◆工具費を抑えて真鍮加工の利益率を改善するには?
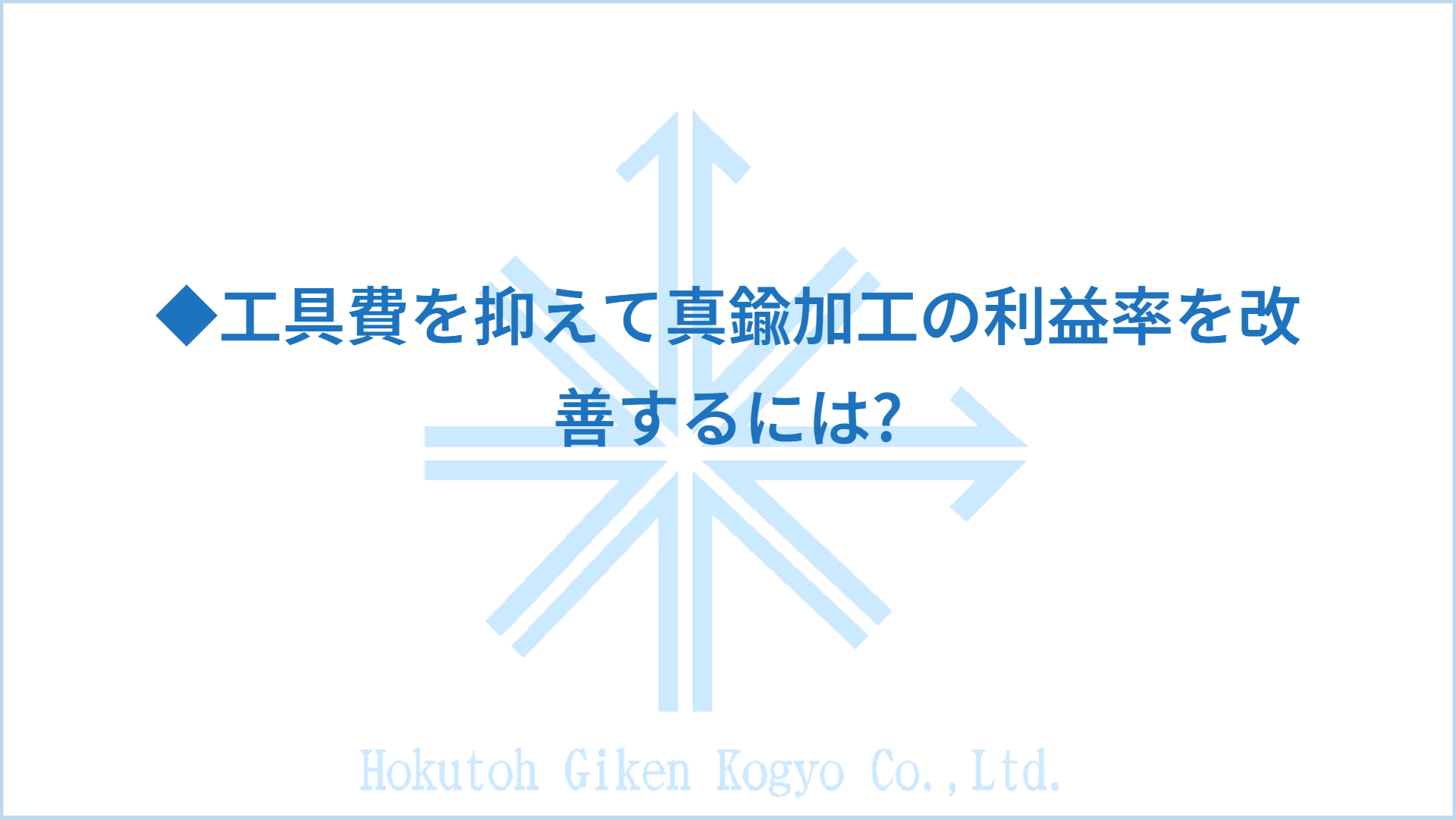
はじめに
真鍮加工において、利益率を左右する大きなコスト要因の一つが「工具費」です。特に量産体制においては、工具交換の頻度や突発的な工具破損による損失が利益を圧迫する要因となりがちです。そこで本稿では、真鍮加工における工具費を抑制しつつ、品質を維持または向上させ、結果として利益率を改善するための具体的かつ実践的な方策を、技術的・運用的・経営的観点から詳述していきます。
1. 工具費の内訳とその影響
1-1. 工具費とは何か?
工具費とは、加工に使用する切削工具(エンドミル、バイト、ドリル、リーマーなど)の購入費用、再研磨費、交換頻度に起因する作業工数の損失などを含む、トータルのコスト要素を指します。真鍮加工においては比較的切削性が高いとはいえ、以下のような要因により工具費は膨らむ可能性があります。
- 高速加工による工具摩耗の加速
- 被削材の種類(快削黄銅C3604 vs 高強度真鍮など)
- クーラントの使用状況
- 工具寿命管理の不徹底
1-2. 工具費が利益率に及ぼす影響
たとえば、ある加工品で1個あたりの工具コストが30円かかっている場合、年間10万個生産するだけで工具費は300万円になります。仮にこれを20円に削減できれば、年間で100万円の経費削減、つまりその分の純利益が増えることになります。これは中小企業の加工現場にとって非常に大きなインパクトです。
2. 工具費削減のための技術的アプローチ
2-1. 適正な切削条件の設定
真鍮は鉄やステンレスに比べて加工がしやすい金属ですが、あまりにも高い切削速度を設定すると、工具の摩耗を早めてしまいます。特に注意すべきは以下の3点です。
- 切削速度(Vc):高すぎると工具の摩耗が急激に進行します。
- 送り速度(fz):過大な送りは切りくず排出を妨げ、チップ損傷の原因になります。
- 切込み量(ap, ae):加工面積を無理に増やすと、工具の負荷が増大します。
推奨設定例(C3604切削時)
加工方法 | 工具径 | 切削速度 (m/min) | 送り (mm/tooth) | 切込み (mm) |
---|---|---|---|---|
フライス加工 | φ10 | 150〜200 | 0.05〜0.08 | ap=1.0、ae=0.5 |
旋盤加工 | φ20 | 100〜150 | 0.1〜0.2 | ap=1.5 |
2-2. 工具材質の最適化
安価な超硬工具を選定することで初期コストは下がりますが、結果的に寿命が短く、頻繁な交換が発生することで総コストが高くなるケースがあります。以下のような工具材質の選定がポイントです。
- 超微粒子超硬(Submicron Carbide):高剛性で耐摩耗性に優れ、長寿命。
- コーティング付き工具:TiN, TiAlNなど、真鍮加工では非推奨のことが多いが、特殊コーティング(AlCrNなど)を選べば切りくず排出が改善され寿命が延びることも。
2-3. 再研磨・再利用の活用
一定のサイズのエンドミルやドリルは再研磨することで3〜4回まで再利用が可能です。再研磨コスト(1本あたり300〜500円)と新品購入コスト(1500〜2500円)を比較すれば、その有用性は明白です。
3. 工具寿命の管理と最適タイミングでの交換
3-1. 工具摩耗の種類と兆候
摩耗タイプ | 特徴 | 兆候 |
---|---|---|
フランク摩耗 | 刃先が摩耗し、幅が広がる | 寸法精度の低下、バリの増加 |
クレーター摩耗 | チップ表面に凹みができる | 面粗度の悪化 |
刃こぼれ・チッピング | 微小な欠けが発生 | 異音、切りくずの不均一化 |
3-2. 工具交換の判断基準
- 工具寿命管理シートの活用
- 稼働時間に基づく予防交換
- 異音・振動検知によるリアルタイム監視(センサ付き主軸が有効)
4. 工具選定と調達におけるコストダウン戦略
4-1. 工具メーカーの見直し
同等性能で価格が30%以上安価な海外製品や、国内でも中堅ブランドに切り替えることで大幅なコスト削減が可能です。例として以下のようなブランド比較があります。
ブランド | 特徴 | コスト(目安) | 信頼性 |
---|---|---|---|
大手A社 | 長寿命・安定性 | 高(¥3,000〜) | ◎ |
中堅B社 | 性能は及第点 | 中(¥1,500〜) | ○ |
海外C社 | 安価・納期に難あり | 低(¥800〜) | △〜○ |
4-2. 一括購入・契約購買の導入
工具を都度購入するよりも、月次・四半期単位の発注ロットで契約することで、単価を15〜30%抑えることが可能です。また、下記のような運用が効果的です。
- 年間使用数に応じた量産価格交渉
- 在庫最適化と発注の自動化(MROシステム連携)
5. 加工プロセス全体の見直しと改善
5-1. 加工手順の統合と最適化
1個あたりの加工工程数を減らすことで、使用工具の種類と総消費量を削減できます。特に、以下の見直しが効果的です。
- 荒加工と仕上げを兼用する工具の導入
- マルチフルートエンドミルやハイブリッド工具の採用
- 同時5軸加工で工程を統合
5-2. 自動化・IoTの活用
工具交換予測や寿命監視にIoTを活用することで、「工具破損による不良品」や「過剰な早期交換によるコスト増」を防止できます。
- 工具摩耗検知センサー
- 加工状態監視システム(振動・温度・スピンドル負荷)
6. 人的運用によるロス削減
6-1. オペレータの教育
工具寿命や摩耗兆候に対する現場の感度が低い場合、不要な交換や見逃しによる不良発生が起こりやすくなります。以下の教育が重要です。
- 寿命限界の見極めポイント
- 工具別の切削音の違いの把握
- チップ形状・切りくず色の変化での判断
6-2. 工具在庫の見える化と適正管理
- 棚卸のデジタル化(バーコード・RFID)
- 使用履歴の可視化(誰が・いつ・どの工具を使ったか)
7. ケーススタディ:工具費削減による利益改善例
ケースA:中小量産部品メーカー
- 年間工具購入額:480万円
- 寿命管理と再研磨導入で30%削減 → 336万円に
- 利益改善額:144万円/年
ケースB:多品種少量対応の加工会社
- 工具種の統合(5種類 → 3種類)
- 加工工程の短縮(5工程 → 3工程)
- 工具在庫圧縮による無駄削減:約80万円
8. 経営者・購買部門ができること
- 工具費のKPI化(工具単価・寿命・1製品あたり工具原価)
- 工具メーカーとの共同開発によるオリジナル品導入
- 購買部門と現場の情報共有体制(なぜ高い工具が必要か、寿命が伸びたのか、などの見える化)
おわりに
真鍮加工における利益率改善は、単なる工具の「安価化」ではなく、「適正な工具管理」と「工程の最適化」を通じて達成されるべきです。本稿で紹介した複数の視点(技術、購買、現場、経営)を組み合わせて実行することで、工具費を30〜50%削減しながら、加工品質と利益率を同時に向上させることが可能です。現場の声を生かした地道な改善こそが、継続的な競争力につながります。