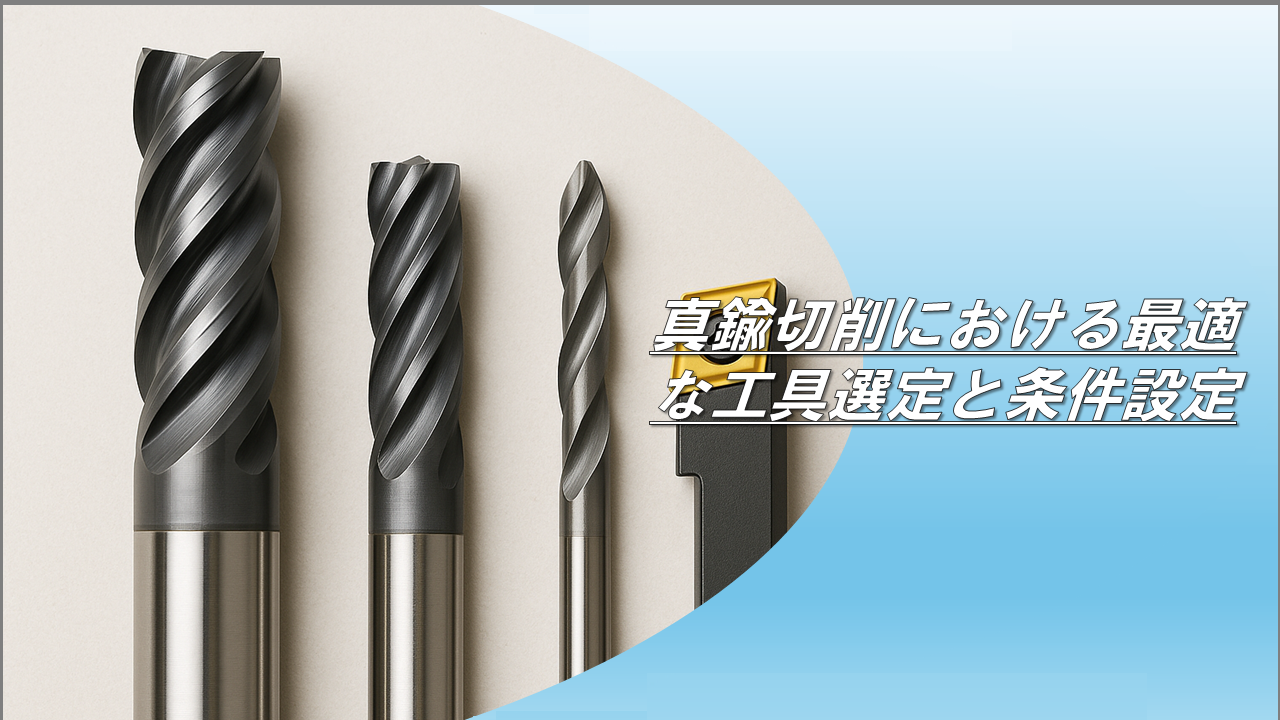
はじめに
真鍮(しんちゅう)は銅と亜鉛の合金であり、その優れた加工性、耐食性、導電性などから、機械部品、電気部品、水栓金具など多くの分野で使用されています。中でも、快削性に優れたC3604などの快削真鍮は、切削加工に最適な材料として知られています。
しかし、真鍮は軟らかい反面、工具との反応や熱の影響によって切削面の品質や工具寿命に影響を及ぼすこともあります。この記事では、真鍮の切削における最適な工具の選定方法と、条件設定のポイントを詳しく解説します。
1. 真鍮の切削特性
真鍮は以下のような切削特性を持っています:
特性項目 | 内容 |
---|---|
切削抵抗 | 低い(鉄系材料に比べて30〜50%程度低い) |
熱伝導性 | 高い(切削熱が工具に集中しにくい) |
ワーク硬度 | 低〜中程度(HB80〜HB180程度) |
被削性 | 非常に良好(快削材ではさらに向上) |
溶着性 | やや注意が必要(軟質真鍮では工具溶着のリスクあり) |
2. 最適な工具材料の選定
真鍮の切削には、その被削性の高さを最大限に活かすために、高精度な工具材料の選定が不可欠です。特に量産加工や自動盤での使用では、工具寿命と加工面品質の両立が求められます。以下に代表的な工具材料と、それぞれの特徴・適性について詳述します。
2-1. 超硬合金工具(Carbide Tool)
真鍮加工において最も一般的で推奨されるのが**超硬合金(セメントカーバイド)**です。
- 推奨グレード:K種(ISO分類でK10〜K20程度)
- 硬度と靭性のバランスに優れ、非鉄金属加工に適しています。
- 適応領域:旋削、フライス、穴あけ、溝入れなど幅広く対応
- メリット:
- 高速加工に対応可能(高回転数での切削でも安定)
- 摩耗に強く、長寿命
- 加工面の仕上がりが良好
- 注意点:
- 工具欠損(チッピング)を防ぐため、送りと切込み深さは過剰にならないように調整が必要
2-2. 高速度鋼工具(HSS)
高速度鋼(ハイス、HSS)工具は、超硬よりも安価で汎用性が高く、小ロット生産や試作加工で活用されます。
- 適応領域:主に旋盤やボール盤、卓上フライスなどの汎用機械
- メリット:
- 刃付け・再研磨がしやすく、メンテナンス性に優れる
- コストが低いため初期投資を抑えられる
- デメリット:
- 耐熱性・耐摩耗性が超硬に劣る
- 高速回転や長時間の連続加工には不向き(摩耗が早い)
2-3. ダイヤモンド工具(PCD・単結晶)
高精度加工や微細切削、鏡面仕上げが必要な場面では、ダイヤモンド工具(PCDまたは単結晶)が検討対象となります。
- 適応領域:
- カメラ部品、医療機器、電子部品などの微細精密加工
- バリゼロ・Ra0.2μm以下の高精度表面が求められる場面
- メリット:
- 圧倒的な耐摩耗性、長寿命(特に量産ラインで有効)
- 加工面が極めて美しく、仕上げ工程を簡素化できる
- デメリット:
- 工具コストが非常に高い
- 衝撃に弱く、欠損リスクがあるため加工条件の厳守が必須
- 再研磨が困難、使い切り前提
2-4. セラミック・CBN工具(補足)
真鍮のような非鉄金属にはセラミックやCBN(立方晶窒化ホウ素)工具は基本的に適しません。これらは硬度の高い鋼材向けに設計されており、真鍮のような軟質素材に使うと切れ味の低下や欠損が発生しやすくなります。
【工具選定の早見表】
工具材種 | 加工適性 | 対応速度域 | 寿命 | コスト | 推奨用途 |
---|---|---|---|---|---|
超硬合金(K10〜K20) | ◎ | 高速域 | ◎ | △ | 全般、量産、自動盤 |
HSS(高速度鋼) | ◯ | 低〜中速域 | △ | ◎ | 試作、小ロット |
PCD/単結晶ダイヤ | ◎ | 高速域 | ◎◎ | × | 高精度仕上げ、微細加工 |
セラミック/CBN | × | 高速域 | ◎ | △ | (真鍮には不適) |
2-5. 工具選定の実務的なポイント
- 量産 or 試作?
- 量産なら超硬が基本。長寿命で工具交換頻度も減らせる。
- 試作や個別対応品なら、再研磨可能なHSSも有効。
- 仕上げ重視 or コスト重視?
- 鏡面仕上げが必要ならPCD系工具を検討。
- コスト最優先なら、汎用超硬またはHSSで対応し、送りと回転を最適化。
- 使用機械の剛性と精度に合わせる
- 高剛性のNC旋盤やマシニングでは超硬やPCDが使いやすい。
- 汎用機や低剛性の設備では、工具欠損リスクを避けてHSSを選定する。
このように、真鍮切削では「どのような設備で、どのような目的で加工するか」によって最適な工具材料は変わります。工具寿命、加工品質、コストのバランスを見ながら、状況に応じた選定が重要です。
2-1. 超硬工具(Carbide)
真鍮の切削には超硬合金工具が第一選択です。特に高い耐摩耗性と耐熱性を備えており、長寿命と高精度を両立できます。
- おすすめ材種:K種超硬(ISO分類でK10〜K20)
- 利点:
- 摩耗に強い
- 微細加工でも刃先強度を保ちやすい
- 自動盤などの連続切削にも対応
2-2. ハイス工具(HSS)
コストを抑えたい場合や小ロット品、非量産品ではハイス鋼(高速度工具鋼)も有効です。
- 利点:
- 安価で再研磨可能
- 複雑形状の工具も製作しやすい
- 欠点:
- 工具寿命が短く、高速回転では焼き付きやすい
2-3. ダイヤモンド工具(PCD/単結晶)
真鍮自体は非鉄金属であり、**ダイヤモンド系工具(PCD/天然単結晶)**も適用可能です。ただし、一般的には高価であり、微細加工や高精度仕上げ用途に限定されます。
3. コーティングの有無と選定
3-1. 無コーティングが基本
真鍮は軟質金属で熱伝導率も高いため、通常は無コーティング工具が適しています。コーティングによって切れ味が鈍化し、バリ発生や加工面の粗れの原因となる場合があります。
3-2. 必要に応じてTiNなど
大量生産や自動盤での長時間連続運転を行う場合は、**TiN(チタン窒化物)**などの薄膜コーティングが有効なケースもあります。主に工具寿命を延ばす目的で使用されます。
4. 工具形状と刃形の最適化
4-1. ポジティブ刃形が基本
真鍮は軟質であり、加工中の切削抵抗を小さく保つために、ポジティブ(前向き)すくい角の刃形が望ましいです。
項目 | 推奨値 |
---|---|
すくい角 | +10〜+20度 |
逃げ角 | 5〜10度 |
先端R | 0.1〜0.4mm程度(仕上げ重視) |
4-2. 鋭利な刃先を維持
真鍮はバリが出やすいため、鋭利な切れ刃が不可欠です。磨き仕上げがされた刃先(ミラーフィニッシュ)が有効です。
5. 切削条件の設定(回転数・送り・切込み)
以下はC3604快削真鍮を例とした基本的な条件の目安です。
加工方法 | 切削速度(Vc) | 回転数(n) | 送り速度(f) | 切込み深さ(ap) |
---|---|---|---|---|
旋削 | 100〜300 m/min | 3000〜8000 rpm(φ20基準) | 0.05〜0.2 mm/rev | 0.2〜2.0 mm |
フライス | 150〜400 m/min | 6000〜12000 rpm | 0.02〜0.1 mm/tooth | 0.1〜2.0 mm |
ドリル加工 | 50〜100 m/min | 1000〜3000 rpm(φ10基準) | 0.05〜0.2 mm/rev | 穴径による |
※回転数は加工機の剛性や冷却能力、工具寿命を考慮して調整してください。
6. クーラントと切削油の使用
6-1. 水溶性切削液
加工熱を抑えるために水溶性クーラントの使用が基本です。特に自動盤などで連続運転を行う場合には、濃度管理が重要です。
6-2. オイルミストやドライ加工
短時間の加工やバリ取り加工ではドライ切削やオイルミストも効果的。加工環境に応じて選定します。
7. 加工不良を防ぐための注意点
トラブル例 | 原因 | 対策 |
---|---|---|
バリの発生 | 鈍った刃先・過度の切込み | 鋭利な刃物を使用、送り速度を適正化 |
工具摩耗 | 不適切な工具材・高温加工 | 超硬工具の選定、クーラント強化 |
チッピング | 逃げ角不足・衝撃負荷 | 工具形状最適化、送り速度の見直し |
8. 加工事例:C3604部品のフライス加工
- 材料:C3604(快削真鍮、JIS H3250)
- 工具:超硬エンドミル φ6mm(無コート、2枚刃、ポジティブ形状)
- 加工機:立形マシニングセンタ
- 条件:Vc=250 m/min、n=13200 rpm、f=0.06 mm/tooth、ap=0.5mm
- クーラント:水溶性クーラント(5%濃度)
- 加工時間:約8分
- 結果:面粗度Ra=0.6μm、バリ無し、工具摩耗少なし(100個加工後)
まとめ
真鍮の切削は一見簡単に見えますが、適切な工具選定と条件設定によって、加工精度、工具寿命、生産性が大きく左右されます。特にC3604などの快削材は高い加工効率を発揮できますが、刃先形状や切削条件の微調整によって不良リスクをさらに減らすことが可能です。
以下のポイントを押さえておくと、真鍮切削の品質と効率が向上します:
- 工具は超硬+ポジティブ刃形が基本
- コーティングは無またはTiN薄膜程度にとどめる
- 高回転・低送りを意識しつつ、切込みは適度に
- バリ・摩耗対策には刃先管理と切削液が重要