フライス加工と旋盤加工の違いとは?~加工方式の基礎から選定のポイントまで徹底解説~
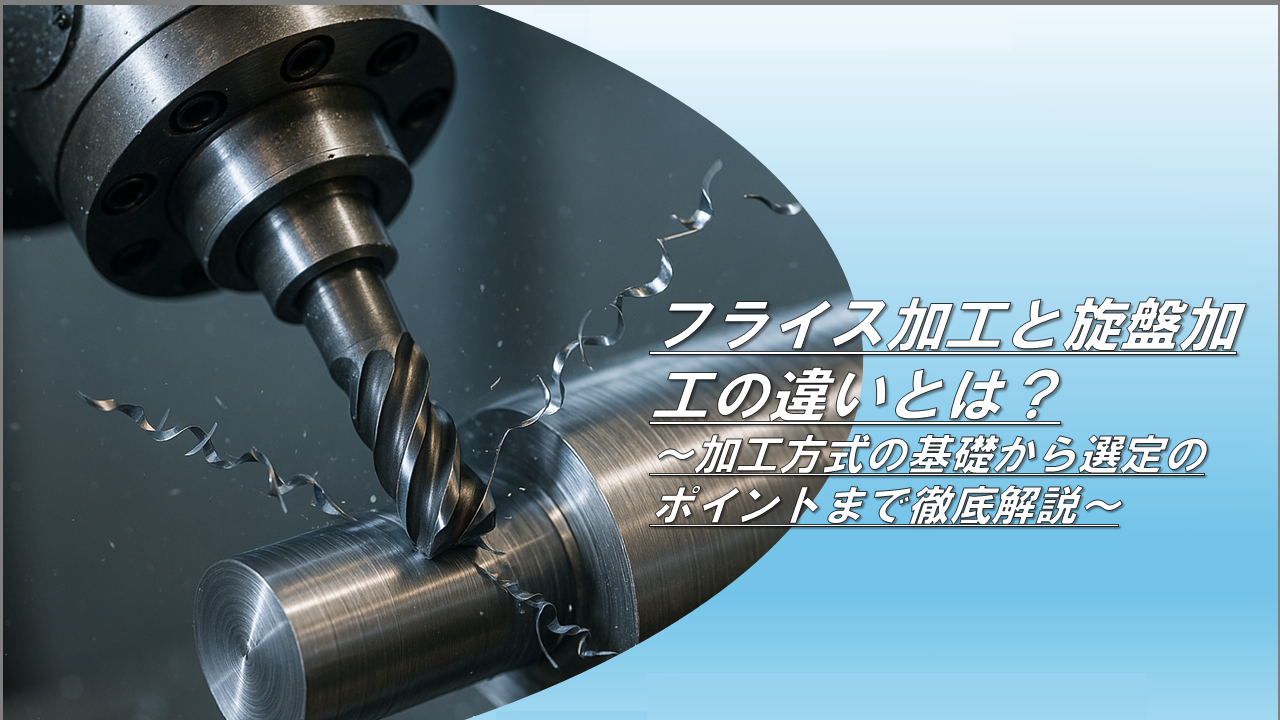
ものづくりの現場において、「切削加工」は金属や樹脂などの材料を精密に加工するための基本技術のひとつです。その中でも特に代表的な加工方法が「フライス加工」と「旋盤加工」です。これらはどちらも広く使われている加工法でありながら、その目的や手法、対応可能な形状、機械構造に大きな違いがあります。
本記事では、これら2つの加工法の違いについて、以下の構成で詳しく解説していきます。
目次
- フライス加工と旋盤加工の基本的な定義
- 使用する機械と工具の違い
- 加工の原理と切削の方向性
- 加工できる形状と精度の違い
- 加工対象素材の違い
- 加工コストと生産性の違い
- 自動化・NC制御の観点から見た違い
- 現場での使い分け事例
- 両者を組み合わせたハイブリッド加工の可能性
- 加工方式選定のチェックポイント
- まとめ
1. フライス加工と旋盤加工の基本的な定義
まずは、それぞれの加工法がどのようなものか、基本的な定義から確認しましょう。
フライス加工(Milling)
フライス加工とは、「フライス盤」と呼ばれる工作機械に回転工具(フライスカッター)を取り付け、材料に対して工具を回転させながら、工作物を移動させて加工する方法です。主に平面、溝、キー溝、歯車などの複雑な形状を削り出すのに適しています。
特徴:
- 工具が回転し、工作物が移動
- 平面加工、曲面加工、穴あけ、キー溝など多様な加工に対応
- 加工形状の自由度が高い
旋盤加工(Turning)
旋盤加工は、「旋盤」と呼ばれる工作機械に材料(丸棒など)を回転させながら、固定された刃物(バイト)で材料を削る加工法です。主に円筒形状の製品を加工するのに適しており、円形部品の外径加工、内径加工、溝入れ、ネジ切りなどを行います。
特徴:
- 工作物が回転し、工具が固定または送り動作
- 円筒部品に特化した加工法
- 精度の高い軸物製品に適している
2. 使用する機械と工具の違い
両者では使用する機械や取り付ける工具も大きく異なります。
項目 | フライス加工 | 旋盤加工 |
---|---|---|
機械名称 | フライス盤 | 旋盤 |
主軸の回転対象 | 工具が回転 | 材料(工作物)が回転 |
主な工具 | エンドミル、フライスカッター | バイト(外径バイト、内径バイトなど) |
チャックの役割 | 工作物をテーブルに固定 | 工作物を主軸にチャッキング |
テーブルの動き | XYZ方向に移動 | X方向(工具の横移動)とZ方向(工具の縦移動) |
3. 加工の原理と切削の方向性
フライス加工の切削原理
フライス加工では、回転する刃物が材料表面を削り取る形で加工します。切削方向は工具の回転と工作物の送り方向によって、以下の2種類に分類されます。
- 順削(ダウンカット): 工具の回転方向と送り方向が同じ。切削力が安定する。
- 逆削(アップカット): 工具の回転方向と送り方向が逆。仕上げ面が良好になりやすい。
旋盤加工の切削原理
旋盤加工では、回転する材料に対して固定された工具(バイト)を押し当てて削っていきます。切削方向は主に外径(円周方向)と軸方向(長手方向)です。旋削中は常に材料が中心軸に沿って回転しているため、対称性のある形状しか作れません。
4. 加工できる形状と精度の違い
加工形状 | フライス加工 | 旋盤加工 |
---|---|---|
平面 | ◎ | △(できないことが多い) |
円筒外径 | △ | ◎ |
円筒内径(穴) | ○ | ◎ |
溝加工 | ◎ | ○(外周溝に限る) |
歯車や複雑形状 | ◎ | × |
ねじ切り | ○(タップやねじ切り工具) | ◎(バイト使用) |
精度面では、旋盤加工は軸物の加工に特化している分、同心度や円筒度に優れています。一方フライス加工は平面度や直線度に強みがあります。
5. 加工対象素材の違い
どちらの加工法も金属、樹脂、木材など多種多様な素材に対応できますが、用途に応じた向き不向きがあります。
- フライス加工: 複雑形状を削り出す用途で使用。アルミ、鉄、ステンレス、真鍮など。
- 旋盤加工: 丸棒状の素材が前提。自動車部品やシャフトなどで使われるS45CやSCM材、黄銅棒などが多い。
6. 加工コストと生産性の違い
加工コストは加工時間、段取り、工具寿命など多くの要因に左右されますが、概ね以下の傾向があります。
- 旋盤加工の方が加工時間は短くなりやすい(円筒形状に特化しているため)
- フライス加工は段取りが多くなりやすい(多面加工・複雑形状が多いため)
- 単純な丸物部品は旋盤加工のほうがコスト低減可能
7. 自動化・NC制御の観点から見た違い
近年ではNC旋盤やマシニングセンタなど、自動化された設備が主流となっています。
項目 | NCフライス(マシニングセンタ) | NC旋盤 |
---|---|---|
自動工具交換 | 可能(ATC) | 機種による |
バー材の連続加工 | 不可(1チャックごと) | 可(バーフィーダーによる自動供給) |
加工の自由度 | 高い(3軸、5軸制御可能) | 制限あり(円筒形状が主) |
自動化のしやすさ | 高度なプログラミングが必要 | 汎用的なパターンで自動化しやすい |
8. 現場での使い分け事例
事例1:自動車のシャフト部品
- 加工内容:外径、段差、ねじ切り
- 適用加工法:旋盤加工
- 理由:対称形状で加工効率が高く、NC旋盤による自動加工が可能
事例2:ロボットの関節用ブラケット
- 加工内容:平面、穴あけ、ポケット形状
- 適用加工法:フライス加工
- 理由:複雑な形状を多面から加工する必要があるため
事例3:カメラ部品(精密小物)
- 加工内容:外径加工後に溝入れ、ねじ切り、面取り
- 適用加工法:旋盤加工+フライス加工の複合
- 理由:精密な円筒形状と部分的な穴や切り欠きの併用
9. 両者を組み合わせたハイブリッド加工の可能性
最近では、1台の工作機械でフライスと旋盤の両方を行える「複合加工機」が登場しています。これにより、加工効率の向上と段取り時間の短縮が可能になっています。
- 例:Mazak INTEGREXシリーズ、DMG MORI NTシリーズ
- **特徴:**主軸回転(旋削)とミーリング加工の両立
- **メリット:**工程集約によるコスト削減、位置ずれリスク低減、サイクルタイム短縮
10. 加工方式選定のチェックポイント
最後に、どちらの加工法を選定すべきかを判断する際のポイントをまとめます。
チェック項目 | フライス加工が向く場合 | 旋盤加工が向く場合 |
---|---|---|
加工形状 | 平面、溝、複雑形状 | 円筒形状、軸物 |
加工精度 | 直線度、平面度を重視 | 同心度、真円度を重視 |
加工数 | 少量試作にも対応しやすい | 多数ロットで効率的 |
自動化 | 3軸以上の動きが必要な場合 | 単純な形状で連続加工 |
設備保有状況 | マシニングがある | NC旋盤がある |
加工費用 | 工数が多くなりがち | 単価を下げやすい |
11. まとめ
フライス加工と旋盤加工は、どちらも切削加工の代表的な手法であり、それぞれに適した用途や得意分野があります。平面・複雑形状の加工にはフライス加工、軸物・円筒形状の加工には旋盤加工が最適です。製品の形状、精度要件、生産数量、加工コスト、設備の有無などを総合的に判断し、適切な加工法を選定することが、品質と効率の両立につながります。
さらに、近年では複合加工機によって両者の長所を活かしたハイブリッド加工も普及しており、製造現場の生産性を一段と高めるソリューションとなっています。
切削加工を理解し、適切な加工方法を選ぶことで、製品開発・量産体制において大きなアドバンテージを得ることができるでしょう。