真鍮加工で発生するバリの原因と対策
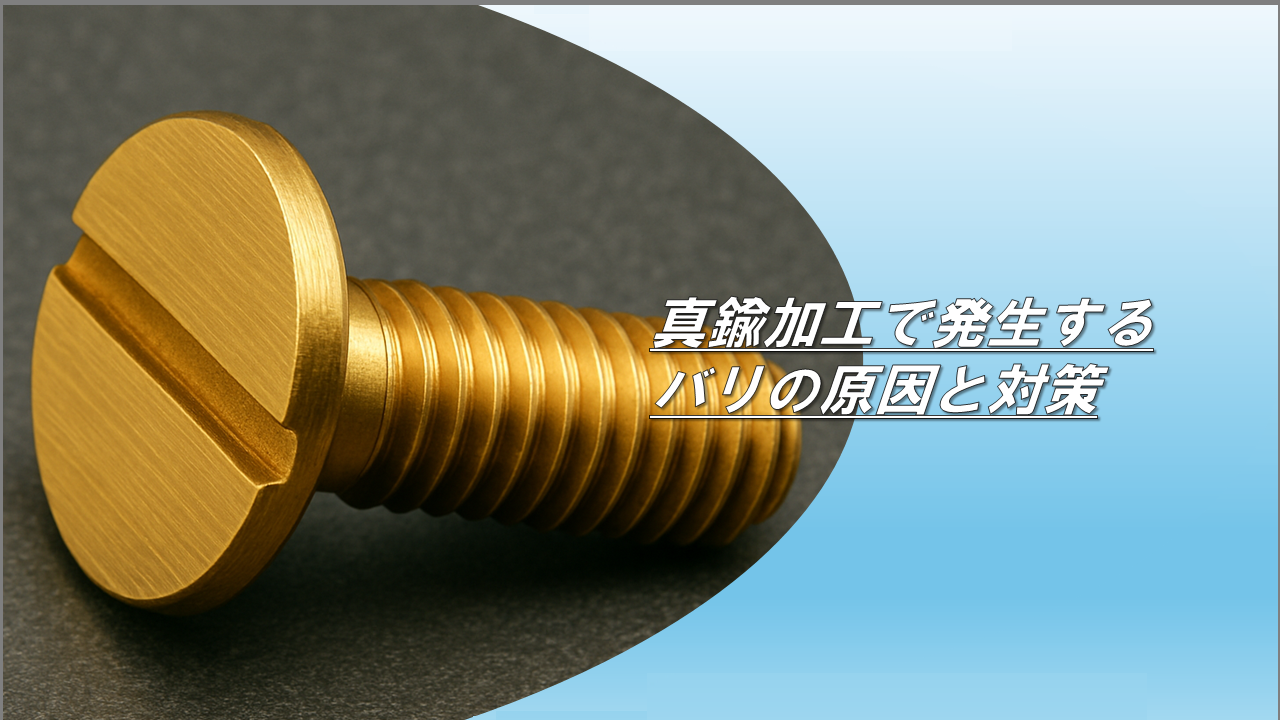
mw2pp0jd6c
CONTENTS
はじめに
真鍮はその加工性の高さから多くの機械部品や装飾品に使用されており、切削・穴あけ・フライス・旋盤加工など多様な加工手法に対応します。しかし、その一方で「バリ(burr)」の発生は避けられず、精密加工を行う現場では品質や後工程に悪影響を与える原因となります。本記事では、真鍮加工におけるバリ発生の原因を体系的に整理し、それぞれの対策を技術・工程・設備面から詳述します。
1. バリとは何か?
バリとは、切削や穴あけなどの加工時に発生する余剰金属の突起や残留物のことを指します。特に真鍮などの展延性を持つ金属では、加工方向に応じて材料が塑性変形し、意図しない形状の突起がエッジや開口部に残る傾向があります。
主なバリの種類:
- エッジバリ(端面バリ):刃物の通過終点に発生する突起
- ドリルバリ(裏バリ):穴あけ加工時、工具の抜け側にできる突起
- ミルバリ(側面バリ):フライスや旋盤など連続加工で発生
2. 真鍮加工におけるバリ発生の主な原因
2-1. 切削条件の不適切な設定
- 送り速度が遅すぎる、または切削速度が速すぎると、刃物が素材を引きちぎるように動作し、バリが発生しやすくなります。
2-2. 工具の摩耗・不適切な刃先形状
- 刃先が摩耗していると切れ味が鈍り、金属を「切る」のではなく「押しつぶす」ような状態となり、バリの発生を助長します。
- 真鍮用に最適化されていない刃角やチップ形状を使用しているケースも原因です。
2-3. 穴あけ・貫通加工の不完全処理
- ドリル加工では、抜け時に裏面に大きなバリが出ることがあります。特にC3604など快削性に富む真鍮は切削抵抗が小さく、貫通時の制御が甘くなりがちです。
2-4. 被削材の性質
- 真鍮は銅と亜鉛の合金であり、成分比率や材質グレード(C3604、C2801など)により加工中の塑性挙動が変わります。例えば延性の高いC2801はバリが出やすく、逆に快削性の高いC3604では比較的抑えられる傾向にあります。
2-5. 加工順序や固定不良
- 加工工程における順序設定やワークの固定力が不十分だと、工具の抜け時や材料のびびりにより余分な変形が起こり、バリが発生します。
3. 真鍮バリ対策の基本戦略(加筆修正版)
真鍮の切削加工におけるバリ対策は、「バリを発生させない工夫」と「発生しても除去しやすい設計」の両輪で成り立ちます。ここでは、現場で即実践できる具体的な戦略を、加工条件・工具管理・補助処理の3軸で整理します。
3-1. 加工条件の最適化
切削条件はバリ発生の主因であり、わずかな調整で大きな効果が得られることがあります。
- 切削速度(Vc)と送り速度(fz)のバランス
真鍮は高回転加工に適しており、切削速度は60~120 m/minが目安です。ただし、送り速度が小さすぎると塑性変形が大きくなり、刃物が材料を“押し流す”ように切るためバリが出やすくなります。推奨される送り速度は0.05〜0.2 mm/rev程度です。 - 切込み量の調整
極端に浅い切込みでは材料が刃物を逃げるように変形しやすく、バリが発生します。1回あたりの切込みは十分に取り、できるだけ少ない回数で仕上げることで、塑性変形を抑制します。 - 仕上げ刃物の使用
粗加工と仕上げ加工を分けることで、最終工程での刃物負荷を減らし、仕上げ面にバリが残るリスクを抑えられます。
3-2. 工具の適正管理と選定
工具の摩耗や形状不適合は、真鍮加工でのバリ発生率を大きく左右します。以下の点を重視すべきです。
- 真鍮専用設計の工具使用
例えばポジティブなすくい角を持つ超硬工具や、鋭角な刃先をもつハイスエンドミルなどは、真鍮の切れ味を活かしつつバリ発生を最小限に抑える効果があります。 - チップのブレーカ形状
特に旋盤加工では、切りくず制御が不適切だと切りくずが刃先に干渉してバリの原因になります。バリを出さないためには、真鍮用に設計された小さめのチップブレーカを使うのが有効です。 - 刃先の再研磨・交換基準の明確化
摩耗した工具は切削抵抗を増加させ、バリが増加します。切削面の変色や切りくず形状の変化を目安に、定期的な交換サイクルを設けましょう。
3-3. 加工手順と補助工程の工夫
加工手順の見直しや、バリ除去工程の自動化・合理化によって、後工程でのトラブルや手戻りを防止できます。
- 加工順序の最適化
たとえば穴あけの前に外形切削を行うと、クランプ剛性が下がりバリが出やすくなるため、内側から外側への順番で工程を構築します。また、複数穴加工時は工具抜け方向を揃えて、裏バリの集中処理が可能な設計にすると効率的です。 - 面取り工程の自動化
C0.2〜0.5程度の面取りは、NCプログラムで自動挿入するのが一般的です。専用の面取り工具(カウンターシンクやC面ツール)を導入し、仕上げと同時にバリを抑制する体制を整えましょう。 - 裏バリ対策用の裏当て・捨て板使用
ドリル貫通時にワークの裏側に当て材を配置することで、抜け際の材料破断を抑え、裏バリを最小限に抑えることが可能です。高精度品では薄いアルミや真鍮の捨て板が使用されます。
3-4. 加工設計段階での工夫(設計部門との連携)
製造側だけでなく、図面設計段階でのバリ抑制配慮も非常に重要です。
- エッジへの面取り指定
「シャープエッジ不可」や「R0.2以上」など、図面上にバリ対策の明記があることで、現場対応のばらつきが減少します。 - バリの発生を考慮した開口設計
溝や穴の逃げ形状を工夫することで、工具の抜け方向に余裕をもたせ、バリ発生リスクを抑えます。 - 交差緩和の検討
高精度が不要な箇所では交差範囲を適度に広げることで、過剰な仕上げ加工によるバリ発生の抑制につながります。
4. バリ除去(バリ取り)工程の選択肢
4-1. 手作業によるバリ取り
- ヤスリ、バリ取りナイフ、ペーパー等を用いる
- 単純形状の小ロット加工品に適する
4-2. 自動バリ取り機・C面加工機
- 面取りツールを用いたC面・R面加工で外観品質を維持
- 量産対応や人手不足対策に有効
4-3. ショットブラスト・バレル研磨
- 小型部品の大量バリ取りに有効
- 外観仕上げとバリ除去を同時に行える
4-4. 電解バリ取り(電解研磨)
- 微細バリ、複雑形状の内部バリ処理に向く
- 表面光沢も得られるがコストと設備が必要
5. 加工設計段階でのバリ対策
- 公差設計と面取り指示を図面に明記しておくことで、現場での曖昧な対応を防止
- バリの発生しにくい加工順序の構築
- 加工方向の最適化により、裏バリや重複加工によるバリの抑制が可能
6. 真鍮特有の注意点
真鍮種別 | バリの発生傾向 | 対応策 |
---|---|---|
C3604(快削黄銅) | 比較的少ない | 適切な工具選定と高回転加工で最小限に抑えられる |
C2801(黄銅2種) | やや延性が高く出やすい | 食いつき角度や送り速度を工夫 |
鉛フリー真鍮 | 加工抵抗がやや高く、刃先への負荷大 | より鋭利な工具が必要、摩耗に注意 |
まとめ
真鍮加工におけるバリの発生は、加工条件、工具、素材特性、工程設計といった多くの要因が複雑に絡み合って生じます。高品質な加工を実現するには、バリが出る前提での設計と、バリの発生を最小限にする切削制御、さらに適切なバリ取り工程の組み合わせが必要不可欠です。とくに量産や高精度加工の現場では、標準化・自動化によるバリ対策の内製化が品質維持とコスト削減の鍵となります。