切削加工における工具摩耗の原因と対策
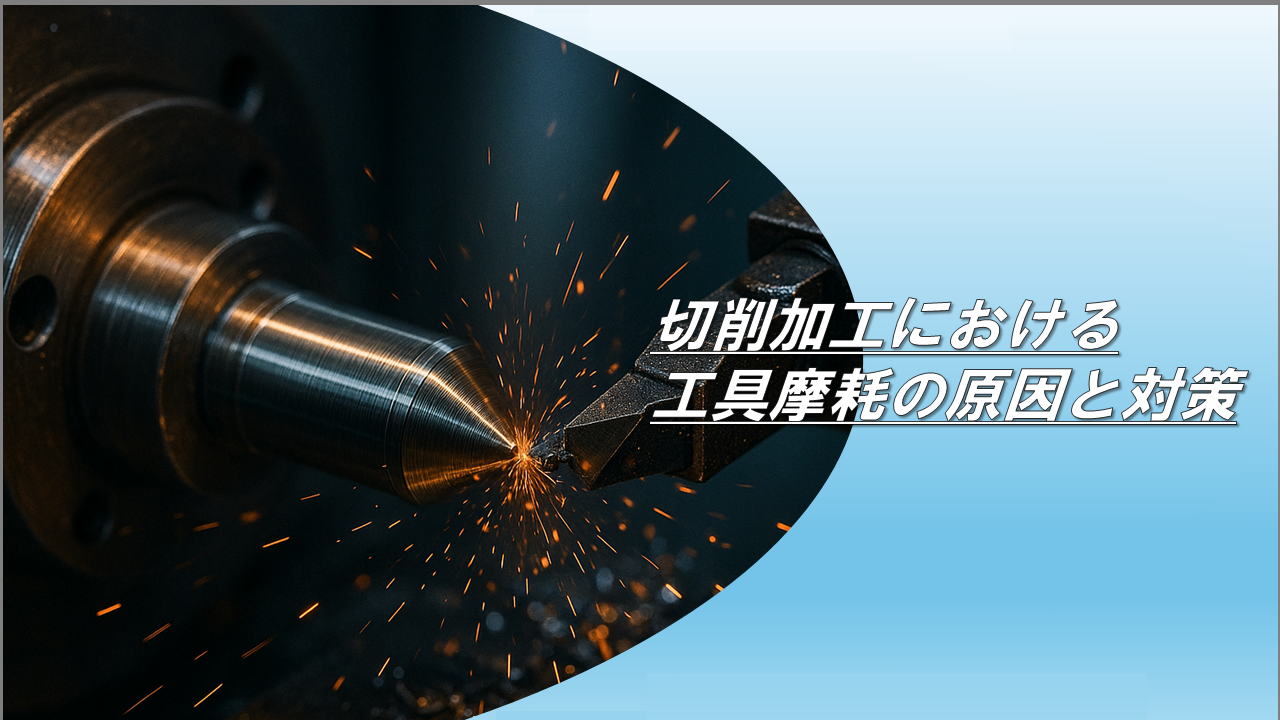
はじめに
切削加工では、工具の摩耗は避けて通れない現象です。工具摩耗が進行すると、加工精度の低下や表面粗さの悪化、最悪の場合は工具破損による設備停止やワークの不良につながります。そのため、摩耗のメカニズムを理解し、適切な対策を講じることが高精度・高効率な加工を維持する鍵となります。
本記事では、切削工具の摩耗の主な種類と原因、さらに具体的な対策について詳しく解説します。
工具摩耗の主な種類と特徴
切削工具に発生する摩耗は、発生箇所やメカニズムによって分類されます。以下は代表的な摩耗形態です。
摩耗の種類 | 発生箇所 | 特徴・影響 |
---|---|---|
フランク摩耗 | 刃の後面(フランク面) | 加工面粗さの悪化・寸法精度低下 |
クレーター摩耗 | 刃の前面(すくい面) | 切削抵抗の増大・工具破損の原因 |
ノッチ摩耗 | 切りくず出口付近 | 不安定な切削・ビビリの発生 |
端部摩耗 | 刃先やコーナー部分 | 微細な欠けやチッピングが進行 |
熱摩耗 | 高温部全体 | 工具材質の軟化・塑性変形により工具形状が変化 |
アブレシブ摩耗 | ワーク材との摩擦面 | 研磨作用による滑らかな摩耗痕、工具寿命短縮 |
工具摩耗の主な原因
工具摩耗の原因は多岐にわたりますが、大きく分けると以下の要因が挙げられます。
1. 高温による熱的要因
切削中には工具先端が非常に高温になります。特に硬い材料や高速切削時には700~1000℃を超えることもあり、工具材質が熱によって軟化しやすくなります。これが摩耗やチッピングを加速させる要因となります。
2. 高切削抵抗による機械的要因
切削条件が過酷である場合、工具にかかる力が大きくなり、摩耗や破損が生じやすくなります。特に送り速度や切込み深さが大きすぎると、工具寿命が著しく短くなります。
3. ワーク材との相性(化学的要因)
一部の難削材(ステンレス、チタン、耐熱合金など)は、切削中に工具材質と化学反応を起こしやすく、工具表面の被膜を劣化させることで摩耗が促進されます。
4. 切削油剤・潤滑不良
切削油が不足していたり、適切な種類が使われていなかったりすると、冷却効果や潤滑効果が不十分となり、熱的・摩擦的な摩耗が進行しやすくなります。
5. 不適切な工具選定・加工条件
加工条件に対して工具材質やコーティングが合っていないと、摩耗が早期に発生する場合があります。特に、高硬度材や繊維強化樹脂などの特殊素材加工では注意が必要です。
工具摩耗の対策方法
工具摩耗の対策方法(詳細解説)
工具の寿命延長と加工品質の安定を目指すために、摩耗対策は多面的に取り組む必要があります。ここでは、現場で実践可能な対策について、より具体的に深堀りして解説します。
1. 適切な切削条件の設定(加工の基本最適化)
切削条件は、摩耗抑制の第一歩です。ワーク材質・工具材質・加工目的に応じて、条件設定を見直す必要があります。
対策の詳細:
- 切削速度(Vc):摩耗速度と密接に関係します。特にクレーター摩耗は高速度で進行しやすいため、硬質合金では100〜250 m/min、超硬工具では材質に応じて50〜200 m/minを目安に調整。
- 送り速度(F)と切込み(ap・ae):過大な送りや切込みは工具負荷を増やし、ノッチ摩耗や刃先破損の原因になります。適切な負荷率を保つには、1刃当たりの送り量(fz)にも配慮が必要。
- 切りくず排出:切りくずが逃げにくい条件(小径工具・深穴加工など)では、切りくず噛み込みによる摩耗や破損が発生しやすいため、切りくず形状に応じた刃型や加工パスの設計が重要です。
2. 高性能な工具材質・コーティングの採用(工具の進化を活用)
現代の切削工具は、材料・構造・表面処理が著しく進化しています。
対策の詳細:
- 工具材質:
- 炭素鋼工具(SK材)は安価だが摩耗に弱いため、量産加工には不向き。
- **超硬工具(WC-Co)**は耐摩耗性が高く、汎用性が広い。
- **CBN(立方晶窒化ホウ素)**は焼入れ鋼などの高硬度材に最適。
- **PCD(多結晶ダイヤモンド)**は非鉄金属・樹脂・グラファイトに最適だが鉄系には不向き。
- コーティング:
- TiN(窒化チタン):耐摩耗性と安定性に優れ、汎用向け。
- TiAlN・AlTiN:高温耐酸化性が高く、ドライ加工や高速加工に強い。
- DLC(ダイヤモンドライクカーボン):摩擦係数が小さく、非鉄金属に有効。
- コーティングは使用目的に応じて使い分けることがポイントです。
3. クーラント(切削油)の適切な使用と供給方法
切削液の管理は、摩耗の熱的・摩擦的要因を抑えるうえで重要です。
対策の詳細:
- 内部給油方式(Through Spindle Coolant):
- 工具中心から高圧で切削点に直接冷却剤を噴射。特に深穴加工や難削材加工に有効。
- 高圧クーラントシステム(HPC):
- 圧力20〜70bar以上での供給により、切りくず除去や熱制御が向上。
- MQL(微量潤滑)方式:
- オイルミストで環境対応型の潤滑が可能。アルミ加工や乾式加工に向くが、過熱には注意が必要。
- 冷却剤の種類:
- 水溶性、非水溶性、合成系、エマルジョン系など、ワーク材質や加工精度によって使い分けが必要。
4. 工具寿命の管理と予防保全(運用体制の構築)
工具の使用状況を数値的に管理することで、突発的なトラブルを未然に防げます。
対策の詳細:
- 摩耗限界寸法の設定:
- 各工具に対し「摩耗幅(VB)0.3mm」などの交換基準値を明確化。
- 工具管理システムの導入:
- 加工サイクル数や使用時間を自動で記録・通知するソフトを活用。
- RFIDタグ付きの工具管理でトレーサビリティを向上。
- 定期再研磨と再利用:
- 摩耗が軽度なうちに再研磨を行うことで、工具を長期間使用可能。
- 再研磨後の工具には再コーティングを施すことで性能維持も可能。
5. 工作機械と周辺環境の改善
切削性能は工具だけでなく、機械全体の剛性・精度にも左右されます。
対策の詳細:
- 主軸の剛性・精度の確認:
- 主軸ベアリングのガタや振れがあると、刃先が振動し摩耗進行が加速。
- ツーリングの見直し:
- ホルダの振れ精度(ランアウト)を5μm以内に抑える。
- 振動吸収性の高いホルダ(制振ホルダや油圧チャック)を使うことで、ビビリによる局所摩耗を抑制。
- 温度管理:
- 加工空間の温度変動を最小限にすることで、機械・工具の熱変位を防ぎ、精度・寿命が向上。
6. 加工パスと戦略の最適化
加工の仕方そのものが、摩耗の速度に大きく影響します。
対策の詳細:
- HSM(高速高能率加工):
- 負荷一定制御により刃先負担を均一化。摩耗の偏りを防止。
- トロコイド加工やヘリカル加工:
- 一般的な加工に比べて切削点の熱集中を分散できる。
- ステップダウン制御:
- 切込みを段階的に調整し、衝撃的な工具負荷の上昇を避ける。
- 旋削では、自動バイト補正や切込み量の変化に注意し、チッピングを防止。
摩耗の進行と加工品質の関係
摩耗が進行すると、次のような品質面への影響が現れます。
摩耗状態 | 加工品質への影響 | 対応策 |
---|---|---|
軽度摩耗 | 寸法精度の低下、バリの発生 | 条件見直し・再研磨 |
中度摩耗 | 表面粗さの悪化、切りくず詰まり | 工具交換の検討・潤滑強化 |
重度摩耗・破損 | ワークの損傷、刃先欠損による停止 | 即時交換・異常検知システム導入 |
難削材における特有の摩耗対策
難削材(インコネル、チタン、焼入れ鋼など)では、一般材料と比較して摩耗が激しいため、以下のような対策が求められます。
- CBNやPCD工具を使い、摩耗への耐性を高める。
- 低速加工+高送りといった、摩耗抑制型の切削戦略を採用。
- クーラントを高圧・内部噴射にすることで、切削点の温度上昇を抑える。
まとめ
切削工具の摩耗は、加工現場における生産性や品質を大きく左右します。摩耗の種類と原因を正しく理解し、適切な対策を講じることで、工具寿命を延ばしつつ安定した加工品質を保つことが可能です。
日々の加工の中で「摩耗は仕方ない」と片付けるのではなく、「どうすれば抑えられるか」という視点で改善活動を進めていくことが、競争力のある現場づくりにつながります。