◆切削加工における切りくず処理の重要性
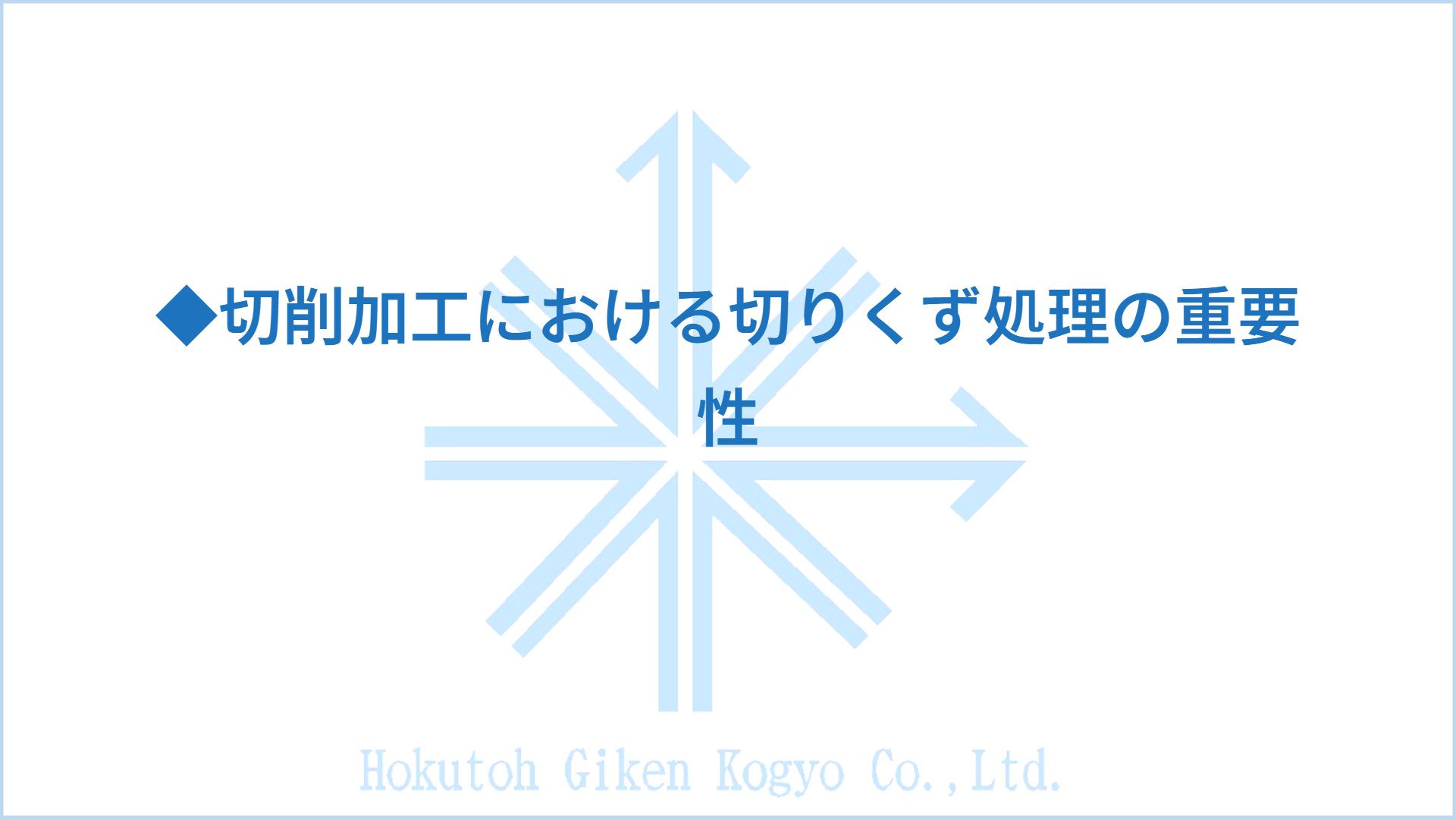
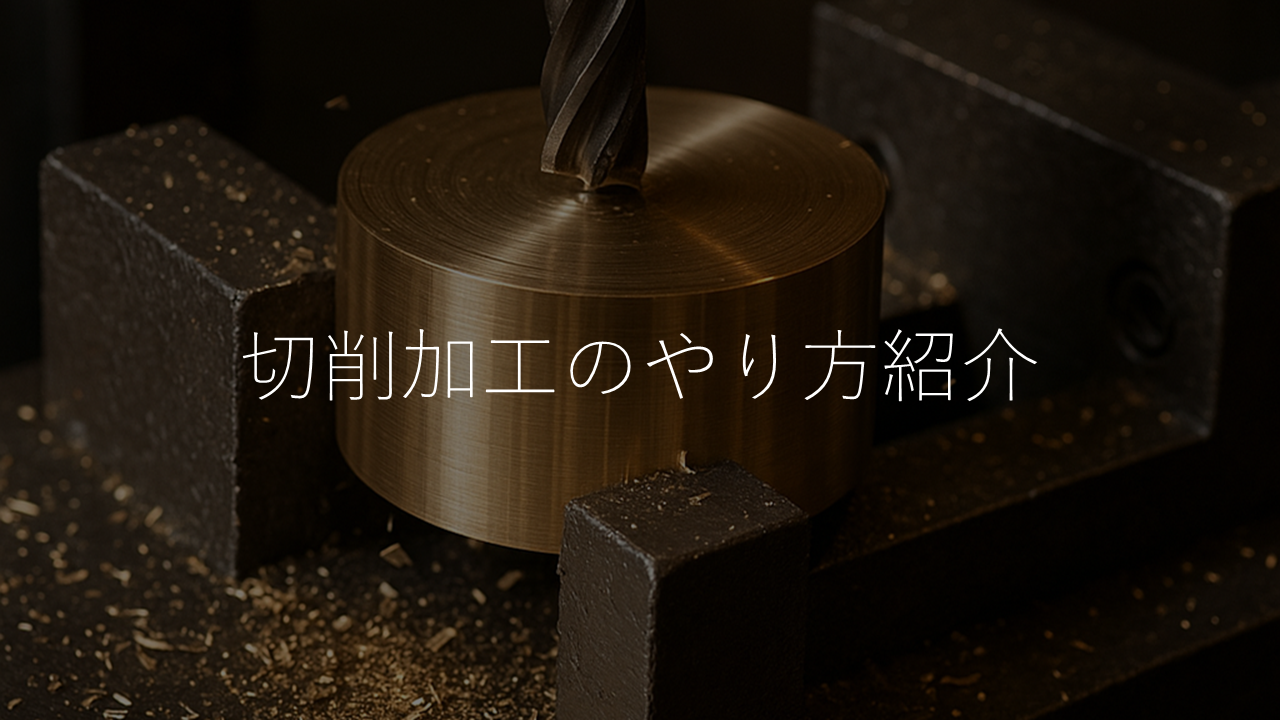
切削加工において発生する「切りくず」は、加工対象物(ワーク)から削り取られた金属片や粉末を指します。この切りくずの処理は、加工精度、作業環境、安全性、設備寿命、コストに至るまで多方面に影響を与える非常に重要な要素です。適切な切りくず処理を行うことは、品質の安定と生産効率の向上に直結するため、加工現場では必須の対応事項となっています。
本記事では、切削加工における切りくず処理の重要性について、具体的なリスク、処理手法、改善事例などを交えて詳しく解説します。
1. 切りくずが引き起こす主な問題点
切削加工中に発生する切りくずは、適切に処理されないと、以下のような深刻な問題を引き起こします。
1-1. 加工精度の低下
切りくずがワークや工具に再接触することで、以下のような不具合が生じます。
- 表面傷やバリの発生
- 工具と切りくずの再切削による寸法誤差
- 切削面の粗さ悪化(Ra値上昇)
特に精密加工においては微小な異物混入も致命的な欠陥の原因となるため、切りくずの速やかな排出が求められます。
1-2. 工具寿命の短縮
切りくずが切削点に滞留すると、刃先への過負荷や過熱が生じやすくなり、以下のような影響が発生します。
- 刃先摩耗の加速
- チッピングや工具欠損
- コーティング層の剥離
結果として、工具交換頻度が増し、工具コストが増大します。
1-3. 排熱不良・熱変形の誘発
切りくずが加工部位に残留すると、熱の逃げ場が妨げられ、局所的な温度上昇を招きます。これによりワークや工具が熱膨張を起こし、寸法精度の低下や変形が発生する原因となります。
1-4. 自動化・連続加工の妨げ
近年の無人加工ラインや自動化システムでは、切りくず処理が適切に行われていないと、
- ワーク交換ロボットの誤動作
- チャック部への切りくず噛み込み
- センサー類の誤検知や誤作動
といった問題が起こり、生産ラインが停止するリスクが増大します。
1-5. 作業者の安全リスク
鋭利で高温な切りくずは、作業者の皮膚や目に飛散する危険性があり、重大な災害事故に発展することもあります。安全な職場環境の確保のためにも、切りくずの管理は欠かせません。
2. 切りくずの種類と形状による影響
切りくずの形状や性質は、被削材の種類、工具の材質と形状、切削条件(速度、送り、切込み量)に大きく依存します。主な切りくず形状には以下のような分類があります。
切りくずの形状 | 特徴 | 加工への影響 |
---|---|---|
連続切りくず | 長く帯状になる | 絡まりやすく、処理が困難 |
破砕切りくず | 短く粉状または粒状 | 処理がしやすいが、飛散しやすい |
わら状切りくず | 渦巻き状に巻かれる | ロボットやチャックに巻き付きやすい |
針状切りくず | 鋭く長いスパイク状 | 作業者に対して危険度が高い |
切りくずの望ましい形状は「破砕切りくず」であり、そのためには切りくずブレーカ付きの工具の採用や切削条件の最適化が重要となります。
3. 主な切りくず処理方法
切りくず処理には、現場規模や加工機の仕様に応じて様々な方法があります。代表的な手法を以下に示します。
3-1. 切りくずコンベアの活用
工作機械の底部や側面に設置された切りくずコンベアは、加工中に発生した切りくずを自動的に排出装置へ搬送する仕組みです。特に大量生産現場においては、コンベアの有無が稼働率に直結します。
コンベアの種類:
- スクラッパー式:粉状や小粒切りくずに適する
- ベルト式:軽量かつ低コスト
- ドラッグチェーン式:長尺切りくずに対応可能
3-2. クーラントフィルタリングとの連動
クーラント液と一緒に流れる細かい切りくずは、クーラントフィルターを通して分離されます。ろ過精度が不十分だとノズル詰まりや加工精度低下につながるため、定期的なメンテナンスと精密フィルターの使用が推奨されます。
3-3. マグネットセパレーター
鉄系の被削材に対しては、磁力を利用して切りくずを回収するマグネットセパレーターが有効です。コンパクトな構造で、クーラント循環装置に組み込むことで自動回収が可能です。
3-4. 集塵機・吸引装置
アルミや鋳鉄のように微粉塵が発生しやすい素材を加工する場合、吸引式の集塵装置を併設することで、飛散による火災・健康被害・設備汚損のリスクを軽減できます。
4. 切りくず処理による現場改善の事例
【事例1】連続切りくずによるロボット停止の改善
課題:自動旋盤による加工で長尺の連続切りくずが発生し、ロボットアームに絡まり作業停止が頻発。
対応:切りくずブレーカー付きチップへの交換と、送り速度の調整を実施。
効果:破砕状切りくずへと変化し、絡まりゼロに。月間の停止時間が90%削減。
【事例2】切りくずの焼付きによる工具寿命低下
課題:鋼材のフライス加工で切りくずが再切削され、工具寿命が半減。
対応:クーラントノズルの配置を再設計し、切りくず排出性を向上。
効果:切削点からの切りくず排出がスムーズになり、工具寿命が2倍以上に延長。
5. 切りくず処理の今後と自動化の展望
近年ではIoTやセンサー技術を活用し、以下のようなスマート切りくず管理が進展しています。
- センサー連携による切りくず滞留の検知とアラート
- AI画像認識による異常切りくずの検出
- 自動清掃ロボットとの連携による無人処理体制の構築
特に無人化を目指す中小製造業にとっては、切りくず処理の自動化が生産性向上の鍵となります。
6. まとめ
切削加工において切りくず処理は、単なる後片付けや廃棄処理ではなく、品質・安全・生産性を支える中核的な要素です。正しい切りくずの排出と管理は、加工の安定性を維持し、コスト削減や設備寿命の延長にもつながります。
現場ごとに最適な処理方法を選定し、必要に応じてIoTや自動化設備と連携することで、より高次元の加工環境を実現することが可能です。