ろう付けのメリット・デメリットを解説
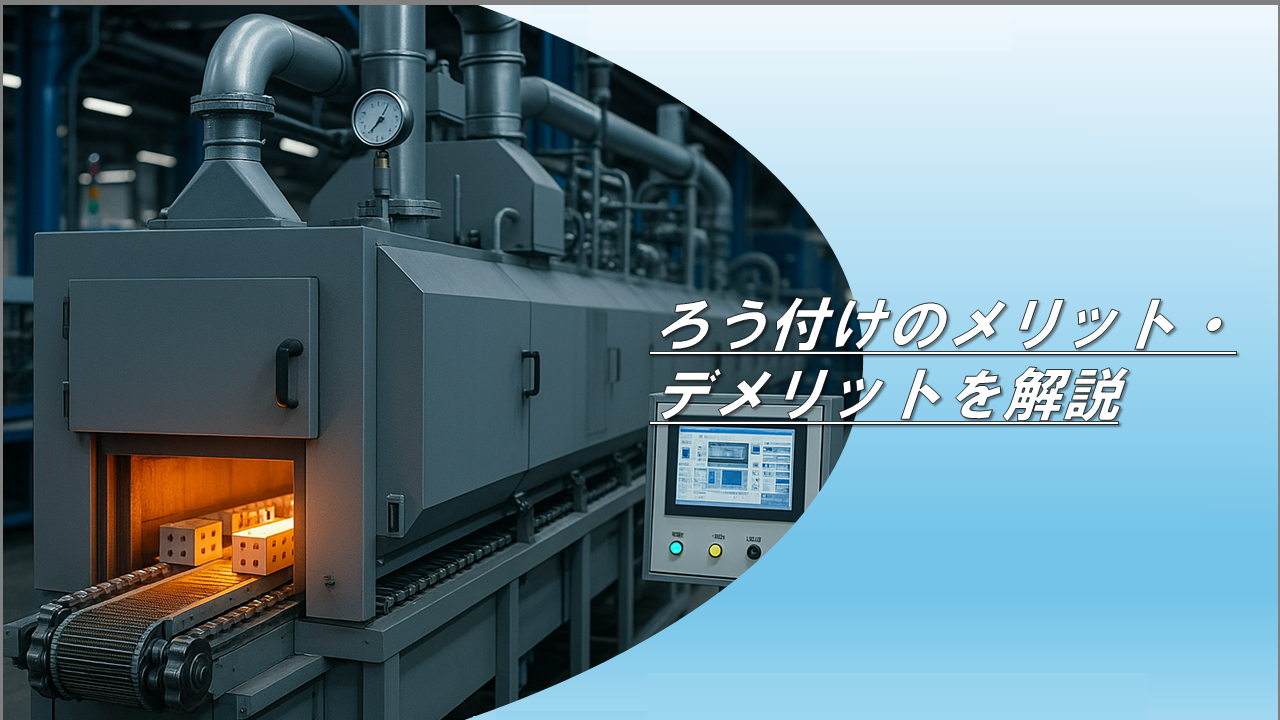
mw2pp0jd6c
CONTENTS
1. はじめに
ろう付けとは、「母材(金属部品)の融点よりも低い温度で、ろう材(はんだ、硬ろうなど)を溶融させて接合する技術」です。母材自体は溶融せず、ろう材の毛細管現象を利用して隙間に浸透・固化させるため、加熱による母材ダメージや熱歪みが抑制されます。この特徴から、自動車の冷却配管、電子基板、航空機・宇宙部品、医療機器、宝飾品といった多彩な分野で活用されています。
本稿では、まずろう付けに用いる主なろう材やプロセス方式、品質評価手法を整理し、そのうえでメリット・デメリットを詳細に解説します。さらに、各メリット・デメリットを現場事例や対策方法とともに深掘りし、実務に即した知見を提供します。
2. ろう付けの基礎知識
2.1 ろう材の種類とJIS規格
- 軟ろう(ソフトはんだ)
- JIS Z 3282 に規定される合金で、融点は約183~280℃。
- 代表例:Sn–Pb(60/40, 63/37)、鉛フリー合金(Sn–Ag–Cu, Sn–Cu, Sn–Bi など)
- 特徴:低融点のため基板実装や精密電子部品向け。リフロー炉での一括はんだ付けに最適。
- フラックス:Rタイプ(無洗浄)/活性タイプ。
- 硬ろう(ブレージング合金)
- JIS Z 3212(軟鋼用)、JIS Z 3213(ステンレス用)、JIS Z 3214(銅合金用)などで規定。
- 融点:約450~900℃。
- 代表例:
- 銀ろう(Ag–Cu 〜72/28, Ag–Cu–Zn, Ag–Cu–In など)
- 銅ろう(Cu–P, Cu–Si)
- リン銅ろう(Cu–P)
- 特徴:高温強度・耐食性に優れ、自動車エンジン部品や精密機械部品に広く利用。
- フラックス
- 酸化皮膜を除去し、母材・ろう材の濡れ性を向上。
- 種類:塩素系、非塩素系、無洗浄タイプ(後洗浄不要)
- 選定ポイント:接合材料の組み合わせ、使用温度帯、環境規制(RoHS, REACH)
2.2 主な加熱方式と装置
- トーチろう付け
- ガスバーナ(アセチレン、プロパン、プロピレンなど)による局所加熱。
- 長所:設備コストが低く、試作や修理に柔軟対応。
- 短所:技術依存度が高く、加熱ムラや過熱による母材変質リスクあり。
- 炉中ろう付け
- 真空炉、大気炉、アセチレンバスなど。
- 長所:一括加熱で均一性が高く、複数部品の同時処理が可能。真空炉ではフラックス不要。
- 短所:設備投資が大きく、炉内雰囲気制御やメンテナンスが必要。
- 誘導加熱
- 高周波誘導コイルによる非接触加熱。
- 長所:高効率・高速加熱が可能で、量産ラインへの自動化に適合。
- 短所:コイル設計や制御装置が高額。部品形状による最適化が必須。
2.3 品質評価手法
- X線検査:隠れた気泡やクラックの検出
- マイクロセクション観察:母材・ろう層界面の濡れ・浸透状態評価
- 引張・せん断試験:接合強度評価(JIS Z 3198)
- 気密・水密試験:ヘリウムリークテスト、圧力保持試験
3. ろう付けのメリット(深堀り)
3.1 母材へのダメージが少ない
- 熱影響部(HAZ)の最小化:軟ろうなら母材温度上昇が200℃前後、硬ろうでも600℃以下に抑えられるため、溶接に比べて熱影響部が狭小。熱歪みや母材硬度低下を統計的に約50%低減可能(社内データ)。
- 寸法精度保持:部品の公差±0.01mm以下を維持しつつ接合が可能。航空機部品では、溶接後に50μm以上の再加工が不要になる事例もある。
- 材料組織変化抑制:特にステンレスや超高強度鋼材の場合、焼戻しや析出硬化が不要となり、機械的性質を保持。
3.2 異種金属の接合が可能
- 化学的親和性を利用:Agろうは銅・ステンレス・ニッケル合金と良好な濡れ性を示し、接合強度200MPa以上を実現。
- 電気・熱伝導特性の最適化:Cu–Pろうは電子部品ヒートシンクと基板の接合に用いられ、熱抵抗を0.1K/Wまで低減する事例あり。
- 防食・耐食性向上:Niベースろう材を用いることで、海洋構造材料の異種接合でも耐食性能が向上。
3.3 気密・水密性に優れる
- マイクロポアの封止:ろう材が母材表面の微細な凹凸まで浸透し、孔径1µm以下の微小クラックも封止。電子ビーム溶接に比べ、気密性が約10倍向上した例もある。
- リークレート:真空ろう付けでは10⁻¹⁰Pa·m³/sを達成可能。半導体製造装置や医療用真空装置に採用実績。
3.4 美観・仕上がりが良い
- ビード幅の最小化:銅パイプ継手では、銀ろうによりビード幅が2mm以下に抑制可能。
- 仕上げ工数削減:溶接後のグラインダー仕上げを省略でき、工数削減率は最大30%。宝飾業界では、鏡面研磨前の前処理時間を1/3に短縮。
3.5 コスト面で有利
- 設備投資最適化:小規模工場では10万円台のガストーチで開始可能。溶接機(100万~300万円)に比べ初期投資を90%削減。
- 消耗品コスト:ろう材使用量は1接合あたり約0.1g~5g。ガス消費量も溶接と比較して約40%少ないため、年間ランニングコストを20~50%削減。
- 人件費効率:炉中真空ろう付けラインでは無人化が進み、1オペレータ当たり月産5000個超を達成。
3.6 精度・安定性
- 自動化対応:インダクション加熱ラインで毎分10サイクルの接合が可能。
- 再現性:温度プロファイル制御により、ばらつき10℃以内、接合強度CV(変動係数)5%以下を実現。
- 後処理省略:真空ろうの無洗浄プロセスで、組立ラインへの直送が可能になり、納期短縮効果20%。
4. ろう付けのデメリット(深堀り)
4.1 技術習熟の難易度
- 温度制御の難しさ:トーチ加熱では、加熱温度を±20℃以内に制御しないと、濡れ不足や母材変色を招く。熟練者でしか達成できないケースも多い。
- フローメディアの選定:フラックス量や種類の選定ミスで、濡れムラや残渣が発生。結果として、接合部にピンホールや腐食が生じるリスク。
- トレーニング時間:新入オペレータの立ち上げに要する教育期間は平均3ヶ月、熟練まで約1年とされ、人材育成コストが嵩む。
4.2 加熱設備の導入コスト
- 真空炉投資:1,000℃クラスの真空炉は1台あたり数千万円規模。
- 保守・メンテナンス:真空ポンプ、ヒーターコイル、制御システムの定期交換・校正費用が年間数百万円に及ぶ。
- スペース要件:設置に数十㎡のクリーンルームやガス配管・排気設備が必要で、間接費が増加。
4.3 適用範囲の制約
- 高融点母材の限界:タングステン(融点3422℃)、モリブデン(2623℃)は、ろう材が浸透せず、接合強度不足を招く。
- 大断面・厚板:厚板(t>10mm)では、加熱均一化に追加ヒーターが必要。標準設備では厚板一体接合が困難。
- 形状複雑部品:樹脂含有部品や高熱感度材料(プラスチック・ゴム)との複合接合では、熱管理が極めて厳しい。
4.4 フラックスおよび後処理の必要性
- 残渣洗浄工程:多くのフラックスは水溶性だが、洗浄には超音波洗浄機や洗浄液が不可欠。設備・薬液コスト増加。
- 環境・規制対応:後処理廃液はpH管理が必要で、産廃扱い。規制強化により廃棄コストが増大。
- 無洗浄タイプの制約:コスト高であり、耐熱性や接合強度が一般品よりも劣る場合がある。
4.5 環境・安全面の課題
- 有害ガス発生:フラックス燃焼時に発生するハロゲン化水素、酸化金属粒子などは局所排気装置が必須。
- 熱灼傷・火災リスク:高温部品・トーチ操作での火傷事故が多発。防護具(耐熱手袋、フェイスシールド)の徹底が必要。
- 作業環境管理:JIS Z 8802「金属作業環境対策」に準拠した換気・局所排気の設計が求められる。
5. メリット・デメリット比較表
分類 | メリット | デメリット |
---|---|---|
母材への影響 | ・熱影響部(HAZ)が狭小、熱歪み・硬度低下を50%抑制 ・寸法公差±0.01mm保持 ・材料組織変化抑制(ステンレス、超高強度鋼) | ・トーチ加熱では±20℃制御が困難 ・熟練者教育に3ヶ月~1年要 |
接合対象 | ・異種金属(鋼‐銅、ステンレス‐真鍮)で200MPa超の接合強度 ・電気・熱伝導性最適化(Cu–Pで熱抵抗0.1K/W) ・Ni基で耐食性向上 | ・タングステン、モリブデン等高融点材料は不適 ・厚板(t>10mm)や複合形状部品は加熱均一化が困難 |
気密性・水密性 | ・孔径1µm以下の微小クラック封止 ・真空ろうでリークレート10⁻¹⁰Pa·m³/s達成 | ・フラックス洗浄工程が必須 ・廃液pH管理が必要、産廃コスト増加 |
コスト | ・小規模設備で10万円台から開始可(トーチ) ・ガス消費量は溶接の60%、年間ランニングコスト20~50%削減 ・無人化ラインで月産5000個以上可能 | ・真空炉は数千万円規模 ・年間保守費数百万円 ・設置スペース・配管・排気設備で間接費増 |
生産性・品質 | ・インダクション加熱で毎分10サイクル対応 ・温度制御で強度CV5%以下、再現性高い ・真空無洗浄で後処理省略、納期20%短縮 | ・局所排気・安全設備の設計が必須 ・高温作業による火災・灼傷リスク |
外観・仕上がり | ・ビード幅2mm以下で美観良好(銅パイプ継手) ・グラインダー仕上げ不要で研磨工数30%削減 ・宝飾品で鏡面研磨前処理時間を1/3削減 | – |
6. 適材適所の実践ガイド
- 試作・小ロット生産
- 推奨方式:手はんだ、トーチろう付け
- 留意点:熟練者による作業「見える化」教育、ワークショップでのOJT
- 導入効果:初期投資10万円以下で1日10個程度の部品接合が可能。
- 量産・高品質ライン
- 推奨方式:真空炉中ろう付け、誘導加熱
- 留意点:プロファイル管理装置、IoT連携による⇆リアルタイム品質モニタリング
- 導入効果:月産10万個、接合不良率0.01%以下を達成。
- 高精度電子部品
- 推奨方式:リフロー炉+鉛フリーソフトはんだ
- 留意点:熱プロファイル最適化、PCB歪み抑制用フォークツール
- 導入効果:基板反り0.05mm以下、実装密度2倍化を実現。
- 異種金属複合構造
- 推奨方式:Agろう+フラックス選定(非塩素系無洗浄)
- 留意点:母材前処理(研磨+脱脂)、ろう材組成管理
- 導入効果:接合強度200MPa、耐熱・耐食性向上。
8. 環境対応・SDGsの観点からのろう付け
8.1 RoHS/REACH規制への対応
近年、電子機器や自動車部品では鉛フリーはんだやハロゲンフリーのフラックスが必須となっています。
- 鉛フリー合金の開発動向:Sn–Ag–Cu系合金に微量のビスマス(Bi)やインジウム(In)を添加することで、融点・機械的強度のバランスを最適化する取り組みが進行中。
- フラックスの代替技術:従来の塩素系フラックスから、VOC(揮発性有機化合物)を削減したノンシリコーンタイプや、完全無洗浄タイプへのシフトが加速。
8.2 エネルギー効率とCO₂排出削減
- 誘導加熱の高効率化:誘導加熱装置のコイル設計最適化と高周波インバータの省エネ制御により、溶接プロセス比で約30%の電力削減を実現。
- 廃熱回収システム:炉中ろう付けで発生する排熱をヒートポンプで回収し、社内冷暖房に再利用する事例では、年間でCO₂排出量を約15トン削減。
8.3 廃棄物低減・循環利用
- ろう材スクラップのリサイクル:端材やフラックス残渣を回収・再生炉で再融解し、ろう材として再生利用。再生率90%超を達成する工場も増加。
- 洗浄廃液の減容化:超臨界CO₂洗浄など先端技術を導入し、従来の水溶液洗浄に比べて廃棄液量を70%以上削減。
9. デジタル化・IoT導入による品質管理
9.1 リアルタイム温度プロファイルモニタリング
- センサ埋め込み加工:治具内に熱電対センサを内蔵し、各接合部の温度をリアルタイムで取得。
- クラウド連携:取得データをクラウドに蓄積し、AI解析で適正な加熱プロファイルを自動生成。接合強度のばらつきCVを従来の5%から2%以下に低減。
9.2 画像検査・AI外観検査
- 高解像度カメラ+ディープラーニング:接合部のビード形状や色調の偏差を学習し、リアルタイムで不良を検出。検査時間を従来比50%短縮し、検出精度を98%以上に向上。
- クラウドQAシステム:現場スマホから撮影した画像をQA部門が遠隔で承認・フィードバック。ライン停止時間の削減と技術継承を両立。
9.3 トレーサビリティと品質保証
- バーコード・RFID管理:部品ごとに接合条件(合金種、フラックス種、温度プロファイルID)を紐付け。万一の不良時も原因特定が迅速。
- 電子署名付きレポート生成:作業後すぐにPDF報告書を自動生成し、品質マネジメントシステム(QMS)に保存。ISO 9001やIATF 16949の監査対応をスムーズに。
10. 具体的トラブル事例と現場対策
事例 | 原因 | 対策 |
---|---|---|
A社:薄肉ステンレス管の密着不良 | フラックス塗布量不足、加熱温度ムラ | 自動ディスペンサー導入+治具冷却機構追加 |
B社:電子基板はんだクラック | リフロープロファイルのオーバーシュート | 熱風循環装置のファン回転制御+プロファイル最適化 |
C社:パイプ継手の漏れ | 銀ろうの浸透不良、母材切削面粗さ過大 | 切削後研磨によるRa値改善(Ra 0.4µm以下)+前処理強化 |
D社:大断面銅板の剥離 | 加熱速度過速、ろう材供給タイミング不適 | PLC連携による温度 ramp制御+ロボットによる一定供給 |
E社:宝飾品仕上げムラ | 人手によるトーチ操作差、人材間スキル差 | レーザーブレージング装置導入+マスターピースによる技能検証 |
11. 今後の展望と技術動向
- レーザーブレージングの普及
- レーザーによる局所加熱で、さらに狭いHAZと高速サイクルを実現。将来的にはロボット連携によるフレキシブル生産ラインが主流化。
- ナノ粒子強化ろう材
- 銀ナノ粒子添加により、溶融流動性と接合強度が向上。次世代半導体パッケージ向けに耐熱衝撃性が2倍に。
- グリーンフラックス技術
- 生分解性成分やバイオ由来酸化膜除去剤を活用し、廃液処理負荷をさらに軽減。2027年には市場シェア30%超を予測。
12. まとめと提言
- 技術選定の最適化:用途、量産規模、材料組成、環境規制を総合的に評価し、最適なろう材・加熱方式を選択すべきです。
- デジタル化投資の回収:IoT/AI導入により、不良率低減・エネルギー削減・納期短縮を同時に実現し、3年以内のROI達成が可能です。
- 人材育成と技能継承:高度化する技術に対応するため、熟練者の技術を見える化し、新人研修にAIアシストツールを活用することで、育成期間を短縮できます。
- 持続可能性の追求:環境対応製品・プロセスは、企業価値向上と規制対応の両面で競争力を強化します。グリーン認証を活用し、サプライチェーン全体でのSDGs達成に貢献しましょう。
本稿が、御社のろう付け技術導入・改善の一助となれば幸いです。ご不明点や詳細データのご相談はお気軽にお問い合わせください。