ステンレスとは?その特徴と加工の難しさ
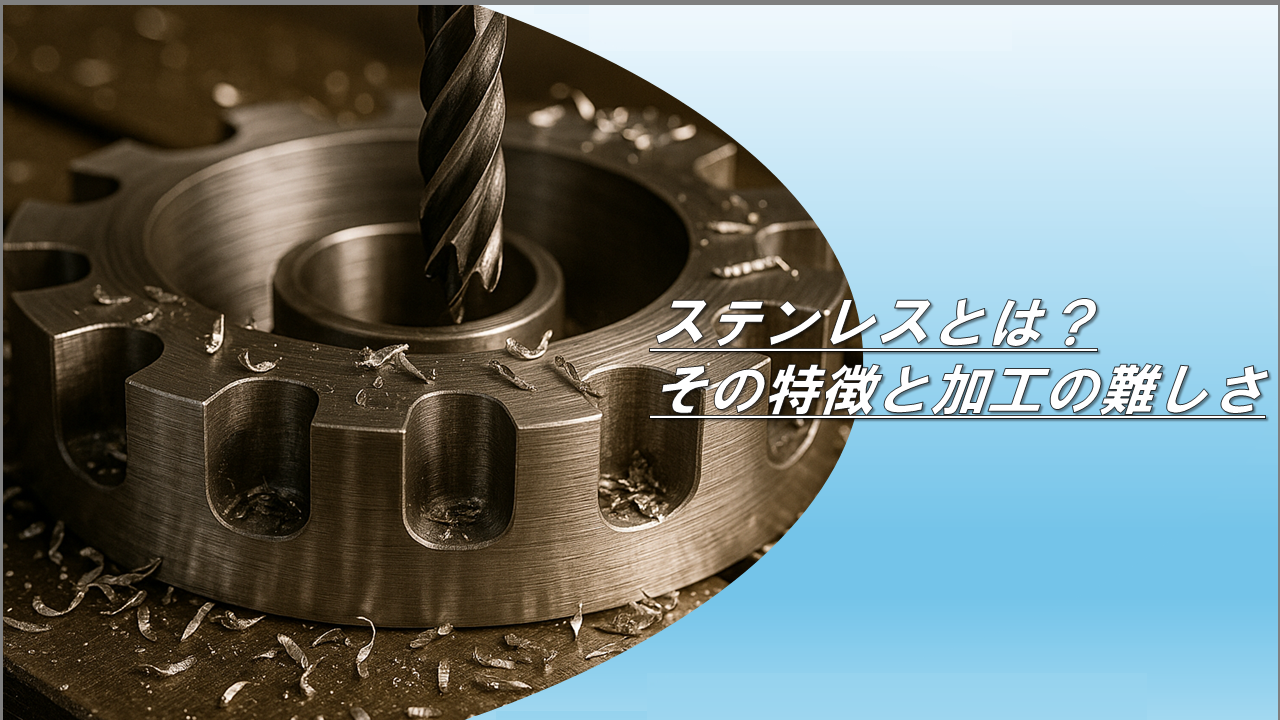
はじめに
金属材料の中でも、建築、自動車、医療機器、食品機械、家庭用品など、さまざまな分野で活躍する素材に「ステンレス鋼(以下、ステンレス)」があります。鉄を主成分に、クロム(Cr)やニッケル(Ni)などを添加して作られるステンレスは、「錆びにくい」「強度が高い」「衛生的」といった特性を持ち、私たちの生活を支える重要な金属材料です。
しかし、その優れた特性の裏には、加工の難しさという技術的な課題が存在します。本稿では、ステンレスの基本的な性質や分類から、具体的な加工の難しさ、そしてそれに対する対処法まで、詳しく解説します。
1. ステンレスとは何か?
1-1. ステンレスの定義
「ステンレス」とは、「ステイン(stain)=汚れ・錆」と「レス(less)=少ない」という英語を語源とし、「錆びにくい鋼(Stainless Steel)」を意味します。
JIS(日本産業規格)では、ステンレス鋼は「クロム含有量10.5%以上、炭素含有量1.2%以下の耐食性を持つ鋼」と定義されています。一般的には、クロムの含有量を増やすことで、鉄が酸化して錆びるのを防いでいます。
1-2. ステンレスの主な合金成分と役割
元素 | 役割 |
---|---|
クロム(Cr) | 酸化皮膜(不動態皮膜)を形成し、耐食性を付与 |
ニッケル(Ni) | 延性・靱性を向上させ、オーステナイト組織を安定化 |
モリブデン(Mo) | 塩素系環境下での耐食性を強化 |
炭素(C) | 少量であれば硬度や強度を上げるが、多すぎると耐食性を下げる |
2. ステンレスの代表的な種類とその特徴
ステンレスはその組織により、以下のような分類がされます。
2-1. オーステナイト系ステンレス鋼(例:SUS304、SUS316)
- 非磁性(ただし冷間加工で若干磁性を帯びることも)
- 耐食性・加工性に優れる
- ニッケルを多く含み価格が高め
- 代表例:SUS304(最も汎用的)、SUS316(モリブデン添加で耐塩素性向上)
2-2. フェライト系ステンレス鋼(例:SUS430)
- 磁性あり
- 耐食性はオーステナイト系に劣るが安価
- 高温強度や溶接性はやや劣る
- 家電製品や内装材によく使われる
2-3. マルテンサイト系ステンレス鋼(例:SUS410、SUS420)
- 熱処理によって硬化可能
- 刃物・工具・バルブなど、機械的強度重視の用途に使用
- 耐食性は他の系に比べて劣る
2-4. 二相系ステンレス鋼(オーステナイト+フェライト)
- 強度と耐食性のバランスが良い
- 石油化学プラントなど、過酷環境下での使用が多い
3. ステンレスの特性(メリット)
ステンレスがこれほど広く使われる理由は、その多機能性にあります。
3-1. 高い耐食性
ステンレスは表面に**不動態皮膜(酸化クロムの薄膜)**を自然に形成し、この皮膜が錆の進行を防ぎます。傷ついても空気中の酸素と反応してすぐに再生されるため、自己修復性も持ちます。
3-2. 強靭性・靱性に優れる
オーステナイト系ステンレスは、極低温(-196℃)でも靱性を保つため、LNGタンクなどにも使用されます。
3-3. 加工後の美観が良い
研磨や電解研磨、ヘアライン処理などが可能で、美観性に優れ、建築外装や厨房機器など意匠性が求められる分野で活躍します。
3-4. 耐熱性・耐薬品性
一定温度下でも安定性が高く、化学プラントや医療機器でも使用されます。
4. ステンレス加工の難しさとは?
一方で、ステンレスには以下のような加工上の課題があります。
4-1. 熱伝導率が低く、加工熱が逃げにくい
ステンレスは熱伝導率が低いため、切削加工時に発生する熱が刃先や加工面に集中します。この結果、刃物の摩耗が早く、加工面も荒れやすくなります。
4-2. 加工硬化しやすい
特にオーステナイト系は加工硬化性が高く、切削中に材料が局所的に硬化し、刃物が急激に摩耗したり、ビビり振動が発生したりします。
4-3. 切りくずが長く、絡みやすい
切りくずがダラダラと長く出る傾向があり、チップブレーカーやクーラントの工夫が必要です。
4-4. 工具寿命が短くなりがち
高硬度や加工熱の蓄積により、切削工具の寿命が著しく短くなるケースが多いです。耐摩耗性の高い工具材やコーティングが必要です。
5. ステンレス加工における対策と工夫
5-1. 加工条件の最適化
- 低速・高送りが基本(特に加工硬化対策として)
- 深切りしすぎず、適切な切込み深さを確保
- 必要に応じて**多段階加工(荒→中→仕上げ)**を導入
5-2. 工具の選定
- **コーティング超硬工具(TiAlNなど)**の使用
- 切れ味重視ならセラミック工具も選択肢
- ドリルやタップもステンレス専用設計品を選定
5-3. クーラントの使い方
- 高圧クーラントの活用で切りくず排出性を向上
- 冷却重視の水溶性クーラントが基本
- 加工点へピンポイントで供給
5-4. ビビり対策
- 剛性の高いホルダーを使用
- ワークの固定剛性を上げる
- 加工パスの見直しや工具突出し量の最小化
6. 加工方法別|ステンレス加工のポイント
6-1. 切削加工
- フライス加工:工具の逃げ角や刃数が重要
- 旋盤加工:オーステナイト系ではバリが出やすく注意
- 穴あけ加工:ドリルのチッピングや摩耗が起きやすい
6-2. 溶接加工
- 溶接後に応力腐食割れや結晶粒の粗大化が起きやすい
- TIG溶接やレーザー溶接で精密な制御が可能
- 酸洗いや電解研磨による酸化被膜除去が必要
6-3. 研磨・表面処理
- 不動態皮膜を損なわずに仕上げるには、電解研磨やバフ研磨が有効
- 加工後の脱脂・洗浄で表面品質を保つ
7. ステンレス加工現場での実践例
- 自動車部品ではSUS304のプレス部品が多く、金型への耐摩耗性加工が重要
- 医療機器ではSUS316Lが多用され、バリレス加工と研磨処理が必須
- 食品機械では衛生管理を意識した溶接部の処理が重要視される
8. 今後の展望と技術革新
8-1. ステンレス加工機の進化
- 5軸マシニングセンタの普及により複雑形状の加工が可能に
- 高圧クーラント搭載CNC旋盤の活用が進む
8-2. AIとIoTの導入
- 工具摩耗予測や加工異常検知にAIセンシングが活躍
- 工程監視による不良品削減・歩留まり向上
まとめ
ステンレスは、その優れた耐食性や美観性から、多様な産業で不可欠な素材です。一方で、加工が難しく、工具寿命や熱処理、切りくず排出など、さまざまな技術的課題が存在します。
しかし、これらの課題に対しては適切な加工条件の選定や工具・設備の工夫により、十分に対応可能です。今後は、より高性能な工具開発や加工自動化技術の進展により、ステンレス加工の生産性・品質はさらに向上していくでしょう。