ステンレス切削におけるクーラントの役割と種類
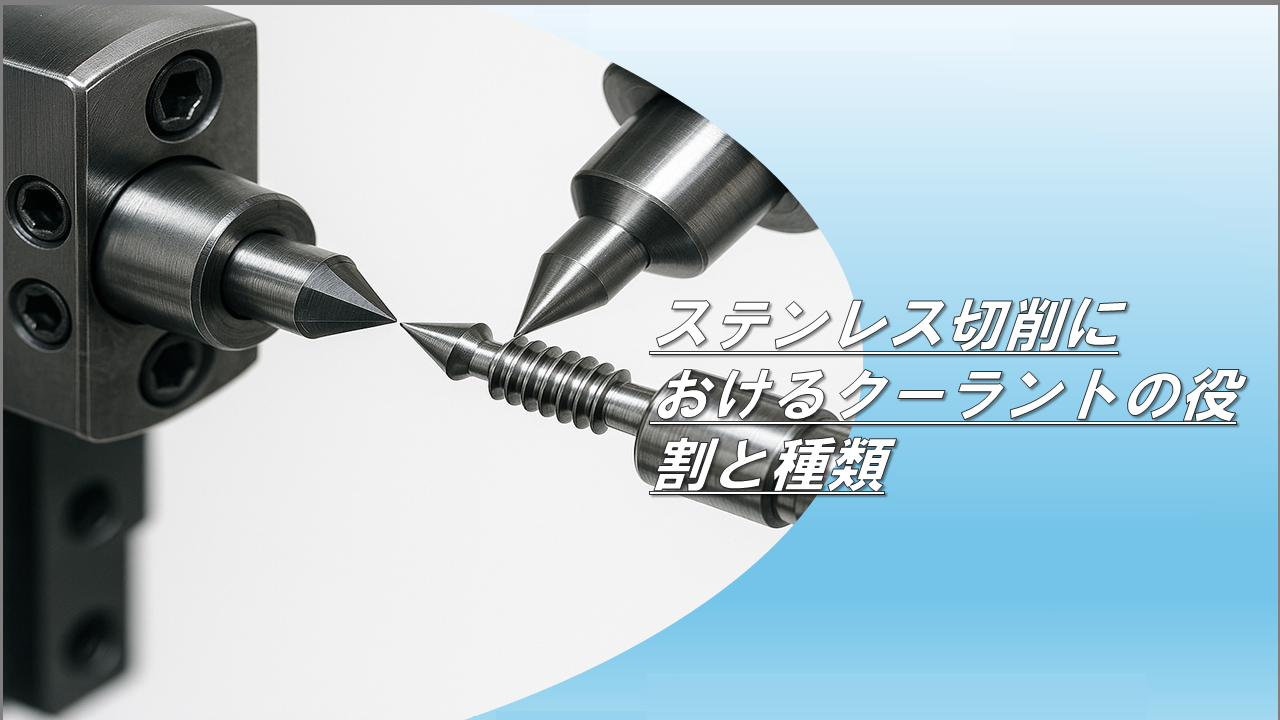
はじめに
ステンレス鋼は耐食性や強度に優れた素材であり、食品機械、医療機器、建築部材、自動車部品など多様な分野で使用されています。しかしその一方で、切削加工においては「加工硬化が強い」「熱伝導性が低い」「工具との反応性が高い」といった加工性の悪さが指摘されており、工具摩耗やビビリ、焼付きなどのトラブルを招く原因となります。
このようなステンレス切削において、クーラント(切削液)の適切な使用は、加工の安定性、工具寿命の延長、品質の向上において非常に重要です。本記事では、ステンレス切削におけるクーラントの役割と種類、選定のポイント、使用上の注意点までを詳しく解説していきます。
第1章:クーラントの基本的な役割
クーラントは切削中の工具とワークに供給される液体であり、主に以下の4つの役割を担っています。
1-1. 冷却作用
ステンレスは熱伝導率が低いため、切削時に発生した熱が工具先端に集中しやすくなります。これにより工具寿命が著しく低下する原因になります。クーラントを使用することで、
- 工具の先端温度を下げる
- 熱による寸法誤差を低減する
- 焼付きや溶着を防ぐ
といった効果が得られます。
1-2. 潤滑作用
潤滑作用は摩擦を減らし、工具の摩耗を抑える効果があります。特に仕上げ加工では、クーラントによる潤滑で切削抵抗が減少し、良好な面粗度が得られます。
1-3. 洗浄作用
切削くずや摩耗粉、汚れを洗い流す作用も重要です。これにより切りくずの再切削や工具への巻き付きが防止され、切削トラブルが低減します。
1-4. 防錆作用
クーラントの成分には、機械や加工品の錆を防止する防錆剤が含まれています。特に水溶性クーラントを使用する場合には重要な機能です。
第2章:ステンレス切削に適したクーラントの種類
クーラントはその成分や形態によりいくつかの種類に分類されます。ステンレス加工に適するのはどのようなものか、代表的なクーラントの種類と特徴を見ていきましょう。
2-1. 油性クーラント(切削油)
特徴:
- 潤滑性に優れる
- 冷却効果は水溶性に劣る
- 面粗度の向上や工具寿命の延長に効果的
適用例:
- 低速〜中速加工(旋削やねじ切り)
- 仕上げ加工
- ドリル・タップ加工
注意点:
- 引火の危険があるため火気管理が必要
- ミストによる健康被害リスクがある
2-2. 水溶性クーラント(エマルジョンタイプ)
特徴:
- 水と油の混合液
- 冷却性が高く、高速加工に適する
- 環境負荷が比較的少ない
適用例:
- 高速フライス加工
- 自動加工機(マシニングセンタなど)
注意点:
- 雑菌繁殖や腐敗のリスクがある
- 防錆剤の管理が必要
2-3. 合成クーラント
特徴:
- 油分を含まない合成成分
- 透明性が高く、切削状況の視認性が良い
- 高い洗浄効果を持つ
適用例:
- 精密部品加工
- 洗浄性が求められる分野
注意点:
- 潤滑性が油性より劣る
- 錆びやすいため管理が重要
2-4. 半合成クーラント(セミシンセティック)
特徴:
- 合成クーラントと水溶性クーラントの中間
- 冷却性と潤滑性のバランスが良い
- 近年では主流になりつつある
適用例:
- 多品種少量生産に対応する加工現場
注意点:
- 成分管理がやや複雑
第3章:クーラントの供給方法と使用形態
ステンレス切削でのクーラント供給方法は、加工精度や生産性に大きな影響を与えます。以下に主な供給方法を紹介します。
3-1. 外部供給方式(外がけ)
工具外部からノズルでクーラントを供給する方法です。
- 特徴:設備コストが低く、メンテナンス性が高い
- 問題点:工具と切削部への到達性が悪いこともある
3-2. 内部供給方式(スルークーラント)
工具内部に穴を設け、クーラントを先端に直接供給する方式です。
- 特徴:深穴加工や高速加工に有効
- 効果:チップの排出性向上、焼付き防止に効果大
- デメリット:工具・設備コストが高い
3-3. ミスト供給方式
微細なクーラントを霧状にして供給する方式です(MQL=最小量潤滑)。
- 特徴:環境負荷が少なく、廃液処理も容易
- 注意点:高負荷加工には不向き
第4章:クーラント選定時のポイント
ステンレス切削に最適なクーラントを選定するには、以下の要素を考慮する必要があります。
4-1. 加工内容と速度
- 高速加工:冷却性重視 → 水溶性クーラントが有効
- 低速・仕上げ加工:潤滑性重視 → 油性クーラントが適する
4-2. 加工方式
- 旋削やフライス加工などの切削加工:冷却重視
- タップ加工やねじ切り:潤滑性が最優先
4-3. 加工材の種類
SUS304・SUS316などのオーステナイト系ステンレスは加工硬化が大きく、熱と摩擦に弱いため、冷却と潤滑の両立が求められます。
4-4. 作業環境・安全性
- 引火リスクのある現場 → 水溶性や合成クーラントが好ましい
- 健康被害リスク(皮膚炎、呼吸器)にも配慮が必要
第5章:クーラント管理とトラブル対策
クーラントは使用しているうちに劣化し、性能が低下していきます。以下のような点を日常管理することで、トラブルを未然に防ぐことができます。
5-1. 濃度管理
水溶性クーラントは、推奨濃度を守ることで効果を最大限に発揮できます。濃すぎると粘度が高くなり、泡立ちや異臭の原因になります。薄すぎると潤滑性・防錆性が失われます。
5-2. 異物除去とフィルター管理
切りくずや油膜、微細な異物がクーラントに混入すると性能低下や配管詰まりの原因になります。定期的なフィルター交換や清掃が必要です。
5-3. 腐敗・悪臭対策
菌類や藻類の繁殖により腐敗が起きると悪臭や皮膚炎の原因になります。防腐剤の添加や定期的なクーラントの交換が求められます。
第6章:最新トレンドと環境配慮
6-1. MQL(最小量潤滑)加工の普及
環境配慮の観点から、MQL(Minimum Quantity Lubrication)による加工が注目されています。極めて少量の潤滑剤で加工を行うため、廃液の発生が少なく、作業環境もクリーンに保たれます。
6-2. バイオ系クーラントの導入
植物性油脂や天然由来の添加剤を使用した環境対応型のクーラントも登場しています。廃液処理の負担が軽く、SDGsやISO14001への対応としても有効です。
まとめ
ステンレス切削におけるクーラントは、加工精度と工具寿命、さらには作業者の安全性にも大きく関わる重要なファクターです。切削条件に適したクーラントの選定と適切な使用・管理により、安定した加工が実現し、コスト削減や品質向上にもつながります。
- 冷却・潤滑・洗浄・防錆の4大機能を理解すること
- 油性・水溶性・合成・半合成それぞれの特徴を把握すること
- 加工内容や設備に応じた供給方法を選択すること
- 定期的な濃度管理・清掃・交換を怠らないこと
これらを意識することで、ステンレスの難削材としての課題にも十分対応できる強い加工現場を構築することが可能です。