ステンレス切削に必要な工具の基礎知識
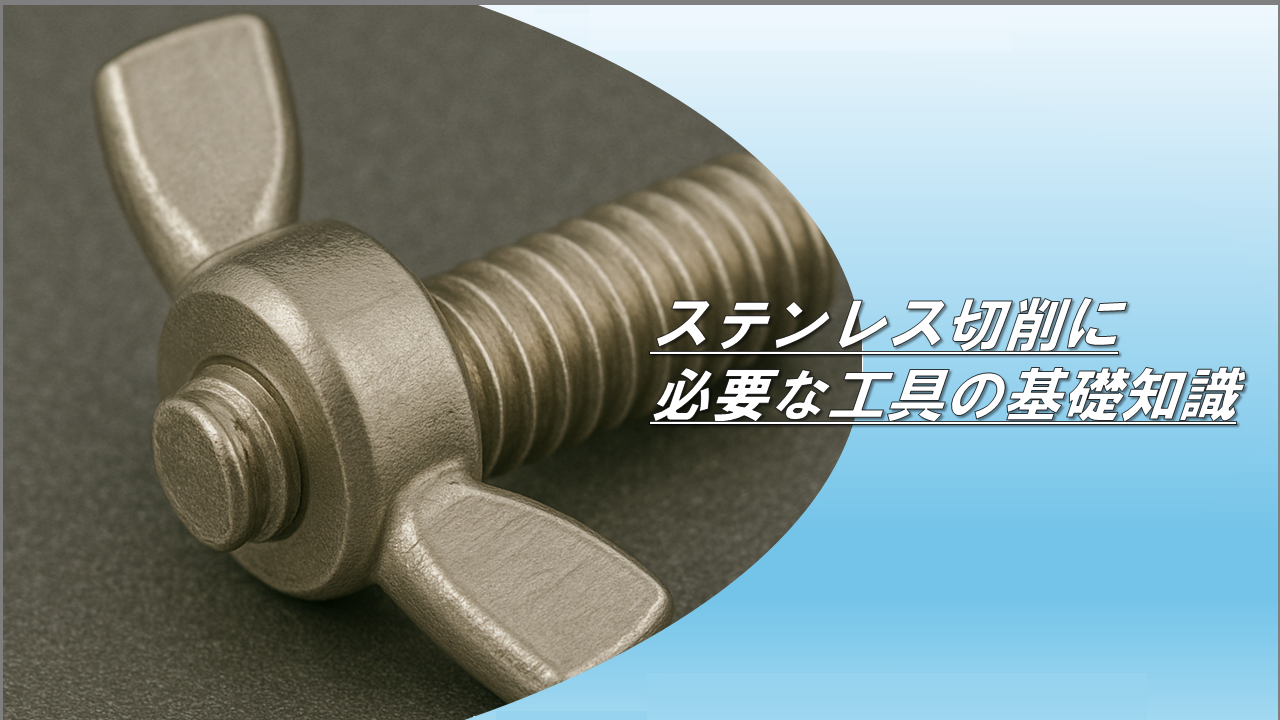
はじめに
ステンレス鋼はその優れた耐食性や強度から、建築、医療機器、食品機械、自動車部品など多岐にわたる分野で使用されています。一方で、その切削加工は非常に困難で、一般的な鋼材とは異なる特性を有しているため、専用の工具と適切な条件設定が不可欠です。
本記事では、ステンレスの切削に必要な工具の基礎知識について解説し、適切な工具の選定方法、推奨される切削条件、トラブル回避のポイントなどを詳述します。
1. ステンレス鋼の切削加工が難しい理由
ステンレスの切削には、以下のような困難さが伴います。
1-1. 高い加工硬化性
ステンレスは加工中に急速に硬化する性質(加工硬化)があります。このため、切削中に被削材の表面が硬くなり、工具摩耗が激しくなります。
1-2. 熱伝導率の低さ
熱が工具先端部に集中しやすく、切削中に温度が上昇し、工具の寿命を縮める要因になります。
1-3. 粘り強さによる切りくず排出性の悪さ
ステンレスは粘りがあるため、切りくずが長くなりやすく、巻き付きや再切削による刃先損傷のリスクが高まります。
1-4. 焼き付きや溶着が起きやすい
高温・高圧条件下で切りくずが刃先に溶着する「焼き付き」が発生しやすいため、工具寿命が著しく低下します。
2. ステンレス切削に適した工具材料
2-1. 超硬合金(Cemented Carbide)
ステンレスの切削において最も一般的な工具材料。高硬度と高耐摩耗性を兼ね備えています。被膜コーティングとの組み合わせにより性能がさらに向上します。
代表的なコーティング例:
- TiAlN(チタンアルミナイトライド)
- AlCrN(アルミクロムナイトライド)
- DLC(ダイヤモンドライクカーボン)※一部用途
2-2. ハイス(高速度鋼)
超硬に比べると耐摩耗性は劣るものの、靱性があり、主にドリルやタップなど、衝撃負荷のかかる工具に使用されます。
2-3. セラミック工具・CBN工具
加工硬度の高いステンレスや高温下の切削に適するが、脆性が高いため注意が必要。主に仕上げ加工や高能率切削に用いられます。
3. 切削工具の形状と選定ポイント(加筆修正版)
ステンレス鋼の切削では、加工中に発生する高熱や硬化、粘性によるトラブルに対応するため、工具形状の適切な選定が極めて重要です。工具の幾何形状、刃数、切れ刃の角度、チップポケットの設計などは、加工安定性や工具寿命、さらには仕上げ面の品質に直結します。
以下に、代表的な工具種ごとに最適な形状および選定時の留意点を詳述します。
3-1. エンドミル
用途: フライス加工、側面加工、溝加工、ポケット加工など
選定ポイント:
- 刃数の選定:
ステンレスは切りくず排出性が悪いため、2〜4枚刃が望ましい。4枚刃以上の場合はチップポケットが狭くなり、切りくず詰まりや焼き付きの原因になる。 - 切れ刃の角度(すくい角):
ポジティブ(鋭角)なすくい角を持つものが切削抵抗を軽減し、工具摩耗を抑制する。ただし、すくい角が大きすぎると刃先が脆弱になるため、バランスが重要。 - ねじれ角:
ステンレスの加工には**高ねじれ角(35~45°)**のエンドミルが適する。切りくずを効率的に排出し、焼き付き防止に貢献。 - コーナーR付きの刃先形状:
シャープな角部は欠けやすいため、**コーナーR(0.2〜0.5mm)**を付けることで寿命を延ばし、仕上げ面の品質を向上できる。 - 溝形状とチップポケットの設計:
切りくずが詰まりにくく、スムーズに排出される設計が重要。特に深いポケット加工時には排出性を優先する。
3-2. ドリル
用途: 穴あけ加工(下穴、通し穴、止まり穴など)
選定ポイント:
- 先端角:
ステンレス鋼は硬く、逃げが少ないと穴の入りが悪くなるため、**先端角130〜140°**の広めのタイプが推奨される。 - 芯厚設計:
芯厚が薄いと切削抵抗が小さくなるが、剛性が下がるため、バランスの取れた芯厚が理想的。 - クーラント供給方式:
焼き付き防止と切りくず排出のため、内径給油式(内部クーラント)ドリルが望ましい。 - 外径形状(ストレート・段付き):
加工対象に応じて、段付きドリルやステップドリルを選ぶことでバリの抑制や加工安定性を向上させられる。 - 溝のねじれ角:
切りくずの排出性を高めるため、**高ねじれ型(30〜40°)**が適している。
3-3. タップ
用途: ネジ切り加工(ねじ山の形成)
選定ポイント:
- ねじのタイプに応じた選定:
- スパイラルタップ:貫通穴向け。切りくずが上方へ排出される。
- スパイラルフルートタップ:止まり穴向け。切りくずが下方へ排出される。
- ポイントタップ:高能率で貫通穴に適するが、切りくずの排出性が求められる。
- ねじ部の表面処理:
ステンレス加工ではTiNやTiAlNコーティングなどの表面処理により、摩耗や焼き付きのリスクを軽減できる。 - ピッチやねじ山角の精度:
ステンレスは加工硬化しやすいため、ねじ山の変形やバリ発生を防ぐ高精度タップを選定すべき。
3-4. 旋削用インサート
用途: 旋盤による外径加工・内径加工・端面加工など
選定ポイント:
- 切れ刃形状:
ステンレスは粘性が高いため、鋭利なポジティブ型の切れ刃が摩擦と発熱を抑え、焼き付きの防止に有効。 - 逃げ角・すくい角の調整:
ステンレス向けには**大きめのすくい角(+10°前後)**が好まれ、切れ味を重視する構成が推奨される。 - コーナーRの選定:
加工面の仕上げや耐欠損性の両立のためにR0.2〜R0.8が一般的。必要に応じて仕上げ用と荒加工用を使い分ける。 - チップグレード(ISOコードM材):
ステンレス向けは**ISO材種 M(ステンレス鋼用)**が基本。メーカー指定の「ステンレス用グレード」の使用が最も安全。 - チップブレーカー設計:
長い切りくずの排出を助ける深い溝設計やチップ巻き防止構造を持つものが適する。
3-5. 特殊工具(バニシングツール、面取り工具 など)
- バニシングツール:仕上げ面の光沢を向上させるために使用。変形の抑制や摩耗の最小化に貢献。
- 面取り工具:ステンレスのようにバリが出やすい素材では、カッター刃数の多い面取り工具を使うとエッジ仕上げが綺麗に仕上がる。
4-1. TiAlN(チタンアルミナイトライド)
耐熱性と酸化安定性に優れ、ドライ加工でも安定。高速加工向け。
4-2. AlCrN(アルミクロムナイトライド)
耐摩耗性に優れ、湿式・ドライ両対応。工具寿命の延命に寄与。
4-3. DLCコーティング
超低摩擦、冷間加工や微細加工に適するが、耐熱性が劣るため高温には不向き。
5. ステンレス切削で推奨される切削条件
5-1. 切削速度(Vc)
工具寿命を大きく左右する要素。ステンレス304の場合、一般的には20〜60 m/min。
5-2. 送り速度(f)
工具の種類により異なるが、過大な送りは焼き付きの原因になるため、適正範囲(例:ドリルで0.1〜0.2 mm/rev)を守る。
5-3. 切り込み量(ap)
加工の安定性を確保するため、ステンレス特有の「弾性変形による戻り」を考慮し、十分な切り込みが必要(例:ap > 0.2mm 推奨)。
6. クーラントの役割と選定
6-1. 冷却と潤滑の二重効果
- 刃先温度の抑制
- 焼き付き・溶着の防止
- 切りくずの洗浄と排出性向上
6-2. クーラントの種類
- 水溶性切削液(エマルジョン型):冷却性に優れ、多くのステンレス加工に適する
- 油性切削液(ミスト加工):ネジ加工やタップ加工に好適
7. 加工トラブルを防ぐための工具管理術
7-1. 工具摩耗の監視
- 刃先の変色やチッピングを定期確認
- 工具管理表で使用時間を管理
7-2. 工具の再研磨と再利用
- 超硬工具は複数回再研磨可能
- 切削性能が戻ることでコスト削減に寄与
7-3. 工具ホルダーとの相性
- ホルダー剛性の確保
- 過度な振れやたわみが寿命を縮めるため、工具とホルダーのマッチングが重要
8. 加工精度と工具選定の実務的アドバイス
- 高精度加工には小さな刃先R:コーナー部の仕上げ品質を向上
- 深穴加工には内部給油機能:ドリル折損リスクの低減
- 自動化ラインでは長寿命型インサート:段取り回数を最小化
まとめ
ステンレス切削加工は、工具の選定と条件設定次第でその効率と品質が大きく左右されます。加工硬化や焼き付きといったステンレス特有の課題に対応するためには、適切な工具材料、刃先形状、コーティング、そしてクーラントの選定が不可欠です。
また、日々の工具管理を徹底し、摩耗状態の把握や再研磨の活用など、メンテナンス面にも気を配ることで、安定した加工とコスト削減を両立することが可能になります。