◆切削加工における主要な加工条件とは?
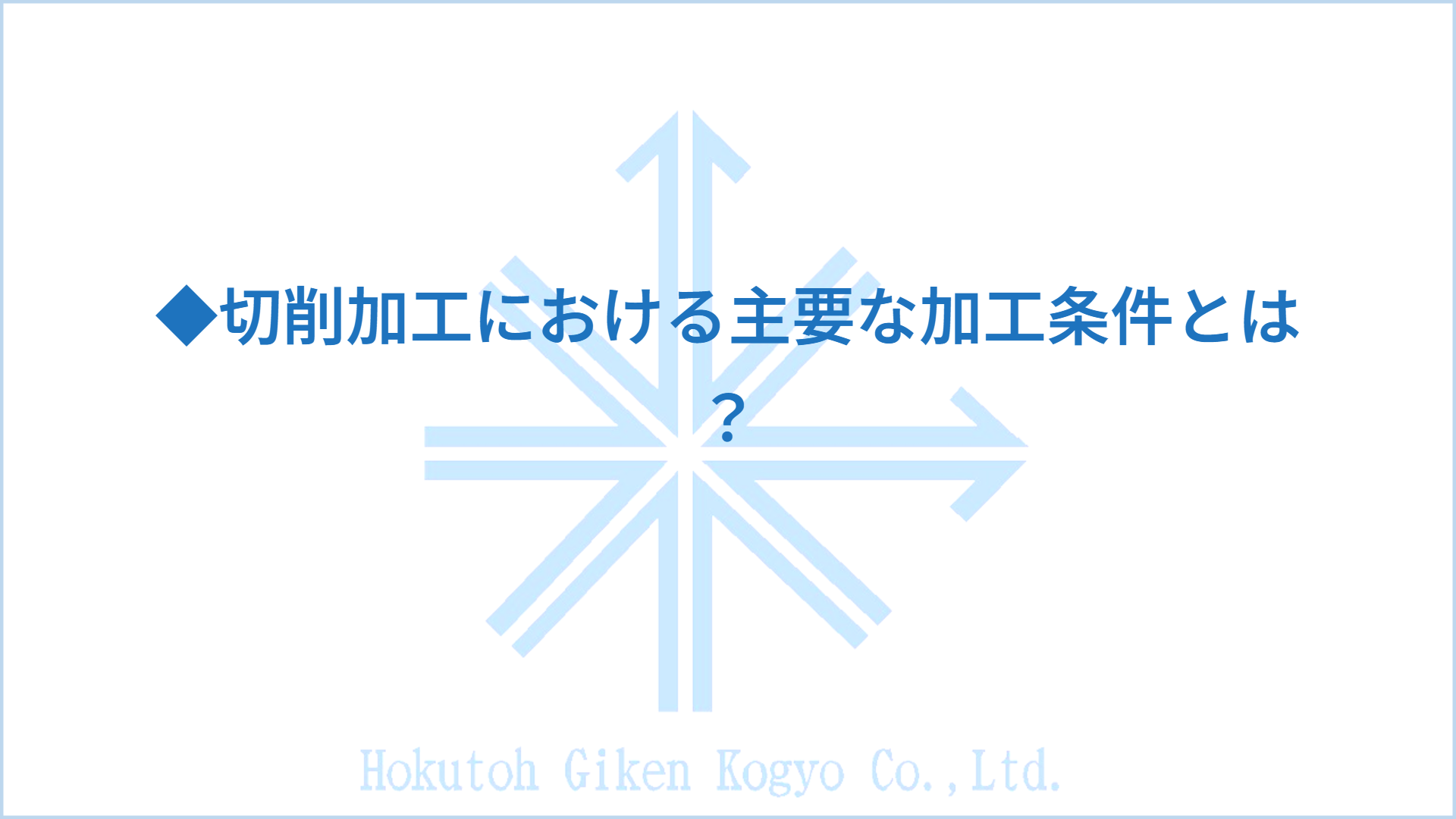
はじめに
切削加工は、金属やプラスチック、木材などの素材から不要な部分を削り取り、目的の形状に仕上げる加工方法です。自動車、航空機、精密機器、医療機器など、幅広い産業分野において必要不可欠な工程であり、製品の精度や品質、加工コスト、さらには生産性にも直結します。
そのため、切削加工の効率性と安定性を確保するためには、「加工条件」の最適化が非常に重要です。本記事では、切削加工における主要な加工条件について、詳細に解説していきます。
1. 切削加工の基本構造と要素
1-1. 切削加工とは?
切削加工は、工具(切削工具)を用いて素材(被削材)に対して機械的に力を加え、不要部分を削り取って所定の形状や寸法に加工する方法です。
一般的な切削加工には以下のような種類があります。
加工方法 | 特徴 |
---|---|
旋盤加工 | 回転する素材に固定した工具で削る |
フライス加工 | 回転する工具で固定した素材を削る |
ボール盤加工 | 回転するドリルで穴を開ける |
ブローチ加工 | 直線的な動きで素材を削る |
これらの加工を成立させるには、工具の選定、機械条件の設定、素材の性質など、多くの条件が複雑に関係します。
2. 主要な切削加工条件とは?
切削加工において「加工条件」とは、加工効率や精度、工具寿命に影響する要素を指します。以下に、代表的な加工条件を一覧で示します。
加工条件 | 説明 |
---|---|
切削速度(Vc) | 工具または素材の周速度(m/min) |
送り速度(f) | 工具の移動量(mm/revまたはmm/min) |
切込み深さ(ap) | 工具が素材に入る深さ(mm) |
切削油剤の有無 | 冷却・潤滑・洗浄の有無 |
工具の材質・形状 | 刃先形状、コーティングなど |
被削材の材質 | 加工しやすさや熱伝導率など |
これらは相互に影響し合い、最適化には経験と試行錯誤が不可欠です。
3. 切削速度(Vc)
3-1. 定義と計算式
切削速度は、工具と素材が相対的に接触する速度で、素材の表面に対してどれだけの速さで刃物が当たっているかを示します。
計算式(旋盤加工の場合): Vc=π×D×N/1000Vc = \pi \times D \times N / 1000Vc=π×D×N/1000
- VcVcVc:切削速度(m/min)
- DDD:素材の直径(mm)
- NNN:主軸回転数(min⁻¹)
3-2. 切削速度が加工に与える影響
- 高すぎる速度: 工具が早く摩耗し、熱の発生も大きくなる
- 低すぎる速度: 加工時間が長くなり、表面粗さも悪化しやすい
3-3. 適正な切削速度の目安
素材別の適正切削速度(参考値):
素材 | 適正切削速度(m/min) |
---|---|
炭素鋼 | 80〜150 |
アルミ合金 | 200〜800 |
ステンレス | 60〜120 |
チタン合金 | 20〜60 |
4. 送り速度(f)
4-1. 定義と種類
送り速度は、切削工具が素材に対して進む速度です。一般的に以下の2種類で管理されます。
- 回転送り(mm/rev): 1回転あたりの送り量(旋盤など)
- 直線送り(mm/min): 単位時間あたりの送り量(フライスなど)
4-2. 加工への影響
- 速すぎる送り: 表面が粗くなり、振動やビビリが出やすくなる
- 遅すぎる送り: 加工時間が長くなり、工具の刃先が摩耗しやすい
4-3. 最適送り速度の決め方
加工機械メーカーや工具メーカーが提供する切削条件表を参考にしつつ、被削材や工具の状態に合わせて調整します。
5. 切込み深さ(ap)
5-1. 定義
切込み深さとは、工具が素材にどれだけ食い込むかを示す値で、1回の切削でどれだけの体積を削るかに関わる要素です。
- ap(mm): 放射方向の切込み深さ
- ae(mm): 径方向の切込み幅(フライスなどで使用)
5-2. 切込み深さの影響
- 深すぎる切込み: 工具負荷が増え、ビビリや破損リスクが高まる
- 浅すぎる切込み: 加工回数が増え、時間とコストが増加する
適切な切込み深さは、素材の硬さと加工目的によって調整する必要があります。
6. 工具材質と形状
6-1. 主な工具材質
材質 | 特徴 |
---|---|
超硬合金(WC) | 高硬度・高耐熱、汎用性が高い |
高速度鋼(HSS) | コストが安く、靭性に優れる |
セラミックス | 高速加工向けだが脆い |
ダイヤモンド | 超精密・非鉄金属向け、価格高 |
6-2. 工具のコーティング
- TiN(チタンナイトライド): 一般用途に最適
- TiAlN: 高温環境やステンレス加工に適す
- DLCコート: アルミや銅などの粘着防止
6-3. 工具形状
刃先角度、チップ形状、逃げ角などの微細な形状も、加工の仕上がりや工具寿命に直結します。
7. 被削材の材質
被削材の硬度や靱性、熱伝導率によって、適切な加工条件は大きく異なります。
材質 | 加工性 | 注意点 |
---|---|---|
アルミ | 良好 | 切りくずの詰まりに注意 |
銅 | 良好 | バリ発生しやすい |
ステンレス | 難削材 | 熱がこもりやすく、加工硬化あり |
チタン | 非常に難削 | 工具摩耗が早い |
難削材ほど、切削条件の管理が重要となり、専用の工具や加工液も必要になります。
8. 切削油(クーラント)
8-1. 使用目的
- 冷却: 工具と素材の温度上昇を抑える
- 潤滑: 摩擦を減らして工具摩耗を防ぐ
- 洗浄: 切りくずを除去し、再切削を防ぐ
- 防錆: 加工後の素材の腐食を防ぐ
8-2. 種類
種類 | 特徴 |
---|---|
水溶性油剤 | 冷却性能が高く、環境にも優しい |
不水溶性油剤 | 潤滑性に優れるが熱がこもりやすい |
ミスト加工 | 微量の油を噴霧、環境対応型 |
ドライ加工 | 油剤不使用、省エネでクリーンだが制約あり |
9. 加工条件の最適化と管理
9-1. 最適化の手順
- 素材と図面に応じた工具を選定
- 加工機械の能力に基づいて速度や送りを設定
- 試加工による条件検証
- 工具摩耗や加工温度を測定
- 工程FMEAや工程能力指数(Cp, Cpk)を活用して継続的改善
9-2. 加工シミュレーションの活用
近年ではCAMソフトやCAEを使い、加工前に切削条件の影響を可視化・予測する方法が一般化しています。
10. 切削条件と品質・コストの関係
加工条件 | 品質への影響 | コストへの影響 |
---|---|---|
高切削速度 | 表面仕上げ向上/工具寿命低下 | 加工時間短縮/工具費上昇 |
低送り速度 | 高精度/加工時間延長 | 工数増加/コスト高騰 |
適切な切込み深さ | 安定加工・工具保護 | 加工時間と効率のバランス |
まとめ
切削加工における主要な加工条件は、切削速度・送り速度・切込み深さを中心に、工具の材質や形状、被削材の性質、切削油の使用有無など多岐にわたります。これらを最適に設定・管理することで、製品の精度や生産効率、コストに大きな差が生まれます。
加工条件の選定は「経験とデータ」によって支えられており、現場でのフィードバックと、最新の加工シミュレーション技術を活用した改善が今後ますます重要となっていくでしょう。