ろう付け接合部の強度評価方法 ~信頼性と品質を支える評価技術~
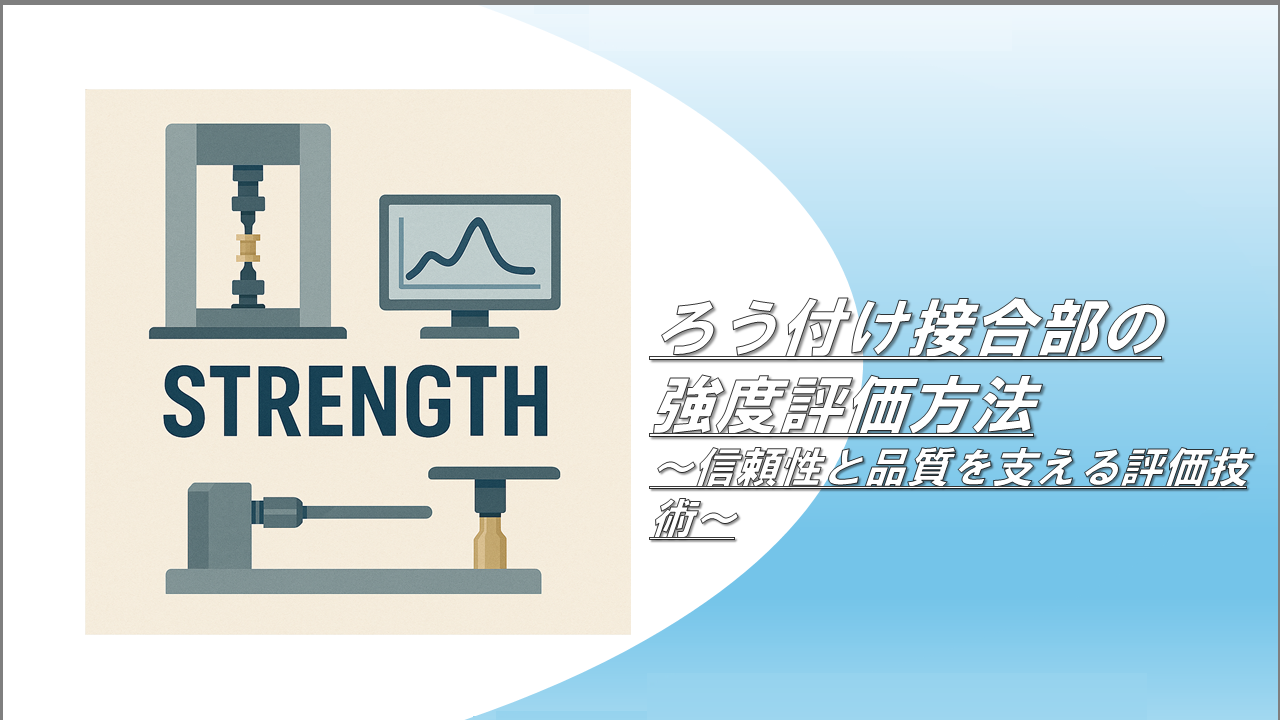
はじめに
ろう付け(brazing)は、金属材料の接合技術として多様な産業分野で利用されています。特に、自動車部品、空調機器、電子部品、医療機器など、高い信頼性と精密性が要求される製品においては、ろう付け接合部の強度が製品全体の性能や安全性を左右します。したがって、接合部の強度評価は非常に重要です。
本稿では、ろう付け接合部の強度評価方法について、実験的手法、非破壊評価、シミュレーション評価を含めて体系的に解説します。また、JIS(日本産業規格)に基づく評価指針や、評価に関する実務的な注意点についても触れます。
1. ろう付け接合部に求められる強度とは?
1-1. 接合強度の基本概念
ろう付けにおける接合強度とは、接合された部品が外力(引張、せん断、曲げ、圧縮など)に対してどれだけ耐えられるかを示す指標です。接合強度は、使用するろう材、母材、接合条件、接合形状、接合面の清浄度などに大きく依存します。
1-2. 強度評価の目的
強度評価には以下の目的があります:
- 製品設計時の安全率の確保
- 製造条件(温度、時間、ろう材量など)の最適化
- 製造後の品質管理と合否判定
- 使用中における信頼性確認
- 不具合解析や改善策の立案
2. 強度評価の方法:破壊試験
ろう付け接合部の機械的強度を数値として明確に評価する最も基本的な手法が「破壊試験」です。接合部に力を加えて意図的に破壊し、その破壊荷重や破壊様式から接合の性能を測定します。以下では、主要な破壊試験方法について詳細に解説します。
2-1. 引張試験(Tensile Test)
試験の目的:
接合部が引張荷重に対してどの程度耐えられるかを測定することで、接合強度の基礎データを得る。
試験片の形状:
JIS Z 3197に準拠し、母材の中央部にろう材を挟んで接合した「棒状試験片」を使用。標準的なサイズは、全長100 mm、接合部長さ10 mm、断面積は10 mm × 1 mmなどが指定されている。
試験手順:
- ろう付け済み試験片を万力または引張試験機に固定。
- 一定の速度(例:1 mm/min)で荷重を加える。
- 破断するまで引っ張り、最大荷重と破断モードを記録。
評価項目:
- 最大引張荷重(N)
- 引張強さ(MPa)=最大荷重 ÷ 接合部断面積
- 破断位置(ろう材内部、接合界面、母材)
活用事例:
- 銀ろう、銅ろうによる機械部品の強度設計
- JISやISO規格への適合性評価
注意点:
- 試験片の接合中心のずれにより応力集中が起こる場合がある
- 実製品の応力方向が引張でない場合は、補助的評価にとどまる
2-2. せん断試験(Shear Test)
試験の目的:
接合面に沿ってずらすような荷重(せん断力)に対する抵抗力を測定し、実使用時に近い応力状態での強度を評価する。
試験片の形状:
「ラップジョイント型」または「重ね継手型」試験片を使用。母材の端部同士を10~20 mm程度重ねてろう付けし、上下方向から力を加える。
試験手順:
- 接合された試験片を治具に取り付け、上下方向に荷重を加える。
- ろう付け部を中心にすべり破壊させる。
- 最大荷重と変位、破壊モードを測定する。
評価項目:
- 最大せん断荷重(N)
- せん断強度(MPa)=最大荷重 ÷ 接合面積
- 初期滑り、最大変位、破断面積
活用事例:
- 自動車用チューブ・フィン部品などの評価
- 小型電子部品のリード線接合評価
注意点:
- 接合面積のばらつきが評価結果に影響を与える
- 面圧・治具の摩擦などが誤差要因になるため、十分な再現性が必要
2-3. 曲げ試験(Bend Test)
試験の目的:
接合部の靱性(粘り強さ)や割れに対する耐性を評価し、ろう付け部の延性を調べる。
試験片の形状:
長方形の母材の中央にろう付けされた板状試験片(厚み1〜3 mm程度)。三点曲げまたは四点曲げ装置を用いる。
試験手順:
- 試験片を支持台の上に置き、中央または2点から下向き荷重を加える。
- 曲げ半径や曲げ角度を記録し、表面割れや剥離を観察する。
- 規定角度まで曲げられたかどうかを評価基準とする。
評価項目:
- 曲げ荷重(N)
- 曲げ角度(度)
- 表面割れの有無(合格/不合格)
活用事例:
- 熱交換器配管のろう付け評価
- 医療用チューブの接合健全性チェック
注意点:
- 破断に至らないため、強度値としての定量評価には向かない
- 曲げ半径や応力集中部の設計が適切でないと誤判断を招く
2-4. 圧縮試験(Compression Test)
試験の目的:
圧縮方向の荷重に対するろう付け接合部の変形抵抗性と強度を測定する。
試験片の形状:
円筒形または立方体形状の母材を上下に接合した試験片。寸法例:直径10 mm、高さ20 mmなど。
試験手順:
- 試験片を圧縮試験機にセット。
- 上部から一定速度で加圧し、変形・破壊に至るまで荷重を記録。
- 応力-ひずみ曲線を作成し、降伏点・最大応力などを評価。
評価項目:
- 最大圧縮荷重(N)
- 降伏点・変形開始点
- 圧縮強度(MPa)
活用事例:
- 高荷重下で使用される構造体のろう付け部(例:油圧機器、ベアリングハウジング)
注意点:
- ろう材の流れ不足が中央集中荷重によって明らかになる
- 形状バラつきによる座屈に注意
2-5. 破壊面の観察と解析
目的:
破壊後の接合面を観察することで、破壊の起点、形態、破壊の支配因子を特定する。
主な観察機器:
- 実体顕微鏡:肉眼で観察できないレベルの欠陥確認
- 金属顕微鏡:組織観察、ろう材と母材の界面評価
- SEM(走査型電子顕微鏡):微小なクラック、元素分析(EDX)との併用が有効
解析視点:
- 破壊モードの分類(ろう材内部破壊/界面破壊/母材破壊)
- ろう材の濡れ性の良否
- 酸化物や異物混入の有無
- 微細クラックの有無と分布
活用事例:
- 強度不良の原因究明
- ろう材と母材の相性評価
- フラックス残渣による界面腐食の判定
3. 非破壊検査による評価
破壊を伴わずに強度や接合の健全性を確認する方法もあります。これは製品の全数検査や使用前検査に有効です。
3-1. 超音波探傷試験(UT)
高周波の超音波を接合部に送信し、反射波から内部欠陥を検出します。未接合部、割れ、気孔、ブローホールなどの検出が可能です。
3-2. X線検査(RT)
X線透過画像を用いて内部構造を確認する方法で、電子部品や薄板接合での欠陥検出に適しています。画像解析による自動判定技術も進化しています。
3-3. 渦流探傷(ET)
導電性の部材に交流磁界をかけて発生する渦電流の変化から、接合異常を検知する方法です。薄肉部品や狭小部の検査に適しています。
4. シミュレーション評価と数値解析
実験に加え、CAE(Computer Aided Engineering)を用いた評価も盛んです。これは接合部の強度予測や最適化に役立ちます。
4-1. 有限要素解析(FEA)
接合部のモデルを作成し、荷重や熱履歴を加えた状態で応力分布や破壊挙動を解析します。材料特性やろう材の流動特性、残留応力の可視化にも有効です。
4-2. 熱応力解析
ろう付け時の急激な温度変化により発生する熱応力や歪みをシミュレーションし、クラック発生リスクを予測できます。
5. 強度評価におけるJIS規格と国際基準
日本国内では、以下のようなJIS規格がろう付け評価に利用されます。
規格番号 | 規格名称 | 内容 |
---|---|---|
JIS Z 3197 | ろう付け試験方法 | 引張・せん断などの試験手法の定義 |
JIS Z 3283 | 銀ろう | 成分や物理特性の規定 |
JIS Z 3280 | ろう材の分類 | 硬ろう・軟ろうの分類など |
また、海外では以下の規格も使用されます:
- ASTM B898(Brazed Joint Strength)
- AWS C3.2(Brazing Procedure and Performance Qualification)
これらの国際規格との互換性を意識することで、グローバル品質保証体制の構築が可能になります。
6. 評価時の実務的注意点
6-1. ろう付け面の前処理
接合前の洗浄や酸化膜除去の不備は、強度低下の主因となります。強度評価をする際には、試験片の表面状態を常に記録し、再現性を持たせることが重要です。
6-2. 接合条件のトレース
加熱温度、保持時間、ろう材量などの記録をしっかり管理することで、評価結果との因果関係が明確になります。特にトーチろう付けでは熟練度に依存するため、記録の標準化が重要です。
6-3. 試験片の形状と寸法精度
JISでは標準形状が指定されていますが、実際の製品形状とは異なる場合があります。現場で使用される部品の応力分布を考慮した評価方法を選定することが求められます。
7. 今後の展望:AIとIoTによる強度評価の自動化
近年では、製造現場へのAI・IoT技術の導入が進み、ろう付け強度の自動判定や不良予測が可能になりつつあります。主な技術例は以下の通りです:
- 画像処理AIによるX線画像の不良検出
- 機械学習による接合条件と強度の予測モデル
- IoT温度センサーを活用した加熱プロファイル記録と最適化
これにより、属人性の排除や品質の安定化が期待されます。
まとめ
ろう付け接合部の強度評価は、製品の安全性と信頼性を確保するために不可欠なプロセスです。破壊試験をはじめとする多様な手法を適切に組み合わせ、JISなどの規格に準拠した評価を行うことで、より高品質な接合体の製造が可能となります。また、今後はAIやシミュレーション技術の発展により、評価プロセスの効率化と高度化が進んでいくと期待されます。