ろう付け加工について解説
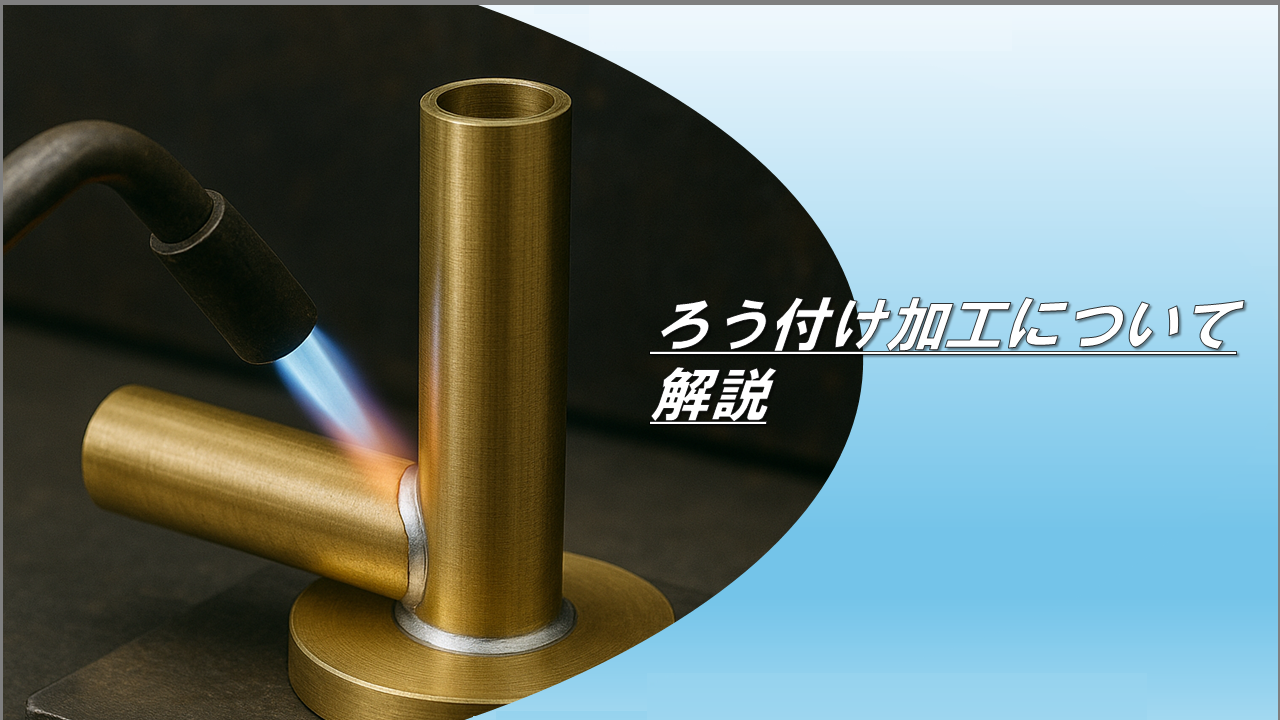
1. ろう付け(ブレージング)とは
ろう付け(ブレージング)とは、金属などの母材同士を加熱し、溶融したろう材(フィラー)を毛細管現象などを利用して接合部に流し込み、冷却後に金属接合を実現する加工方法の総称です。一般的に「はんだ付け」と呼ばれるものも広義のろう付けに含まれますが、融点温度によって区別されるケースが多く、摂氏450℃以上のろう材を使用する場合を「ブレージング(ろう付け)」、摂氏450℃未満のものを「ソルダリング(はんだ付け)」と呼ぶのが通例です。
ろう付けは、母材を直接溶融させて一体化させる溶接とは異なり、母材は溶けずにろう材(ブレージング材)だけが溶融し、母材と拡散・濡れ性によって接合を得る方法といえます。そのため、比較的低温で加工が行え、母材の物性を大きく変化させずに接合できるという利点があります。金属だけでなく、セラミックス・カーボン系材料の一部とも接合できる場合があり、電子部品や熱交換器、航空宇宙分野まで幅広い産業分野で活用されています。
2. ろう付けと溶接・はんだ付けの違い
2.1 ろう付けと溶接の比較
- 温度帯
ろう付けは融点の高いフィラーを溶かす場合でも通常600〜900℃程度が多く、チタンやニッケル系、高温合金同士の接合など特別な場合を除けば、溶接ほどの高温(1,000℃以上)にはならないことが多いです。 - 母材の溶融有無
ろう付けでは母材そのものを溶かさず、フィラー(ろう材)だけを溶かして接合します。一方、溶接は母材を溶かして融解プールを形成し、そこに溶接棒などを溶かし込むことで接合するため、母材の組織や特性に大きな影響が及びやすいです。 - 接合強度
一般的には溶接の方が接合強度は高くなるケースが多いですが、ろう付けでも十分に強度を得られる場合があります。特に部材の形状や接合面の面積、使用するろう材の種類などを最適化することで、実用的に耐えうる強度を確保できます。 - 応力集中とひずみ
ろう付けは溶接と比べて低温かつ局所的な溶融で済むため、熱的な歪みは少なくなります。また、母材が高温で大きく溶融しないため、溶接特有の熱影響部(HAZ)がほとんど生じず、脆化や金属組織の粗大化が抑えられます。
2.2 ろう付けとソルダリング(はんだ付け)の比較
- 温度帯
先述の通り、ろう付けは450℃以上、はんだ付けは450℃未満という大まかな分類があります。 - 用途
はんだ付けは主に電子基板上の部品の接合や小型部品の配線接合など、精密かつ比較的低い強度しか要求されない分野で多用されます。一方、ろう付けは配管や金属構造体、熱交換器、刃物・工具など機械的強度がある程度求められるものにも用いられます。 - フィラーの組成
はんだ付けで用いられるはんだは、錫(Sn)を主成分とした合金(Sn-Pb、Sn-Ag-Cuなど)が主流です。一方、ろう付けでは銀ろう(Ag-Cu合金)、銅ろう、アルミろう、ニッケルろうなど、母材や用途に応じてさまざまな合金が使われます。
3. ろう付けに用いられる主なろう材(フィラー)
ろう材は接合部の強度や耐食性、作業性に大きく影響します。用途や母材の材料、要求特性によって選定が必要です。以下は代表的なろう材です。
- 銀ろう(Agろう)
- 一般的に広く用いられるろう材。銀と銅に亜鉛やカドミウムなどを添加した合金が多い。
- 融点が比較的低く、濡れ性が良好で作業しやすい。
- 輝く外観で、アクセサリーや美術工芸分野でも使用される。
- 高価ではあるが、接合強度・展延性も高く、汎用性が高い。
- 銅ろう(Cuろう)
- 真鍮(銅+亜鉛)を主体とした黄銅系のろう材や、リン銅ろうなどを含む。
- 銀ろうよりも安価で、主に鉄鋼材料の配管や機械部品のろう付けに使用される。
- 融点は銀ろうよりやや高めだが、溶けた後の流動性は良好。
- リン入りの銅ろうは、ろう付け過程で自力で脱酸作用を持ち、一部の場合ではフラックス不要で作業できる。
- アルミろう
- アルミニウムを主体とした母材同士を接合するための合金ろう。
- アルミニウムは酸化膜が非常に安定しているため、ろう付けには専用のフラックスや真空ろう付けなどが用いられることが多い。
- 熱伝導率が高いため、局所加熱よりも大きな熱源が求められる場合もある。
- ニッケルろう・コバルトろう
- 高温強度や耐酸化性が求められる航空宇宙分野やガスタービンなどに使用される。
- 融点が1,000℃を超えるものもあり、真空炉や制御雰囲気炉を用いたろう付けが一般的。
- 母材との冶金的相性を考慮し、ニッケル基・コバルト基合金を使い分ける。
4. ろう付けにおけるフラックスの役割
ろう付けにおいては、母材やろう材が加熱されると表面に酸化物や不純物が生成しやすく、これらがろう材と母材の濡れ性を阻害してしまいます。そこで**フラックス(溶剤)**を使用し、酸化物の除去や生成の防止、表面の清浄化を行うことが必要となります。
- 主要成分
ほとんどのろう付け用フラックスはホウ酸塩、フッ化物、塩化物などを含み、酸化物を化学反応で溶解したり、揮発成分として排出する役割を担います。 - 塗布方法
ペースト状、液状、粉末状などさまざまな形態があり、接合部に直接塗布したり、ろう材にあらかじめ塗布しておく場合もあります。 - 温度特性
ろう付け作業の温度範囲で最も効果的に作用するよう設計されており、温度が上がるにつれ酸化物を除去し、ろう材が溶融する際に邪魔にならないようにする必要があります。 - 後処理
ろう付け後のフラックス残渣は腐食の原因となることがあるため、洗浄など適切な後処理が欠かせません。ただし、リン銅ろうなど一部のろう材では、フラックスを使用しなくても自己脱酸作用によりろう付けが可能な場合があります。
5. ろう付けの基本プロセス
ろう付けを行う際の基本的なステップを順番に示します。実際の現場では設備や母材の種類によって一部省略・追加されることもありますが、ここでは汎用的なプロセスを紹介します。
- 接合面の準備
- 接合部の清掃(油分や汚れの除去)
- 酸化物やサビがある場合は研磨などで除去
- 最適な隙間を確保(ろう材の毛細管現象で十分に流れ込むように)
- ろう材・フラックスの選定と塗布
- 母材と用途に適したろう材とフラックスを用意
- フラックスを接合面またはろう材に塗布
- 加熱
- トーチ(酸素-アセチレンなど)や高周波誘導加熱、電気炉など、用途に合わせた加熱方法を選ぶ
- 必要な温度に達するまで慎重に加熱し、過熱による酸化や母材劣化を防ぐ
- ろう材の溶融と流動
- ろう材が溶融温度に達すると、毛細管作用で接合面に広がる
- 十分にろう材が回りきるように、接合部に均一に熱を与える
- 冷却と後処理
- ろう材が所定の温度まで冷却されると、接合部が固まる
- フラックス残渣などを洗浄したり、表面処理を行う
- 仕上げ・検査を実施(外観検査、場合によっては非破壊検査など)
6. ろう付けに用いられる主な手法
ろう付けにはさまざまな実施方法がありますが、以下に代表的なものを示します。
6.1 トーチろう付け(ブロウバーナーろう付け)
酸素-アセチレンバーナーなどを使用し、局所的に炎で加熱しながらろう材を溶かす方法です。配管や小規模部品のろう付けに多用されます。手動で行うため作業者の熟練度に左右される部分があり、均一な加熱を保つためには経験が必要です。しかし、設備コストが低く、装置の持ち運びも容易であるため、幅広い現場で利用されます。
6.2 炉中ろう付け
電気炉やガス炉などの炉内部で、雰囲気を制御しながら一括で複数の部品をろう付けする方法です。真空炉ろう付けと呼ばれる方法も含まれ、特に高温強度が求められるニッケル基合金や、アルミニウムのろう付けに多用されます。雰囲気ガスを不活性ガス(アルゴンやヘリウム)にしたり、真空状態にすることで酸化を抑え、フラックスを使用せずに高品質な接合を得られるメリットがあります。大量生産向けの自動化工程にも適しています。
6.3 誘導加熱ろう付け
高周波誘導コイルを用いて母材そのものを発熱させ、接合部を加熱する方法です。高周波電源を調整することで、比較的均一な加熱が得られるほか、接合部だけを選択的に加熱できるメリットがあります。局所加熱が可能なため、変形や熱影響を抑えやすいという特徴があります。自動化ラインでも採用され、電子部品や自動車部品のろう付けなどに応用されています。
6.4 レーザーろう付け
レーザーを熱源として、狭い範囲を集中的に加熱する方法です。非常に小さなスポットに高エネルギーを照射できるため、微細加工や高精度な部品に適しています。反射率の高い材料(アルミや銅など)では、レーザーの選択が重要になりますが、自動車の車体パネルの接合工程などでレーザーろう付けが利用される例もあります。
6.5 超音波ろう付け(はんだ付け含む)
超音波の振動エネルギーを利用しながらろう材の濡れ性を向上させ、フラックスなしで酸化膜を破壊して接合する手法です。特にアルミニウムやマグネシウムなど、酸化膜が強固な材料をろう付け・はんだ付けする場合に有効とされています。ただし、設備投資がやや高価となるケースが多いです。
7. ろう付け接合部の品質評価
ろう付け後の接合部は、部品としての使用に耐えられる品質が必要です。下記の方法で評価・検査されることが多いです。
- 外観検査
- ろう材のはみ出しや隙間の有無、フラックス残りなどを目視や拡大鏡で確認。
- 均一なろう回りがあるか、母材との段差やおうとつがないかを見る。
- 非破壊検査
- 浸透探傷検査(PT)や放射線透過検査(RT)で内部欠陥(ボイド、気孔、割れなど)を検出。
- 超音波探傷検査(UT)は、ろう付け厚みが薄い場合は感度や分解能に注意が必要。
- 機械試験
- 剪断試験、引張試験、曲げ試験などで接合強度を数値化。
- 母材が先に破断する場合は、ろう付け自体の強度は十分とみなせる。
- 金相観察
- 断面を研磨・エッチングして顕微鏡で組織を観察。
- ろう材と母材の界面での拡散状況や脆性相の有無を評価。
8. ろう付け加工が活用される主な産業分野
- 電子・電気部品
- プリント基板やコネクタのはんだ付けはもちろん、センサーやリレーなどのユニットをろう付けするケースもある。
- 銅や金、銀メッキなど多種多様な材料が使われるため、最適なろう材や工程の選択が重要。
- 自動車産業
- ラジエーターやオイルクーラーなどの熱交換器では、アルミ真空ろう付けが広く用いられる。
- スチール・ステンレス部品のろう付けも行われ、排気系部品などにも適用されるケースがある。
- 近年は軽量化と高機能化の要請が強く、アルミ部品のろう付け技術がさらに発展している。
- 航空・宇宙分野
- タービンブレードやジェットエンジン部品など、高温環境下で使用される高性能合金の接合に真空ろう付けやニッケルろうが使われる。
- セラミックスと金属の接合や、超合金同士のろう付けなど、高い技術力を要する領域。
- 医療機器・精密機器
- ステンレスやチタンなどの生体適合性金属を用いたデバイスを、ろう付けで加工する場面がある。
- 極めて小さな部品や細管などを精密に接合できるため、工程の安定度が重視される。
- 建築・配管
- 冷却水や冷媒配管、ガス管の接合に銅ろうや銀ろうを使うケースは非常に多い。
- 高いシール性と必要十分な機械的強度が得られるため、長年にわたって安定した性能が期待される。
- 工具・刃物
- 超硬チップとスチールの接合など、切削工具や穴あけ工具でろう付けが利用される。
- ろう付け後の熱処理や研磨が必要になる場合があるが、強固な接合によって工具寿命を延ばせる。
9. ろう付け加工のメリットとデメリット
9.1 メリット
- 低温での接合
母材を大きく溶融させないため、溶接と比べて母材の特性変化や歪みが少なく、精度の高い組立が可能。 - 異種材料の接合が容易
融点や熱膨張率が異なる金属間でも、適切なろう材を選ぶことで接合可能。場合によっては金属とセラミックスなど異種材間接合も可能。 - 仕上がりがきれい
溶接のようにビードが大きく盛り上がることがなく、仕上がり外観が良好な場合が多い。また、隙間にろう材が流れ込むため、内面の段差も比較的少ない。 - 大面積の接合が可能
ブラケットや薄板同士の大面積接合にも向き、均一なろう回りが得られれば気密・液密性にも優れる。
9.2 デメリット
- 接合強度が溶接より劣る場合が多い
一般的には母材を完全に溶かして融合させる溶接のほうが強度や耐熱性は高くなることが多く、高負荷の構造物では適用が難しい場合がある。 - ろう材の選択やフラックス管理が煩雑
母材に合わせて適切なろう材とフラックスを使わないと、十分な濡れ性や強度が得られない。フラックスが残ると腐食の原因となる。 - 作業者の熟練度が必要
とくに手作業ろう付けでは、温度管理やろう材の流し込みのタイミングなど、コツを習得する必要がある。 - 高コストなろう材もある
銀ろうやニッケルろうなどは原材料コストが高く、大量生産品ではコスト増につながる可能性がある。
10. ろう付け加工時の安全面・環境面
- 防護具の着用
- トーチろう付けの場合は火炎により火傷や火災のリスクがあるため、耐熱手袋や保護眼鏡、難燃性の作業服が必要。
- フラックスやろう材から発生する有害ガスや煙を吸わないよう、局所排気装置やマスクを装着する。
- 火災防止
- 可燃物が近くにある環境でのトーチろう付けは火災の危険が高い。
- バーナー火の取り扱いには十分注意し、周囲を整理した上で作業する。
- フラックスやろう材の有害性
- 一部のフラックスにはフッ化物や塩化物が含まれており、吸入すると気道障害を起こす可能性がある。
- 銀ろうに含まれるカドミウムは有毒性が高いため、現在ではカドミウムフリーのろう材に切り替える動きが主流。
- 排気・廃液処理
- ろう付け後の洗浄液やフラックス残渣の処理は、適切に行わないと環境汚染のリスクがある。
- 産業廃棄物として区分管理し、法令に基づいた処理を行う。
- 作業環境の整備
- 炉中ろう付けや真空ろう付けでは、高温炉の取り扱いや真空ポンプの扱いなど、安全教育や定期点検が必須。
- 自動化ラインやロボットを導入する場合は、緊急停止装置や光学センサーなど安全装置を適切に設置する。
11. ろう付け技術の最新動向と今後の展望
- フラックスフリーへの取り組み
真空炉や制御雰囲気下での炉中ろう付け技術が進歩し、フラックスを使わずに高品質の接合が可能になりつつあります。これにより、フラックス残渣処理コストや環境負荷の軽減が期待されています。 - ロボット・自動化の導入
トーチろう付けのような手作業をロボット化し、作業の均一化・効率化を狙う動きが広がっています。とくに誘導加熱やレーザーろう付けは自動制御との相性が良く、生産ラインへの組み込みが増加しています。 - 新素材・複合材料への対応
炭素繊維強化樹脂(CFRP)や金属-樹脂ハイブリッド材料など、新素材の普及が進む中、それらと金属を組み合わせる接合技術の研究が行われています。ろう付けの場合、母材を溶融させないため、材料損傷を最小限に抑えつつ複合化する手法として期待されています。 - ハイエントロピー合金など先進合金のろう付け
多元素を組み合わせたハイエントロピー合金など、高強度・高耐熱性材料の研究開発が進むにつれ、それらを接合するためのろう材・フラックスの開発も進んでいます。高温耐性のあるニッケル基・コバルト基ろう材だけでなく、新たな合金の検討が進められています。 - レーザー3Dプリンタとの組み合わせ
レーザー積層造形(AM)で製造した部品の仕上げや、追加パーツの接合をろう付けで行うケースが模索されています。溶接を使うと母材の冶金学的特性が大きく変わる恐れがありますが、ろう付けなら比較的低温で局所的に接合できる利点があります。
12. まとめ
ろう付け加工は、母材を溶融させないという点が大きな特徴であり、そのおかげで異種材料や繊細な構造にも適用できる強みを持ちます。電子・電気部品のはんだ付けから航空宇宙分野の高温合金の接合に至るまで、幅広い産業界で欠かせない技術となっています。
他の接合方法(溶接や機械的締結など)と比較すると、ろう付けは「接合強度が若干劣るのではないか」というイメージがあるかもしれません。しかし、実際には接合条件や設計によっては、高い信頼性と十分な機械的強度を得ることができます。ろう付けには適したろう材の選択やフラックスの管理、適切な加熱方法など、ポイントをきちんと押さえることが成功の鍵となるでしょう。
さらに近年では、真空炉や誘導加熱、レーザー加熱など、ろう付けのプロセスを高度に制御・自動化する技術が発展してきました。これにより、生産性や品質が格段に向上するとともに、フラックスの無害化や省資源化といった環境対応も進んでいます。
総じて、ろう付けは「低温接合」「異種材接合」「高い気密性・液密性」「美しい仕上がり」「比較的安定した品質」といった特長を併せ持つ有効な接合技術です。機械、電気、建築、自動車、航空宇宙など、あらゆる分野で必要とされており、その応用範囲はますます広がり続けています。ろう材やフラックス、加熱方法の多様化により、これまでは難しいとされていた材料や大型部品の接合、あるいは複雑形状への対応も可能になり、技術開発が進むほどに新たな応用が生まれています。
今後も、軽量化ニーズの高まりや先進材料の開発が加速する中で、ろう付け加工の役割はさらに重要性を増していくことでしょう。設計段階から接合方法を考慮し、ろう付けの優位性を最大限に引き出すことで、部品の高性能化や効率的な量産を実現できる可能性があります。製造業に携わる技術者にとっては、ろう付け加工の原理と実践をしっかりと理解し、最新動向をキャッチアップしていくことが不可欠です。
また、環境負荷低減や安全性に配慮した技術も今後さらに求められるようになるでしょう。ろう付けの分野でも、フラックスレスろう付けや低融点で有毒元素を含まないろう材の研究が続けられており、社会的責任や法規制への対応といった視点でもイノベーションが期待されています。
ろう付けは一見地味に思われがちな技術ですが、製品の品質や信頼性に直結する極めて重要なプロセスです。本記事を通じて、ろう付けの基礎から応用、そして将来展望までの概要をつかんでいただければ幸いです。今後は実際に現場で使用するろう材のメーカー情報や、具体的なフラックスの種類、装置のスペックなどを照らし合わせることで、実践的な知識を深めていただければと思います。