切削加工で寸法精度を高めるコツ10選
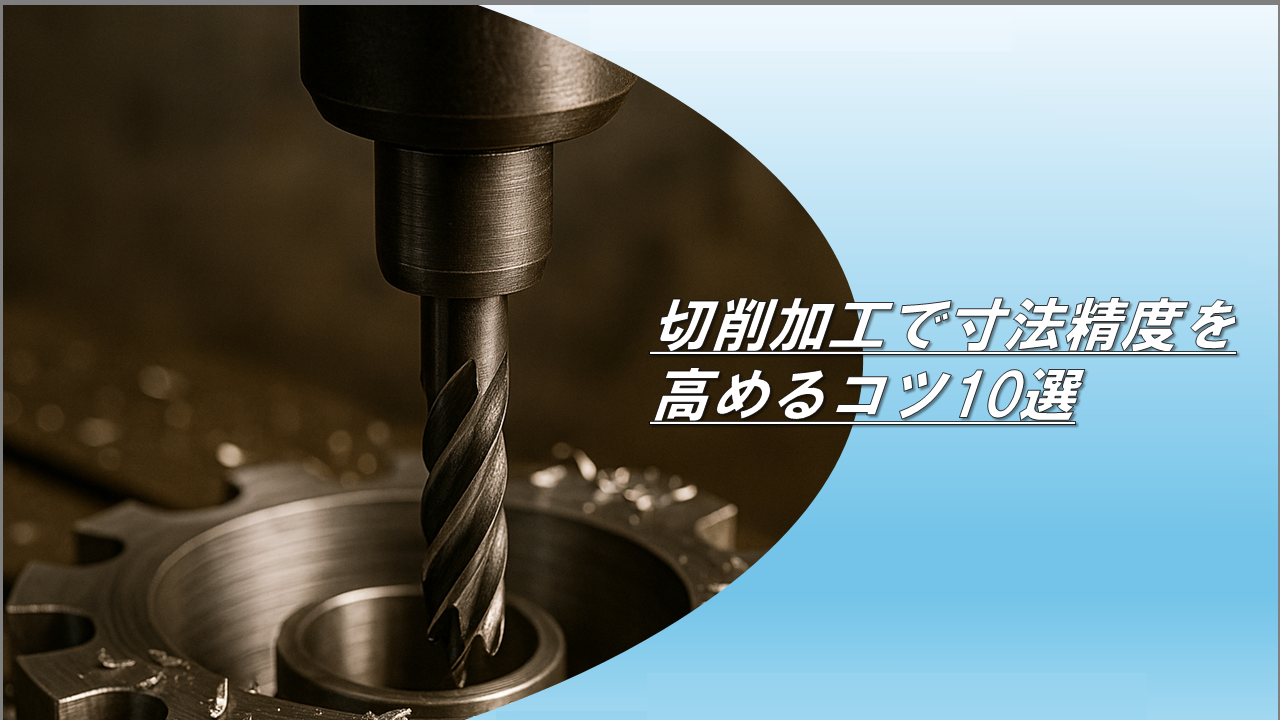
製造業の現場において、寸法精度は製品の品質や信頼性に直結する重要な要素です。特に高精度部品の加工を行う際には、ミクロン単位の精度管理が求められることも珍しくありません。この記事では、切削加工で寸法精度を高めるための実践的なコツを10項目に分けて解説します。NC加工、マシニング、汎用旋盤など、どの現場でも活かせる内容です。
1. 加工手順の最適化を図る
最初の段階で重要なのが、加工工程の順序設計です。粗加工から仕上げ加工へと段階的に進める中で、不要な応力を避け、歪みを最小限に抑える構成が必要です。
- 粗加工で余分な材を大まかに除去
- 中仕上げで外形を整え
- 最後に一発仕上げで精度を追い込む
このように段階を分けることで、熱・加工負荷による変形を抑えられます。
2. クランプと治具の工夫
ワークの固定方法が不安定だと、加工中に微小なズレが生じ、精度が著しく低下します。
- クランプ圧は「強すぎず・弱すぎず」
- 治具設計において「基準面の安定性」を確保
- バイスやチャックの摩耗チェックも忘れずに
特にアルミや樹脂など柔らかい材料では、クランプ圧で歪むことがあるため注意が必要です。
3. 工具の選定と管理
工具の摩耗や欠けは、寸法精度を悪化させる大きな原因です。以下の点に注意しましょう。
- 材料に適した刃物材質と形状を選定(例:超硬、コーティング工具など)
- 工具摩耗の定期交換基準を設ける
- 加工プログラム内に**工具補正量(オフセット)**を適宜調整
また、ドリルやエンドミルの芯ブレも精度に大きな影響を与えるため、ホルダのバランスや芯出し精度も要チェックです。
4. 切削条件の適正化
切削速度、送り、切込み深さなどの条件が不適切だと、振動や焼き付きが発生し、寸法誤差につながります。
- 仕上げ加工では低速高送りよりも高速低送りが一般的に精度が出しやすい
- 加工負荷が高すぎるとワークの変形が起こりやすい
- 安定した切削ができる条件をデータ化し、加工条件を管理
最適条件は材料・工具・工作機械によって異なるため、試験加工によるデータ蓄積が有効です。
5. 温度管理と熱変位対策
金属は熱膨張により寸法が変化します。精度要求が高い場合、以下のような管理が必要です。
- 加工室の温度管理(20±1℃)
- ワークと機械が熱平衡状態になってから加工する
- 長時間加工では間欠加工で熱を逃がす
- 測定器具の温度補正も忘れずに
また、切削油を循環させて工具やワークの温度上昇を抑えるのも有効です。
6. 加工機械の整備と校正
いくら加工条件を最適化しても、機械自体にガタやズレがあると意味がありません。
- 各軸のバックラッシ調整
- スピンドルの振れ精度確認
- サーボモータの補正値確認
- 年1回以上の機械校正・精度チェック
特に工作機械の水平出しが狂うと、加工面全体に傾きが出るため定期点検は必須です。
7. 基準面・基準点の統一
加工において重要なのは「どこを基準にするか」を明確にすることです。
- ワークの基準面・基準穴を統一する
- 加工プログラムではワーク座標系(G54~G59など)を明確に指定
- 可能であれば全加工を1チャッキングで完結
複数の治具や機械をまたぐ場合、基準点のズレが大きな精度劣化につながります。
8. 測定とフィードバックの徹底
寸法精度を高めるには、リアルタイムな測定とフィードバックが不可欠です。
- 加工中にノギス・マイクロメータ・3次元測定機を活用
- 初品チェックだけでなく、中間検査を実施
- 結果に応じて、工具補正値や送り条件を修正
また、測定者間で結果に差が出ないよう、測定環境と技術の標準化も求められます。
9. バリの処理と面取りの最適化
意外と見落としがちなのがバリやエッジの処理です。
- バリが残ると寸法測定に影響し、実測値が変わる
- 面取り過剰は寸法の一部を削りすぎる原因に
- 自動面取り機能を使う場合もプログラム上で寸法許容を管理
精密部品では、バリ取り後に寸法を再チェックすることが精度保証につながります。
10. 加工履歴とトレーサビリティの確保
同じ加工を繰り返す中で、常に高精度を維持するには履歴管理と記録が重要です。
- 加工条件、測定値、工具の使用時間などを記録
- 加工者や加工機ごとのばらつきを分析
- 加工誤差の傾向を分析して次回に反映
これにより、不良予防・品質の安定化に直結します。
まとめ:精度向上は「仕組みづくり」と「継続」がカギ
寸法精度の向上には、単に最新の機械や工具を導入するだけでは不十分です。現場の作業者の「観察力」「気付き」「改善力」そして「記録と再現性」がものを言います。
寸法精度を高めるための要点:
項目 | 要点 |
---|---|
工程設計 | 段階的な加工構成 |
固定方法 | 適正なクランプ圧と治具設計 |
工具管理 | 摩耗管理とオフセット調整 |
切削条件 | 振動を抑えた安定加工 |
温度管理 | 室温・熱変位への配慮 |
機械の整備 | 校正と定期点検 |
基準の統一 | 加工基準点の明確化 |
測定の徹底 | 中間検査とフィードバック |
バリ処理 | 面取りと測定値の整合性 |
加工履歴 | 条件と結果の記録と分析 |
以上を現場で実践することで、寸法誤差を抑え、より安定した加工精度を実現できます。