真鍮切削で高精度を実現するコツ~精密加工を成功に導くための実践ポイント~
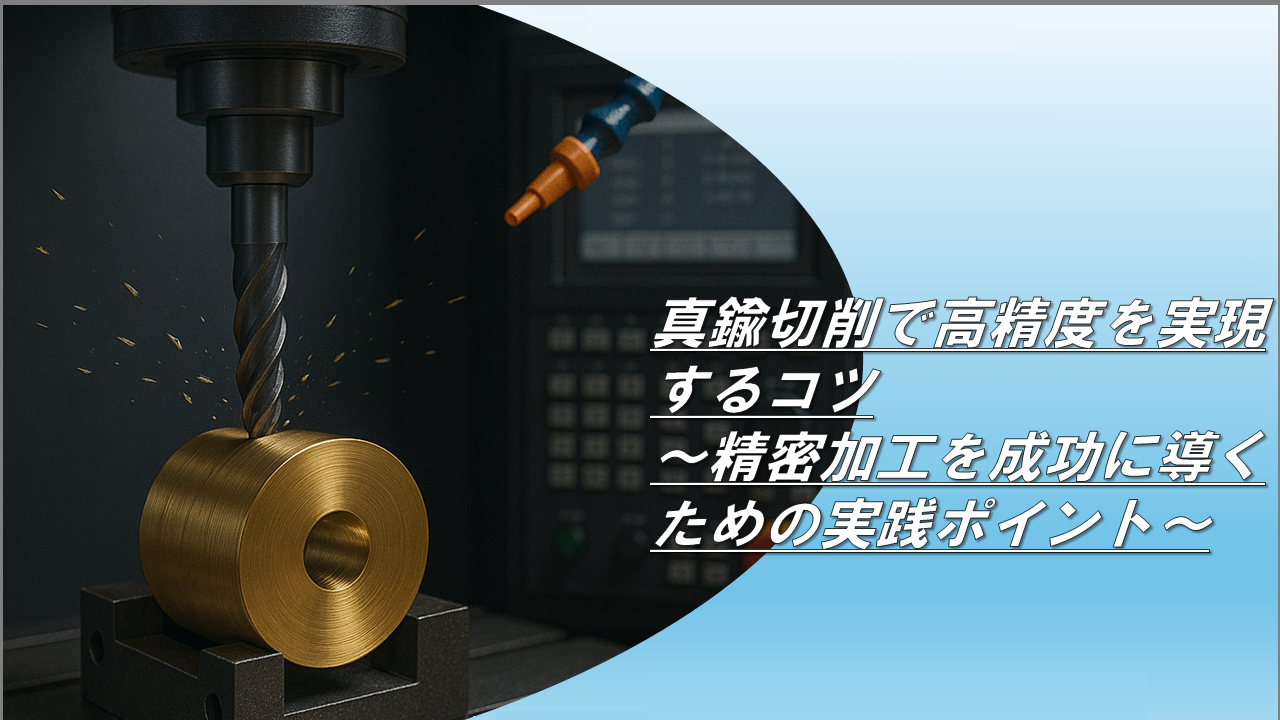
真鍮(ブラス)は、優れた切削性と美しい外観を兼ね備えた材料であり、精密部品や装飾品、電子部品などさまざまな分野で使用されています。とはいえ、どれだけ切削性に優れていても「高精度」が求められる現場では、細心の注意と最適な条件設定が必要です。この記事では、真鍮の切削加工において高精度を実現するためのコツを、段階的に解説していきます。
1. 材料の選定:快削材と一般材の違いを理解する
● 快削黄銅(C3604)の活用
真鍮にも複数の種類があり、特に高精度切削に適しているのは**快削黄銅(C3604など)**です。これは鉛を添加しており、切削抵抗が低く、寸法精度も出しやすい材料です。複雑な加工や連続生産にも適しています。
● 一般黄銅(C2801など)の注意点
一方で、C2801(七三黄銅)などは快削性は落ちますが、強度や耐食性に優れた特性を持ちます。こうした材料を使う場合は、切削条件の最適化や工具寿命管理が重要となります。
2. 工具の選定と管理
● 超硬工具の使用
高精度を求めるなら超硬エンドミルやバイトの使用が基本です。ハイス工具でも加工は可能ですが、刃先の摩耗が早く、寸法ばらつきが生じやすくなります。
● 刃先Rや逃げ角の工夫
真鍮は加工性が高い分、「逃げ角が小さい」と切りくずが詰まりやすくバリが発生しがちです。逃げ角は10°程度、刃先Rも0.2~0.4mmの微小半径にすることで、安定した切削が可能です。
● 工具摩耗のモニタリング
精密加工では、寸法変化の原因の多くが刃先摩耗に起因します。ツールプリセッターや画像測定機で刃先状態を定期確認し、交換タイミングを数値管理することが推奨されます。
3. 加工条件の最適化
● 低切込み・高送りのバランス
真鍮は軟らかく切削性に優れている反面、切削抵抗が小さくて工具の跳ねが起きやすいという特性があります。そのため、切込みは浅く、送りはやや速めに設定することで「安定した切削」と「寸法安定性」の両立が可能です。
項目 | 推奨値(参考) |
---|---|
切削速度(Vc) | 100~200 m/min |
切込み深さ(ap) | 0.2~0.5 mm |
送り速度(f) | 0.05~0.2 mm/rev |
● 切削油の選定
ドライでも加工可能な真鍮ですが、高精度を求めるならミストやオイルを使用するのが望ましいです。工具寿命延長や面粗さ改善にも効果があります。
4. 工作機械と芯出しの精度
● 静的精度と動的精度の把握
どれだけ工具や条件が優れていても、工作機械の剛性・主軸精度が低ければ高精度加工は不可能です。特に**回転軸の振れ精度(振れ精度0.003mm以下)**は真鍮加工において非常に重要です。
● 芯出しとワーク固定
芯出しミスは寸法精度・面粗さに直結します。ワークは高剛性のバイスや治具で固定し、センター出しはダイヤルゲージで±0.01mm以内に抑えることが基本です。
5. 加工後の測定と評価
● 三次元測定機の活用
真鍮部品は細かい寸法公差が要求されることが多いため、ノギスやマイクロメーターだけでなく三次元測定機や光学式測定機による確認が不可欠です。
● SPC管理でばらつきを抑制
量産現場では**SPC(統計的工程管理)**を導入し、連続加工による寸法ばらつきを事前に検出・補正する体制づくりが重要です。
6. 真鍮特有のトラブル対策
真鍮は加工性が高い材料として知られていますが、その一方で加工中に特有のトラブルが発生しやすい素材でもあります。高精度加工を妨げる要因として代表的なのが、「バリの発生」「かえり(返りバリ)」「切りくずの絡まり」「寸法ばらつきの再発」「熱による軟化現象」などです。ここでは、これらの問題に対する実践的かつ効果的な対策を詳しく紹介します。
6-1. バリ・かえり(返りバリ)の抑制対策
■ 問題点
真鍮は延性が高いため、切削時に材料が引き延ばされ、刃先から離れる瞬間に微細なバリやかえりが発生しやすいです。これが寸法誤差や組立不良、導通不良(電子部品の場合)を引き起こす原因となります。
■ 対策方法
対策項目 | 具体的方法 |
---|---|
工具の選定 | シャープエッジではなく小R付きの工具を使用し、滑らかな切断を実現 |
加工パスの工夫 | 最後の仕上げパスで逆回転仕上げや送り速度の低速化を実施 |
自動面取り | NCプログラム内で**面取り処理(C0.2~C0.5)**を組み込む |
専用工具 | バリ取り専用のスピンドル型デバリングツールやロータリーバレルを併用 |
加工後処理 | 超音波洗浄や**バレル研磨(湿式・乾式)**によって微細バリを除去 |
6-2. 切りくずの絡まり・詰まり対策
■ 問題点
真鍮の切りくずは短くて折れやすいものの、高速加工や小径工具使用時にはスパイラル状に絡まりやすく、刃先やワークに付着することがあります。この現象は表面粗さの劣化・寸法不良・工具破損の原因にもなります。
■ 対策方法
- チップブレーカ付き工具を使用し、切りくずを短く折る
- **加工方向を工夫(上から下へ切り逃がす)**し、重力を利用
- エアブローやミスト冷却を併用して切りくずを即座に排除
- 定期的な機内清掃をルーチン化
- チップコンベア・フィルターのメンテナンスを怠らない
特に自動旋盤や小型マシニングセンタでの連続運転では、切りくずトラブルによる停止は大きなロスとなります。加工時間ごとに自動エアブローを組み込むのも有効です。
6-3. 寸法ばらつき・熱による寸法変化への対応
■ 問題点
真鍮は熱伝導率が高く、加工熱が一時的に工具やワークに蓄積すると微小な熱膨張が起こり、寸法誤差が発生することがあります。特に連続加工や深穴加工で顕著です。
■ 対策方法
- **インターバル加工(時間を空けて熱放散)**を計画的に入れる
- 機械温度管理(定常温になるまで加工しない)
- 冷却液を局所に集中噴射し、熱影響を局限化
- 測定時の時間を固定(加工後一定時間後に測定)
- SPC(統計的工程管理)による傾向分析でリアルタイム補正
6-4. 表面のにじみ・変色対策
■ 問題点
真鍮は銅合金であるため、加工中の**摩擦熱や空気中の硫黄成分との反応により変色(酸化・黒ずみ)**が生じることがあります。これは外観部品や端子にとって重大な品質問題です。
■ 対策方法
製品用途によってはニッケルメッキやクロムメッキ処理を前提に設計
無添加の低硫黄切削油や防錆剤を選定する
加工後すぐに脱脂洗浄・乾燥処理
真空保管または窒素封入保管で変色を抑制
● バリ・かえり対策
真鍮は延性が高いため、切断面にかえりやバリが生じやすいです。対策としては以下のような方法があります:
- シャープエッジではなく小R加工
- 加工後の面取り工具(NCデバリング)
- 超音波洗浄+バレル研磨による仕上げ
● 切りくず処理
真鍮切りくずは細かく絡まりやすいため、機内清掃・チップコンベアの定期点検も高精度加工の安定運用には不可欠です。
まとめ
高精度な真鍮切削加工を実現するには、以下の6点がカギとなります:
- 適材適所の材料選定(特にC3604)
- 高精度な工具と適切な刃形設計
- 切削条件の最適バランス調整
- 芯出し精度と機械剛性の確保
- 精密な測定とSPCによる管理
- 真鍮特有のトラブル対策(バリ・切りくず)
真鍮は切削性が高いため「簡単に加工できる」と思われがちですが、高精度を求める加工では非常に繊細な対応が求められます。上記のポイントを押さえることで、再現性のある寸法精度と美しい加工面を実現できます。